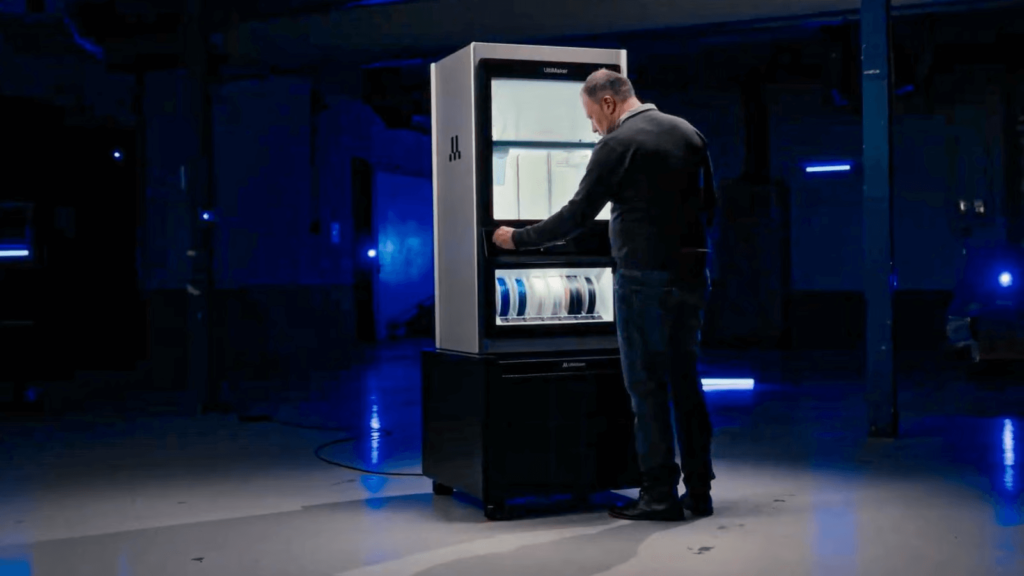
UltiMaker Industrial - UltiMaker Factor 4
UltiMaker's new FDM 3D printer aims to bridge the 3D printing gap between consumer and industrial machines, combining ease of use with engineering-grade materials.
Creating FDM 3D printers since 2011, UltiMaker says that the latest – Factor 4 – is the most “robust” and “reliable” yet, aimed at helping companies overcome the barriers to in-house manufacturing of low-volume end-use tools and parts.
Preferred by industrial design firms, universities and architects for visual and functional prototyping, the machines UltiMaker have a reputation for reliable printing and consistency.
Factor 4, which has been in development for years, is a new path for UltiMaker, challenging companies like Stratasys and Markforged to produce "light industry" tooling, small-run replacement parts, and end-use components. UltiMaker apparently wants to move out of the studio and into the shop/production lines.
"why" Factor 4, as All3DP's lead product engineer Andrea Gasperini explained it - "to provide a complete application solution - a 360-degree offering - that meets as many needs as possible in the manufacturing industry."
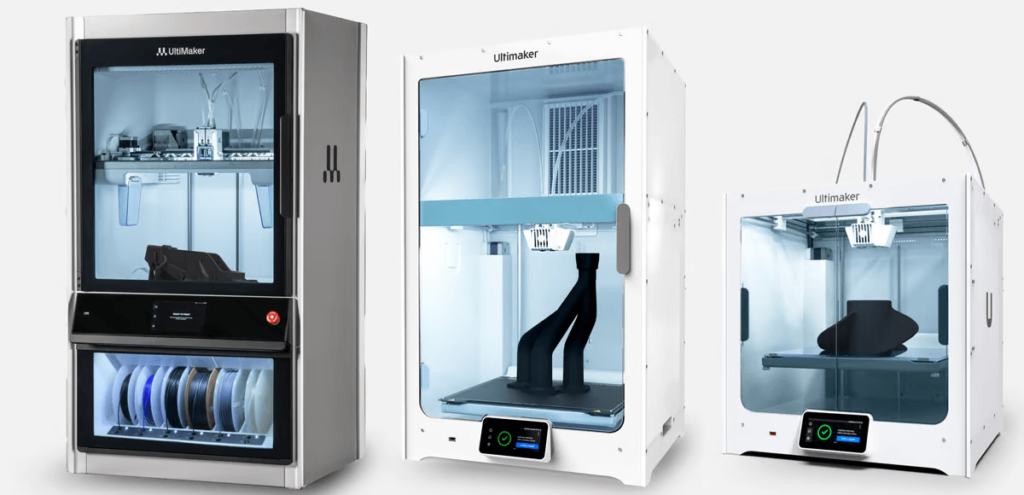
The new UltiMaker Factor 4 has the same build volume as the company's flagship S7 machine, but integrates the six-thread system. That's right, UltiMakers S5 (Source: UltiMaker)
Instead of improving his S7, who is only one year old, UltiMaker created something new that still looks a lot UltiMaker. Factor 4 there is sturdy steel and aluminum chassis, chamber with active heat control up to 70ºC, triple insulated building volume, a direct drive extruder with a larger motor and a nozzle temperature that can reach 340ºC, to allow materials such as metal filaments PPS-CF, PEKK and Ultrafuse.
These are not uncommon features in desktop FDM machines such as the Stratasys F190CR or Markforged FX10, but what UltiMaker distinguishes Factor 4, is consistency, repeatability and a fully integrated process from the software UltiMaker Cura and the materials of UltiMaker, by printing and validating the print. Furthermore Factor 4, starting at around $20,000, is less than half the price of the Stratasys and one-fifth the price of the Markforged.
"It's a clock," says Gasperini. “What is important in light industrial environments is … a predictable process. Our stress is really making sure that the dimensional accuracy and the amount of material we're extruding per second is always the same.”
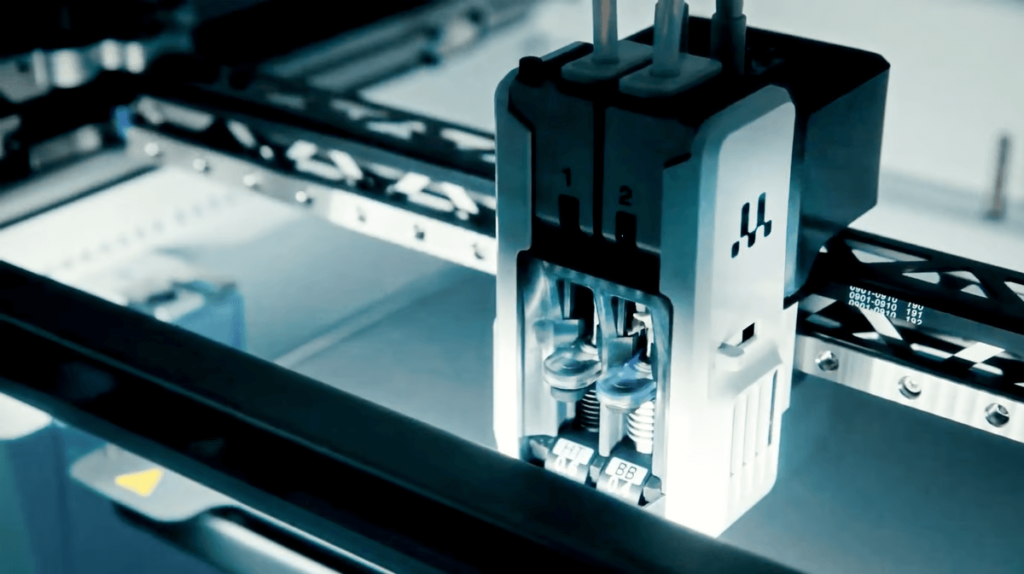
Factor 4 has a 50% performance increase over the series S, says Gasperini, without going into detail about print speed, other than to say, "We're faster than Bambu [Lab] and Raise3D when it comes to dual-material printing."
This is due to the twin extruder UltiMakers, which efficiently prints two materials simultaneously without retrieving the filament on the material changers found in Bambu Lab , and now also in Creality and Anycubic . Gasperini said a faster print speed is being developed for Factor 4.
On the predictability of Factor 4 new software designed to track the entire printing process also contributes. There is a new set of sensors that monitor real-time print data and material performance, providing reports after each print job to provide a level of part validation and quality control.
“Accounting for the printing process allows the customer to understand the process and make a decision to use the part or re-evaluate and re-evaluate, and have the confidence to implement,” says Gasperini.
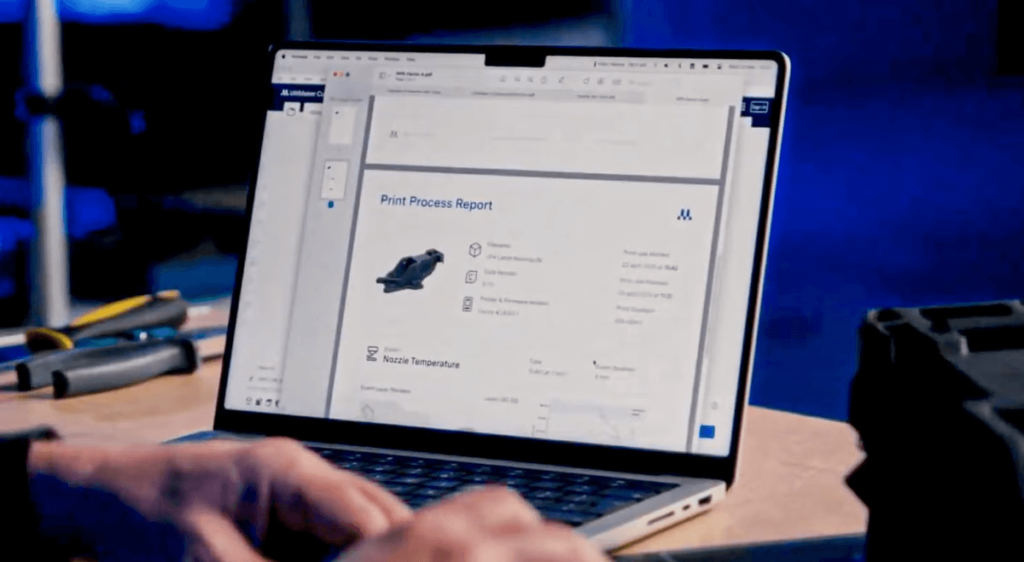
Confidence in results
Confidence that the part you just printed will perform under stress as intended is a barrier to 3D printing adoption, finds UltiMaker. There is still skepticism about whether FDM can deliver quality; in other words, reproducibility, accuracy and structural integrity of industrial components.
"We addressed this at the hardware level with significant advances in the direct drive printhead and a very different gantry from the S Series," says Gasperini. A notable change from the S Series is the fully integrated multi-material system of Factor 4, but the machine is multi-modular to allow easier service. Spare parts and consumables are replaceable, including the material station, printhead, gantry and ventilation system, and user interface panel. These features allow UltiMaker to guarantee higher uptime, says Gasperini. If you have spare parts, you can guarantee the level of performance that companies and manufacturers say they require.
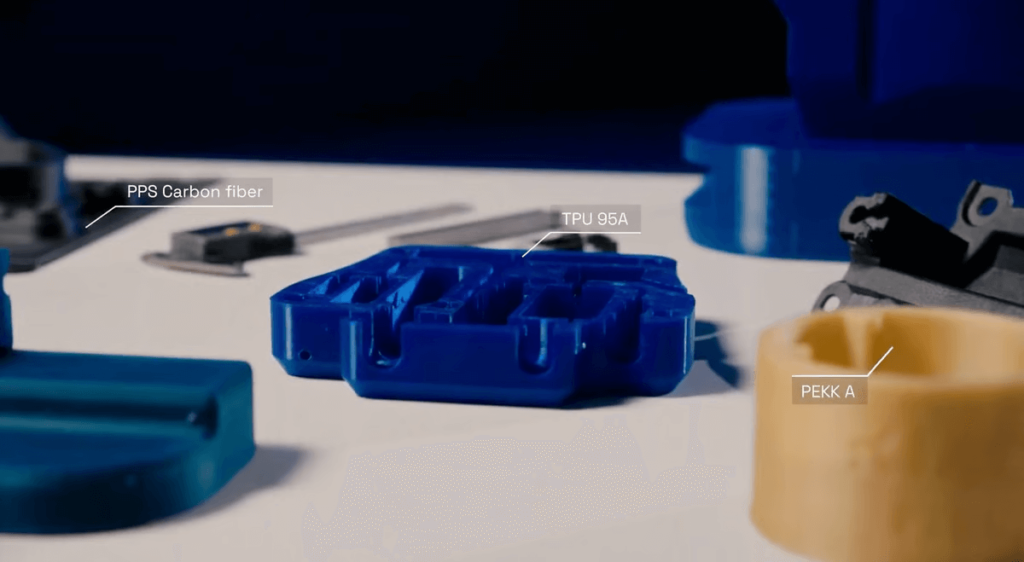
Factor 4's higher temperature nozzle enables printing with engineering grade materials including PEKK and PPS carbon fiber (Source: UltiMaker)
Engineering quality materials
From customers who have purchased UltiMaker S7, when it comes out in early 2023, there is a significant growth in the use of engineering-grade materials, says UltiMaker.
Customers who wanted tools, fixtures, welding fixtures and production aids didn't want to print them every day. They wanted parts from materials that could withstand higher wear and higher temperatures, up to 150 in continuous operation, Gasperini says. The latest materials of UltiMaker, PPS-CF (пpolyphenylene sulfide reinforced with carbon fibers) is designed for parts that must withstand high loads and stresses and show good resistance to wear and friction, plus it has flame retardancy and chemical resistance.
"That's why it's not just about having a carbon fiber composite," says Gasperini, "We also wanted to bring additional properties that are key and necessary for working in harsh environments."
Factor 4 can print with materials with a lower Shore value – softer and more flexible materials – up to 70 Shore A.
All these materials combined with reliability and ease of use are what UltiMaker believes that a new segment of customers wants. "We are also targeting the packaging industry, engineering, automotive, transportation and the military," says Gasperini.
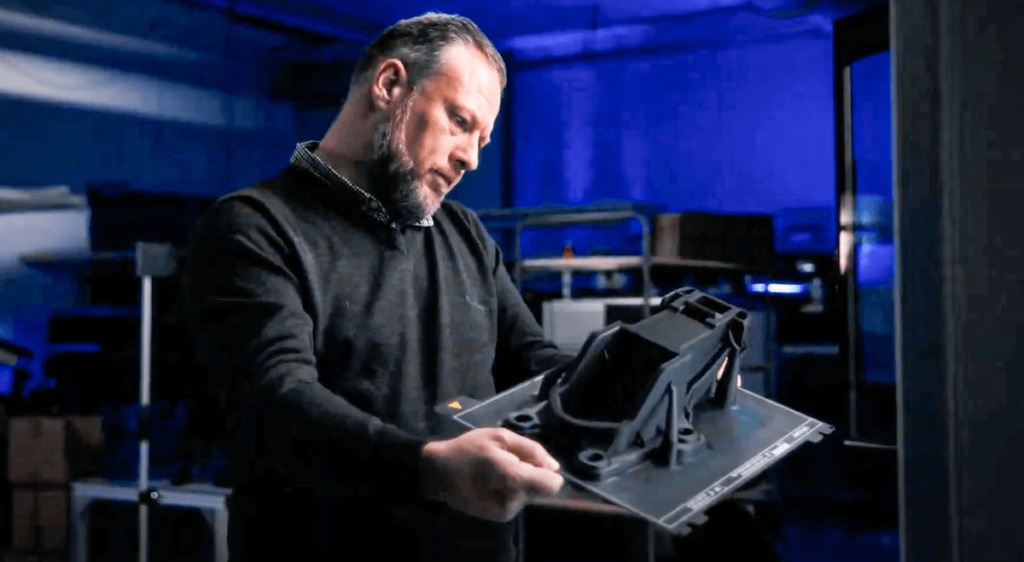
Although the Factor 4's build volume is the same as the S7, it can print larger parts with more confidence at the edges, says UltiMaker (Source: UltiMaker)
Yet, despite the machine's ease of operation, the end user likely won't be the machine operator on the line, but rather the person or engineer who directs the manufacturing process from part design to material selection to manufacturing.
UltiMaker expects that it will be a breakthrough with Factor 4, attractive to companies that are interested in additive manufacturing but do not know how to implement it in their facilities.
“I think some people just look at UltiMaker like hardware, but you get a lot more than just hardware," says Gasperini. “We offer end-to-end support … in helping our customers use additive manufacturing, and that's where we're seeing more requests; they want to know anywhere it can be used."
Michiel Alting von Geusau, CEO of UltiMaker, reiterates this point: “With our comprehensive support, we help customers navigate the complexities of 3D printing and identify opportunities with this technology. There is untapped potential in the light industry market and we believe that Factor 4 will enable customers to further explore application opportunities in this space.”
Technical specifications
- Technology: FDM
- Construction volume: 330 x 240 x 300 mm
- Dimensional Accuracy: within ± 0.2 mm or ± 0.2%
- Air filtration: HEPA filter
- Materials: Available at launch: UltiMaker PPS CF and other UltiMaker branded materials such as PLA, Tough PLA, Polyamide, PETG, PET CF and PVA, plus validated materials from BASF Forward AM, Kimya, Polymaker, LEHVOSS, Jabil and others. Factor 4 will be compatible with UltiMaker Marketplace materials, with 250 preset print profiles.
- Thread Size: 2.85 mm
- Price: about $20,000
We from 3MG Bonev Ltd. we are excited about the new Factor 4 on UltiMaker. We await your e-mail delivery inquiries:
3mgbonev@gmail.com
or use our site with the Contact Us form provided:
0 Comments