When disruptive events affected supply chains, prior to the 2020 corona virus pandemic, finding a solution was much easier. It wasn't the norm to have multiple disruptions on a global scale happening simultaneously—so finding a new supplier for spare parts for the production line wasn't an insurmountable task. Theoretical supply chain “resilience” could then be achieved with traditional procurement practices and risk management frameworks.
Today, supply chain disruptions continue to occur with ever-increasing frequency and with less predictable magnitudes. For manufacturers relying on yesterday's traditional supply chain management strategies, the combination of a disruptive event with the need for even a simple spare part can easily result in extended production line downtime.
So, in today's world of uncertain availability, how can manufacturers keep their manufacturing plants up and running? While traditional just-in-time (JIT) supply chain management models are inherently too stretched and fragile to succeed in the face of constant uncertainty, today's advanced additive manufacturing technologies have evolved to add resilience through greater flexibility .
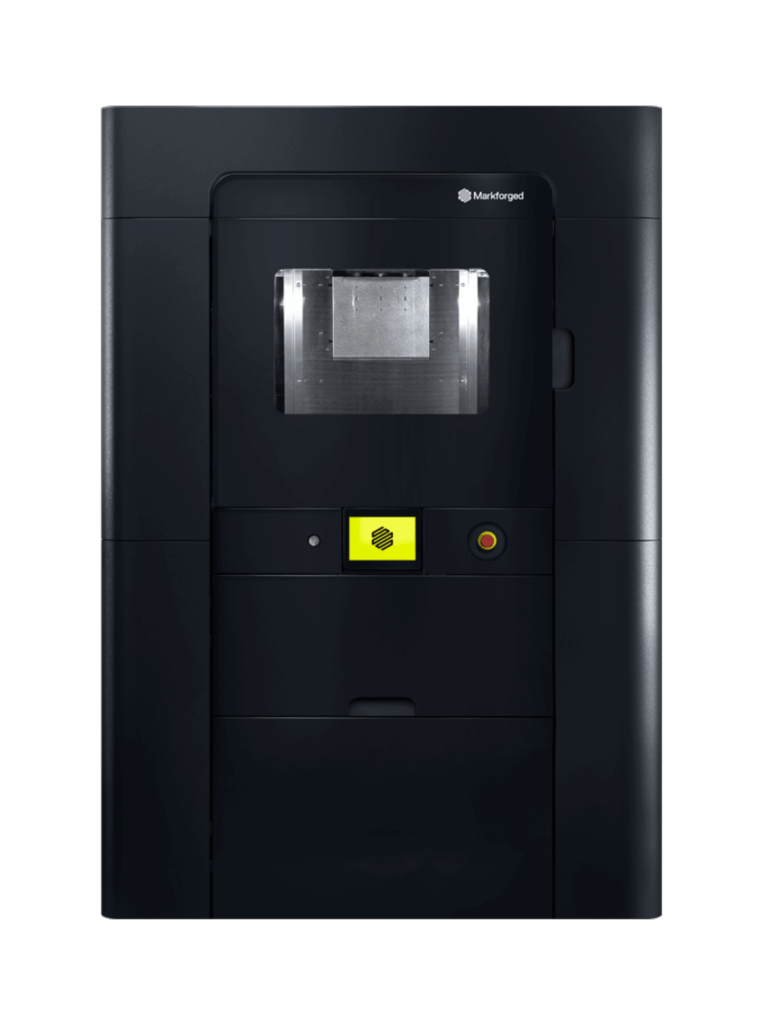
By providing manufacturing capabilities at the point of need for everything that keeps factories running—high-performance spare parts, manufacturing tools and fixtures, MRO parts, or ergonomic equipment—today's industrial 3D printers can provide powerful new autonomy to supply chain operators.
Read this article to learn why today's unpredictable world demands new ways to build supply chain resilience—and why manufacturers around the world are turning to 3D printing to keep production lines running through a new era defined by uncertainty.
Supply Chain Status Quo: Just-in-Time Parts Delivery
Since 1970, the world has trusted JIT manufacturing. Under optimal conditions, this model is efficient, minimizing excess overhead by producing only inventory levels necessary to meet customer demand.
As the efficiency of JIT manufacturing has brought this philosophy to widespread practice in factories around the world, most manufacturers have modeled their supply chain management strategies on a JIT approach—meaning they only order materials and other components from upstream suppliers just before they are needed while ordering slightly more than the exact quantity needed at that moment.
Until before 2020, supply chains were easier to manage. While destructive events still occurred, they tended to be more predictable in scale, easier to contain at these smaller magnitudes. As a result, traditional risk management frameworks were sufficient mitigation.
Today's Supply Chain Landscape: Can You Plan For It?
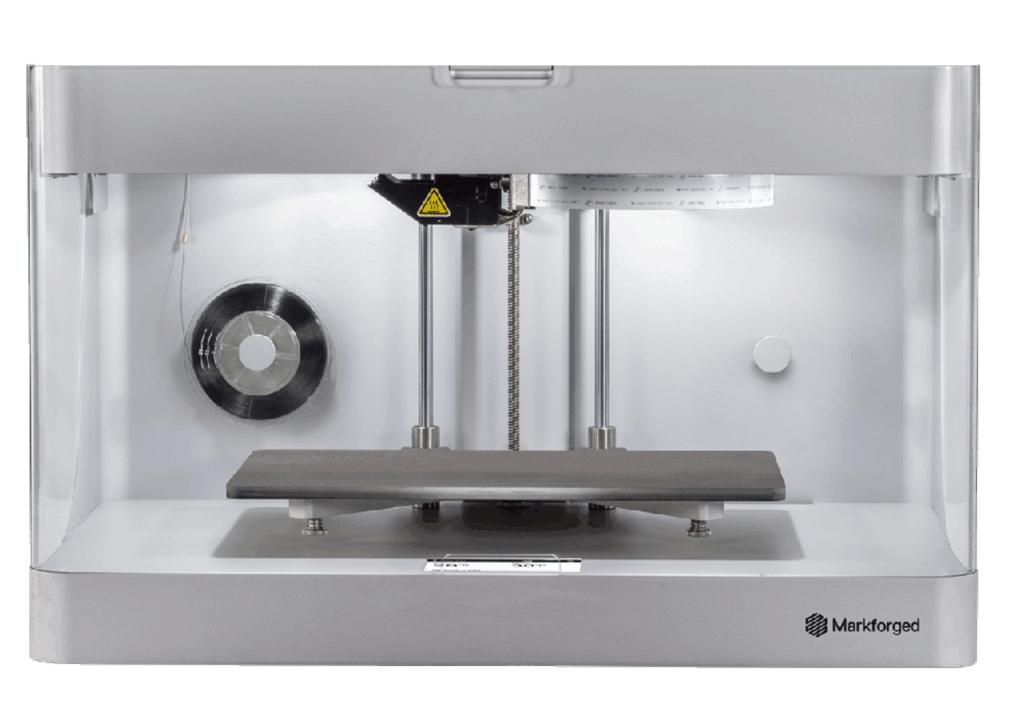
While manufacturers have historically managed supply chain disruptions through comprehensive risk mitigation plans, the theoretical “resilience” of these supply chains is built on assumptions that their impacts can be consistently planned for and addressed.
However, when we consider what specific factors and variables ultimately affect and limit the availability of large parts of global supply chains – can manufacturers accurately track, predict and plan for large-scale geopolitical changes far beyond their control? The factors behind these large-scale disruptions tend to unfold behind the scenes. They are invisible until the catastrophic impact has already materialized, blinding supply chains and upending them.
Supply chains are complex, with countless variables and overlapping dependencies. A disruptive event at any single point in these interconnected networks can have unpredictable ripple effects that ultimately lead to the ultimate failure of multiple other supply chains.
In the new status quo of uncertainty the supply chain model of JIT is vulnerable to these disturbances. JIT relies on lean inventories and precise coordination between suppliers and manufacturers. When the impact of disruptions cascades across entire vendor ecosystems, solutions are not as simple as having clear contingency plans in place. No large inventories to rely on – or fast and flexible manufacturing available in the point of necessity – these production facilities are susceptible to extended periods of costly downtime. A spare part that can take months to receive can stop an entire production line until it is received.
Building Supply Chain Resilience Today: Manufacturing at the Point of Need (point of need) adds more flexibility
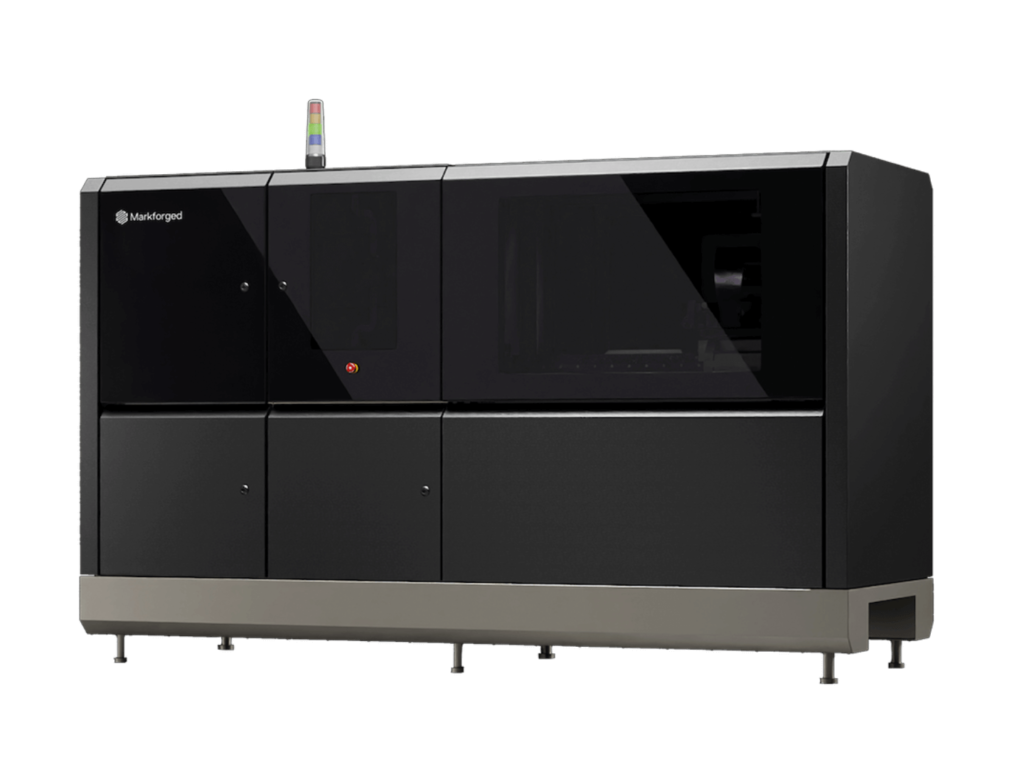
Constantly reassessing supply networks is not a bulletproof solution. Not only does identifying and integrating new suppliers into existing systems take valuable time and resources; but the greater frequency of disruptive events makes constant re-planning of complex, interconnected manufacturing supply chains unviable as a long-term strategy.
Therefore, manufacturers looking for a more reliable buffer against disruptions in factory operations must shift their supply chain approaches to a more nimble and flexible strategy. So what can manufacturers do to acquire critical spare parts without jeopardizing production operations with uncertainty and unnecessarily long lead times?
As federal initiatives like AM Forward highlight the transformational value of cutting-edge technologies like additive manufacturing in supply chain management, a growing number of organizations have brought industrial 3D printing into their factory facilities to aid operations.
Modern additive manufacturing technology is capable of rapidly producing production-grade parts from metal-strength composite materials and a wide variety of industrial metals. When problems arise, technicians can quickly and easily print the solutions they need now on the shop/floor/plant – tools and fixtures, MRO equipment, ergonomic solutions or any other critical production components – without extended downtime.
3D printing ultimately means you have flexibility in your supply chains without having to duplicate physical inventory. Instead of keeping spare parts in stock, parts can be stored in the cloud as digital inventory – which can then be printed into a tangible part in a matter of hours.
With much higher levels of risk and uncertainty almost a constant in today's supply chains, the ability to design and print a solution to any challenge that arises provides autonomy and control of production facilities in today's world of volatile supply chains – instead of waiting weeks or even months for a critical part to arrive.
How additive manufacturing builds supply chain resilience
Point-of-need manufacturing through industrial 3D printing provides sustainability to manufacturers' supply chains in several ways:
- Reduced dependence on traditional suppliers: AM allows manufacturers to produce parts and components in-house, reducing their dependence on outside suppliers. If there are disruptions to existing supply chains, factory staff are empowered to take matters into their own hands by designing and 3D printing a solution.
- Production on demand: With 3D printing, manufacturers can produce items on demand, eliminating the need for large inventories and minimizing the risk of excess inventory.
- Digital inventory: This allows parts to be stored in the cloud as 3D design files, which can then be turned into tangible objects in a matter of hours. This flexibility allows manufacturers to respond quickly to changes in demand or unexpected disruptions in the supply chain.
With today's more sophisticated 3D printing software platforms, major industrial manufacturers like Vestas use secure digital inventories to store certified parts with up-to-date specifications that can be easily searched and printed wherever they are needed. A secure shared repository of part files with up-to-date specifications allows them to be transferred without risk of design inconsistencies or risk of intellectual property leakage. - Localization of production: 3D printing allows manufacturers to establish production facilities closer to customers. This localization reduces transportation costs, delivery times, and mitigates the impact of potential disruptions associated with long-distance shipping.
- Availability of spare parts: 3D printing can address the challenge of spare parts availability, especially for older or discontinued parts. Instead of relying on the availability of spare parts from suppliers and working with their deadlines, manufacturers can produce the necessary parts on demand using 3D printing, reducing factory downtime.
- Distributed production networks: 3D printing enables the creation of distributed manufacturing networks, where multiple facilities can collaborate and share production capacity. In the event of an outage at one location, production can be moved to other facilities within the network, ensuring continuity and reducing the impact of supply chain disruptions.
The Digital Forge: Designed to Maximize the Value of Supply Chains
For today's state of uncertainty, Markforged has developed a suite of uniquely powerful 3D printers and software tools to maximize the value manufacturers can generate from their supply chains.
Cashco Inc. uses Markforged composite 3D printers to print custom tools for the factory floor. This reduced tooling production time with the 70%—while also reducing the need to work with metal tooling with the 90%, freeing up internal machine bandwidth for revenue-generating parts.
Vestas , a world leader in wind energy, stores over 2,000 parts as a cloud-based digital inventory through Markforged Eiger software. Employees at any Vestas location can quickly search and 3D print any parts with up-to-date specifications for qualified applications. With its distributed manufacturing model, Vestas can get parts at a moment's notice anywhere in the world, in just hours.
KST Moschkau turned to the additive at Digital Forge when small-quantity orders for aluminum components became expensive and often created delays with long lead times. 3D printing prototypes and final production parts for a security camera mount cut lead time from 3-4 weeks to just 2 days; with production costs only ⅙ of the previous ones.
0 Comments