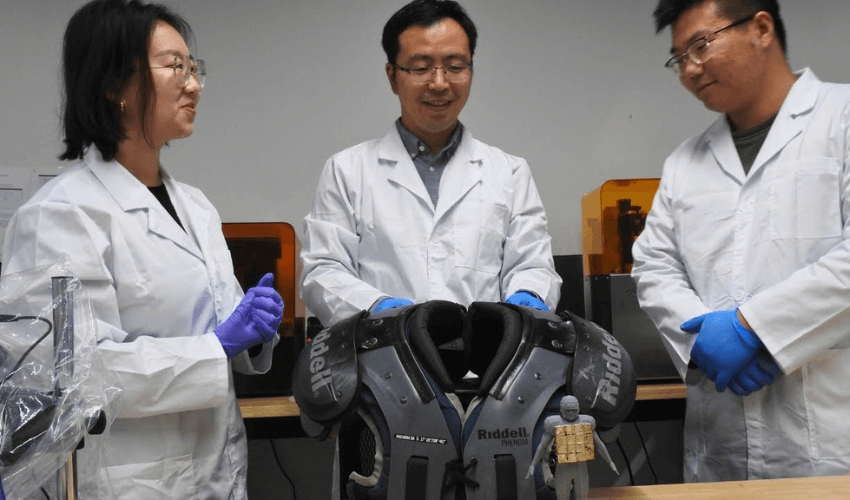
San Diego State University researchers are revolutionizing bulletproof vest design, drawing inspiration from the resilience and adaptability of marine life. Led by Professor Yang Yang and his research team, this transformative approach integrates cutting-edge sensing capabilities into protective equipment developed from a tough yet highly durable composite. And this was made possible through the use of 3D printing.
While marine life has already been studied for inspiration in the development of protective equipment, SDSU researchers have focused their attention specifically on the endurance of cuttlefish. Known for its lightweight yet incredibly elastic properties, Professor Yang and his colleagues sought to emulate its structural composition. Because some species of cuttlefish can thrive under the enormous pressures found 2,000 feet below the ocean's surface, they have developed a rigid yet lightweight microstructure in their shells to help them cope with these extreme conditions. This microstructure, known as "wall baffles", allows the cuttlefish to efficiently absorb and dissipate energy to easily cope with this intense physical pressure.
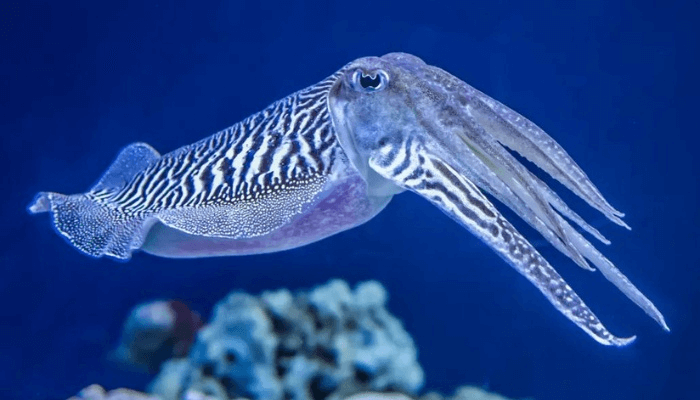
(Photo: BBC Wildlife)
Recognizing the potential of this capability, SDSU researchers have identified a significant impact reduction application. To mimic the structural efficiency of wall barriers, Yang and his team cultivated piezoelectric crystals from Rochelle salt, integrating them with cuttlefish bone. In doing so, they have developed a new composite material that dramatically absorbs impact force.
Practical applications of SDSU's 3D printed armor
The versatility of this advanced material extends across a wide range of industries, ranging from sports to defense, aerospace and healthcare. One major application of this composite is in helmets, which could revolutionize safety in sports and construction. These helmets not only offer superior impact protection, but also feature real-time monitoring capabilities to alert medical personnel to any signs of distress experienced by the wearer. Similarly, in healthcare, customized exoskeletons such as braces and knee braces can include sensors to detect falls and provide in-depth impact data, increasing safety for the elderly.
There are also significant advantages in terms of sustainability, as the nature of 3D printed components allows for easy and affordable maintenance and repair. Damaged parts of the 3D printed body armor can be quickly replaced or repaired by applying droplets of the composite to the broken areas, extending the life of the product and reducing waste – a stark contrast to conventional materials that often end up in landfills.
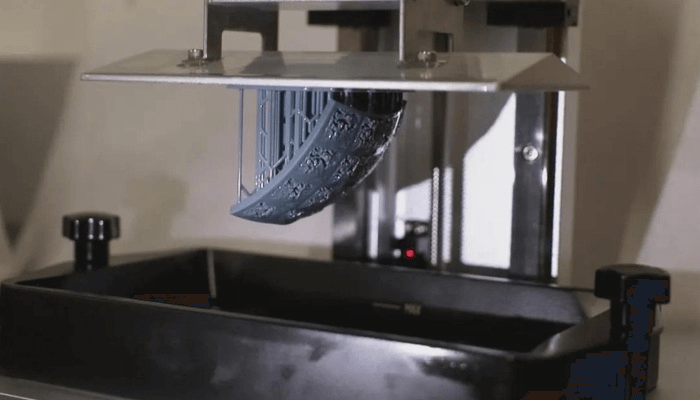
Sepia inspired composite. (Photos: San Diego State University)
Explaining this process, Yang added: “When traditional pottery breaks, it's impossible to heal it this way, creating a lot of waste. Our method, on the other hand, is reusable. The manufacturing process uses much less energy and the total cost of the product is lower.”
As Professor Yang's team continues to refine their body armor, collaborations with industry partners are underway. Since developing their body armor, they have partnered with NFL affiliate 3D Systems to advance research on how this composite and armor can be improved and implemented in the league.
What do you think of this sepia inspired 3D printed armor? Tell us in the comments here:
0 Comments