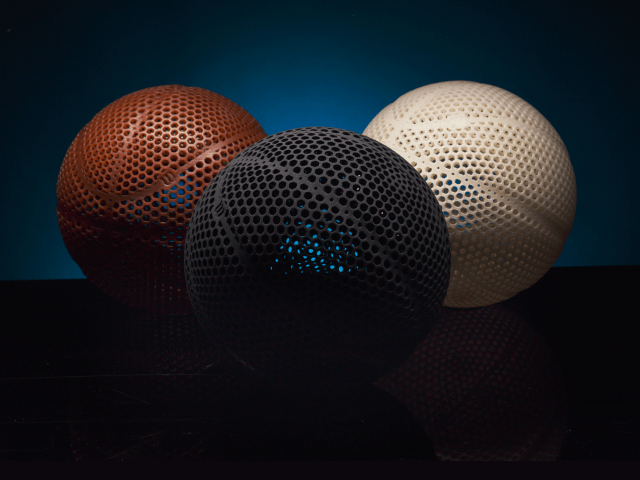
Wilson Airless Gen1 3D Printed Basketballs. (Image via Wilson.)
The American sports equipment manufacturer Wilson Sporting Goods Co. announced that it will be selling its 3D printed airless basketball.
Originally unveiled as a prototype last year, the Wilson Airless Gen1 3D printed basketball will be priced at $2500 in a limited edition starting on February 16, 2024.
As with the prototype, the basketball was developed in collaboration with 3D design specialists General Lattice, the manufacturer of 3D printers EOS and post-processing company DyeMansion. California-based SNL Creative has also joined the partnership as the primary production hub for the product.
According to Wilson, the basketball is fully functional and meets NBA ball performance requirements for weight, size and rebound.
The Airless Gen1's 3D-printed grid structure features eight panel "compartments," eliminating the need for inflation before use. The Airless Gen1 will be available in black, brown and off-white natural colors.
EOS, DyeMansion and General Lattice received an honorable mention in the 3D Designer of the Year category at the 2023 3D Printing Industry Awards for their work on the Wilson Airless Prototype basketball.
Wilson to sell Airless Gen1 3D printed basketball
The Wilson Airless Gen1 Basketball is a direct evolution of the 3D printed basketball prototype unveiled during the 2023 NBA Slam Dunk event.
Designed with GL Labs, General Lattice's enterprise solutions service, Wilson's basketball prototype was 3D printed using a 3D printer EOS P 396 SLS. Post-processing is completed by DyeMansion and its DeepDye Coloring and VaporFuse Surfacing technologies.
Set to debut during NBA All-Star weekend in Indianapolis, the new commercially available basketball features some new modifications. The 3D printed grid underwent digital and physical testing to create a more consistent presentation of the ball.
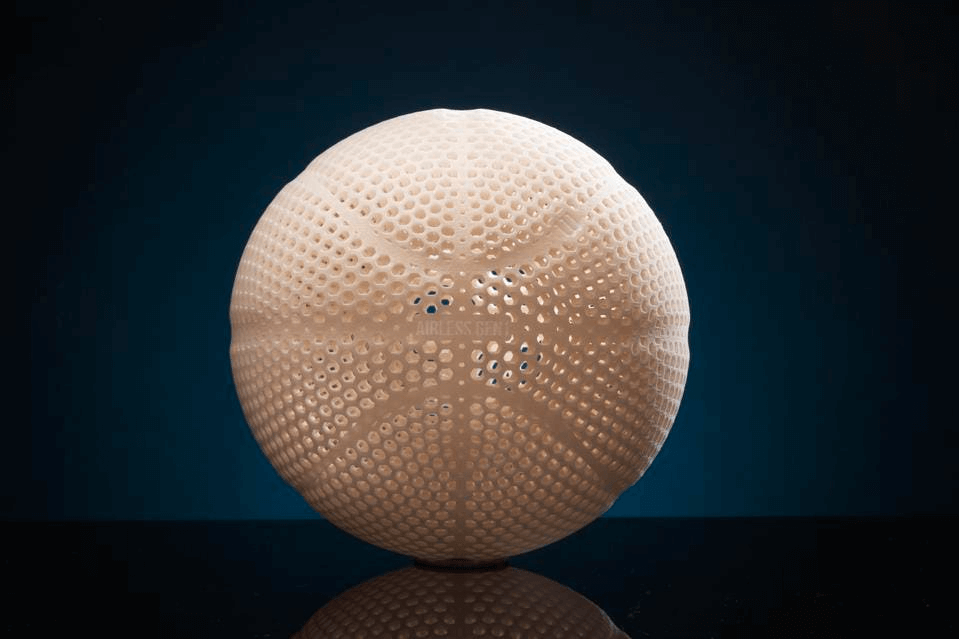
Wilson Airless Gen1 Basketball in off-white natural color. (Image via Wilson.)
Additive manufacturing and post-processing times are also reduced with the addition of holes in the grid channels, allowing for the rapid removal of loose dust after 3D printing. The complete manufacturing process includes 3D printing, smoothing, painting and sealing.
Wilson hopes that the commercialization of his airless basketball will spur industry interest in 3D printing, with greater adoption potentially eliminating air retention challenges in ball production. 3D printing is also said to offer sustainability benefits and allow products to be quickly adapted to customer needs.
The company will now look to further optimize its Gen1 design, with a view to releasing a Gen2 version in the future.
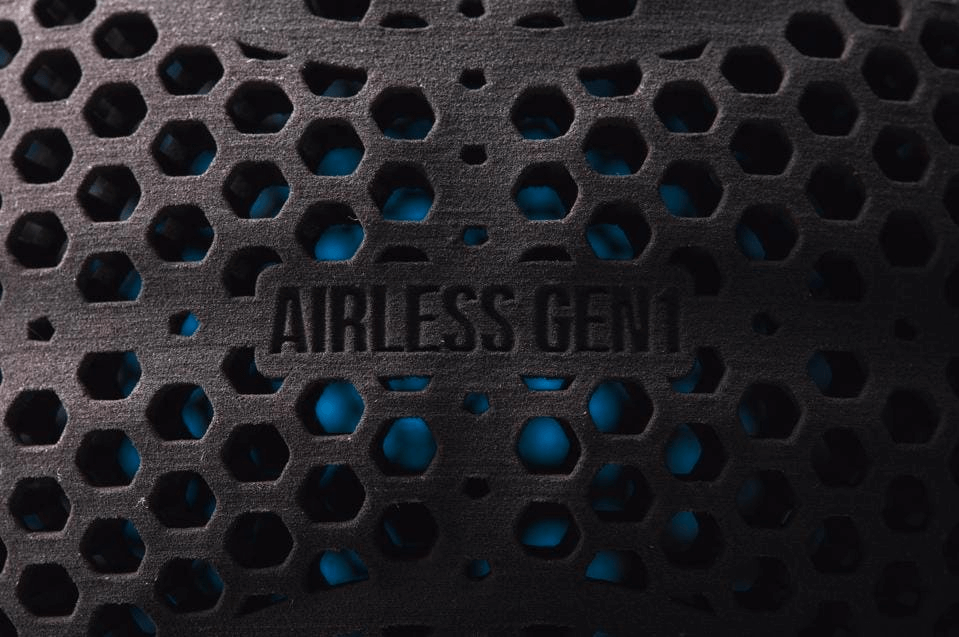
A close-up of the 3D printed grid of the Airless Gen1 basketball. (Photo via Wilson.)
0 Comments