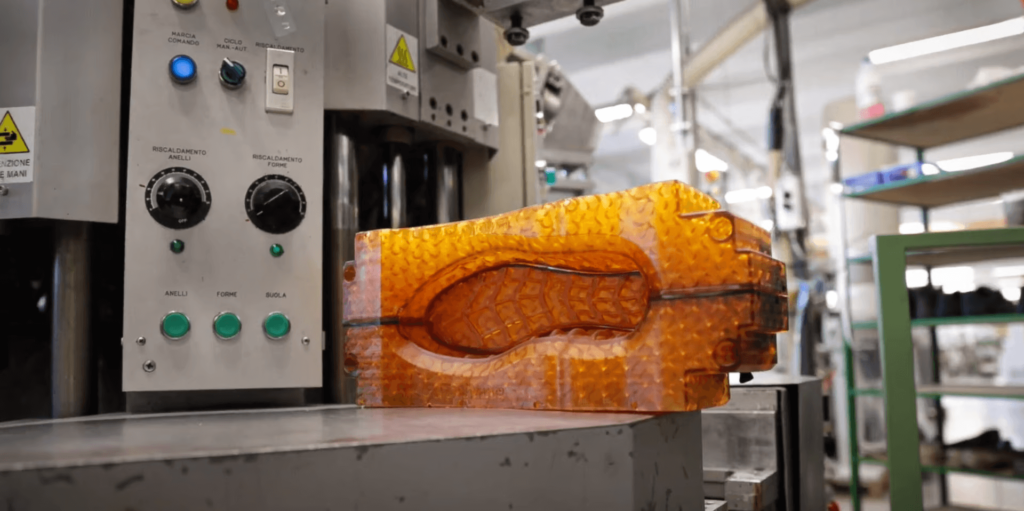
The high performance, high temperature resistant plastic allows a 3D printed injection mold to match the performance of an aluminum mold with the advantage of lower cost and faster production.
After more than four decades of manufacturing high-quality walking and safety shoes, Grisport has made a big leap. The Italian manufacturer has turned its processes around and is replacing its expensive aluminum injection molds with its own 3D printed ones that produce the same result at a tenth of the cost and 50 times faster.
"3D printing will fundamentally change the way we bring models and products to market," says Giovanni Grigolato, the company's head of R&D.
Grisport no longer has to worry about producing a shoe design that will generate the minimum amount of sales to justify the €5,000 ($5,500) cost of producing an aluminum mold. At around €500 per 3D printed mold, the company can bring more designs to market. It also opens up the possibility of producing limited edition and custom products.
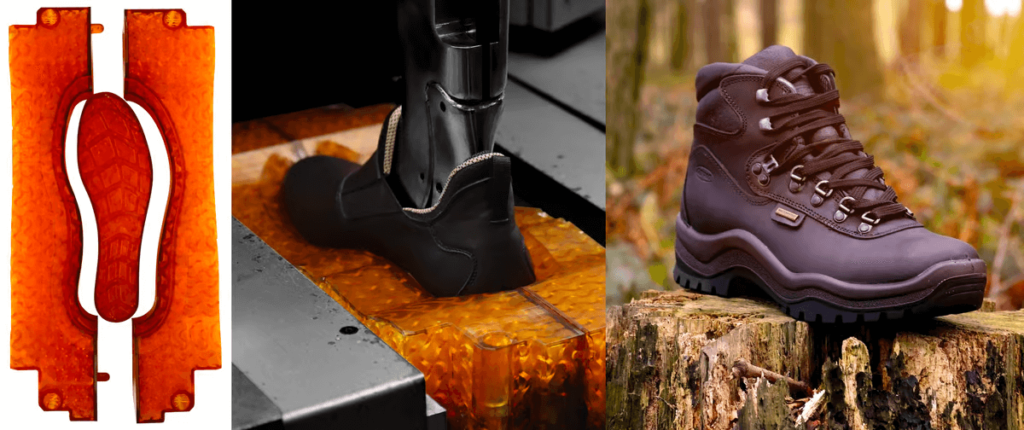
Grisport is one of the leading manufacturers of direct injection shoes worldwide, so they know the shapes. The company researched durable, heat-resistant 3D printing materials and technologies for months before choosing Photocentric Liquid Crystal (LC) Magna, a large-format resin 3D printer, and its HighTemp DL401 material.
"Magna and HighTemp DL401 are transforming the way shoe molds are made," said Hanifeh Zarezadeh, Product Manager at Photocenric. "You can now use the same plastic and the same process as the aluminum mold, but with all the benefits at a lower cost and faster time to market."
The material and printer work together to produce a final shape that has very high strength, stiffness and impact resistance while matching the precision and dimensional accuracy of traditional aluminum forming and machining, Zarezadeh adds.
“The HighTemp DL401 is very good for us because it reaches the higher temperatures needed to inject PU (polyurethane) and keeps them stable,” says Grigolato.
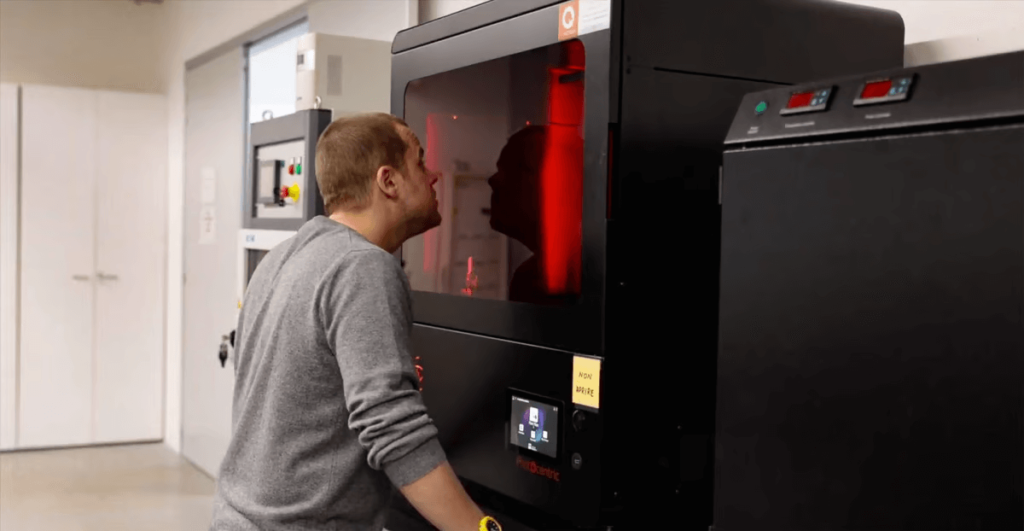
Strength isn't the only reason Grisport endorsed the move to 3D printing. The speed of their production is also an important factor, the company says.
Grisport can produce an entire shoe mold, which consists of three parts, on its LC Magna in 14 hours. Waiting for an aluminum mold from a third party supplier took weeks or more.
A faster, cheaper form means faster prototyping and iteration, and ultimately faster delivery of a product from idea to store shelves.
Grigolato says that before 3D printing, the initial design of the finished product took about four months using a traditional aluminum mold. “But with this new technology, we can do it within a month and a half. In-house 3D printer mold production is revolutionary for us.”
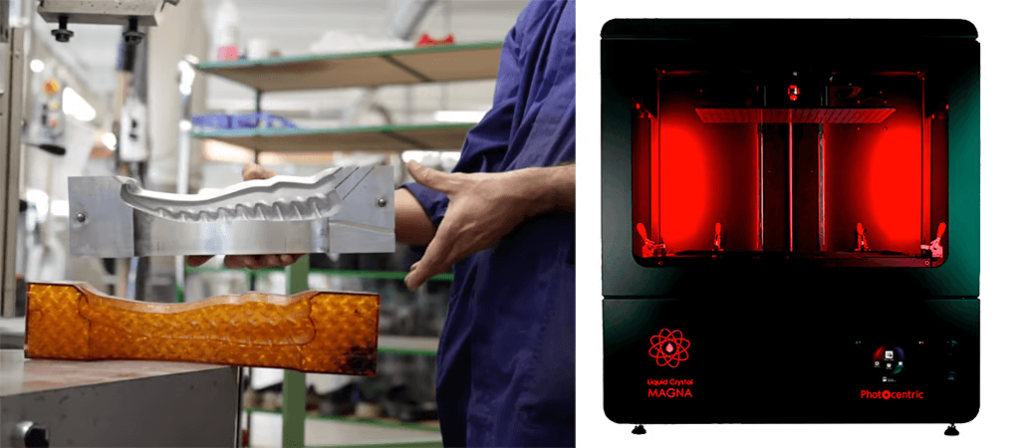
Grisport found that designing the mold for 3D printing is essentially the same process as designing a mold for aluminum production. The company is optimistic about its ability to put these 3D printed molds into mass production at the end of its ongoing feasibility study.
0 Comments