Additive manufacturing is constantly evolving in all areas. Indeed, this year alone saw exciting developments in metal 3D printing, bioprinting and multi-material printing, as well as interesting concepts for greater sustainability. Here is one of them.
POOLP
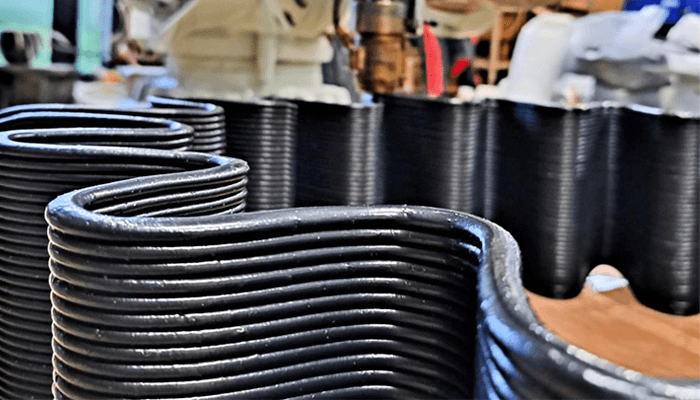
The first 3D startup, the French company POOLP, which was created by two students from ENPC (École Nationale de Ponts et Chaussées) who wanted to expand the potential of additive manufacturing in art and architecture. After experimenting with a variety of recycled and bio-based materials, they developed their own solution to make them compatible with 3D printing. Thus arises the so-called "urban microfactory", a production tool capable of valorizing local plastic waste and transforming it into material for additive manufacturing. The 3D printing system uses large-format FGM (Fused Granulate Modeling) technology, which uses plastic pellets instead of filaments to create all kinds of three-dimensional parts. With this production system, the POOLP team aims to promote the circular economy, an alternative philosophy of production and consumption.
Spherecube
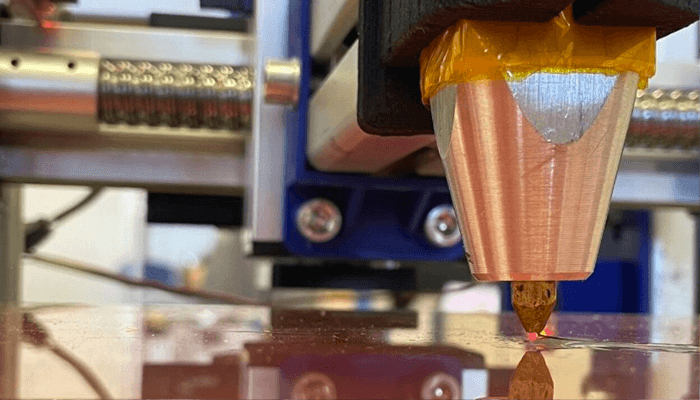
Born from a project of the Università Politecnica delle Marche, Spherecube is an innovative startup working to make 3D printing of composites more sustainable. The laser thermal curing system, developed by his team, is able to automatically create composite products with high performance and without geometric restrictions. More specifically, the Spherecube technology is based on the extrusion of two raw materials in different aggregate states. On one side is the thermosetting polymer matrix (in a viscous liquid state) and on the other – the reinforcing material (in the form of fibers). Thus, the print head is designed to effectively mix the matrix and the reinforcement so that there is perfect adhesion of both during the production process. With this technology, the startup is targeting industries such as aerospace, biomedical, sports and marine.
Axtra3D
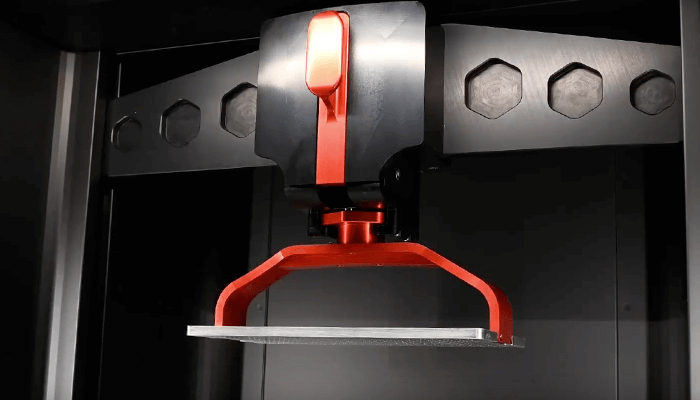
In the field of 3D resin printing, two technologies stand out: SLA and DLP. The former is precise but slow, while the latter is much faster but with major limitations in surface quality. American startup Axtra3D has come up with a solution to this problem. The HPS (Hybrid PhotoSynthesis) technology developed by the company combines both methods to ensure high resolution parts in a much faster process than stereolithography. Specifically, its machines integrate a projector (DLP) and a laser (SLA) simultaneously in a true coaxial system. This additive manufacturing method is thus ideal for applications in a wide variety of industries, including automotive, aerospace, prototyping, healthcare and dentistry, and more.
Diabatix
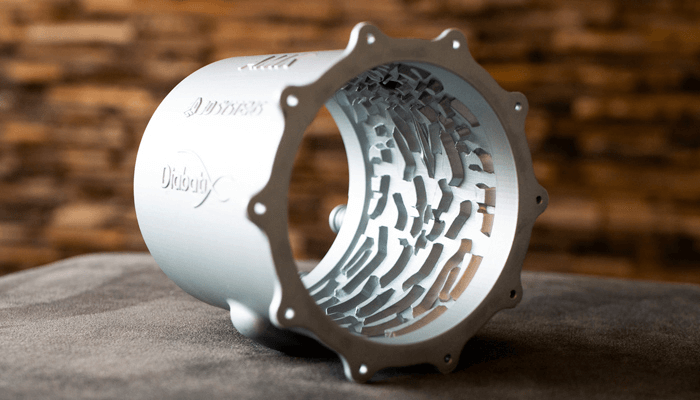
Belgian startup Diabatix was created with the goal of helping companies with the design of their products to get proper cooling. To this end, it has developed ColdStream, a cloud-based platform that enables the use of generative design tools to provide better cooling for 3D printed parts. From thermal analysis to thermal design, the platform is based on state-of-the-art simulation methods without the need for additional software or hardware. In addition, something very interesting about the solution developed by Diabatix is that it adapts to the production method that will be used later. That is, before starting the design process, the user will select the manufacturing technique of his preference and the software will automatically optimize the design within the limits of the selected technique.
Gastronology
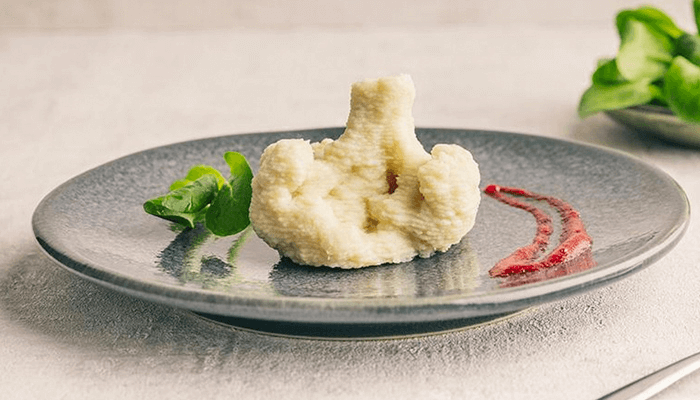
Dysphagia is a medical condition that causes difficulty in swallowing in many patients. This causes the body to need more time and effort to move food or liquids from the mouth to the stomach. To make swallowing easier for those with the condition, Dutch company Gastronology turned to 3D food printing. Specifically, he has developed an additive manufacturing solution that allows food to be presented in its original form, made from fresh puree, with a natural smell and designed in its original form. Gastronology products can also be found frozen and packaged. This requires a five-step process: pureeing, food 3D printing, shock freezing, packaging and frozen storage. Thanks to this technology, the company manages to turn eating into a moment of pleasure, replacing the tasteless and mixed options that currently exist for patients with this condition.
3D Spark
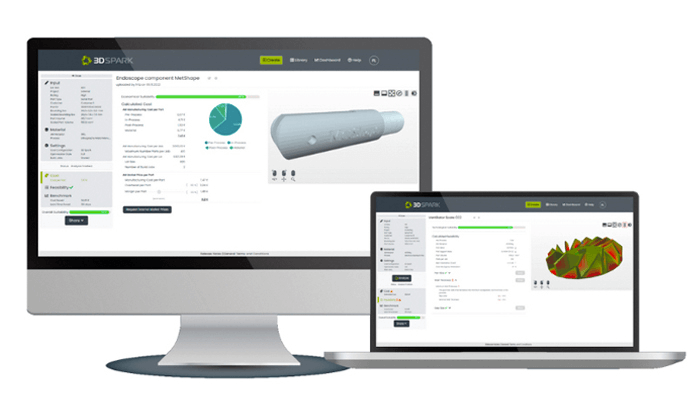
The adoption of workflow management software in additive manufacturing is a growing trend in the industry. One of the companies developing such solutions is another 2023 3D startup, 3D Spark. Based in Hamburg, the startup emerged with the goal of helping companies find ways to reduce costs and lead times while reducing CO2 emissions in production. In turn, Spark 3D's platform ensures that they can benefit from automated evaluation of 3D printed parts and identify the optimal development process for their products. The latter is done by comparing 3D printing with a wide variety of manufacturing processes, providing a transparent and independent basis for manufacturing decisions. As a result, industrial companies will be able to choose more efficient, sustainable and crisis-resistant production.
ONEBra
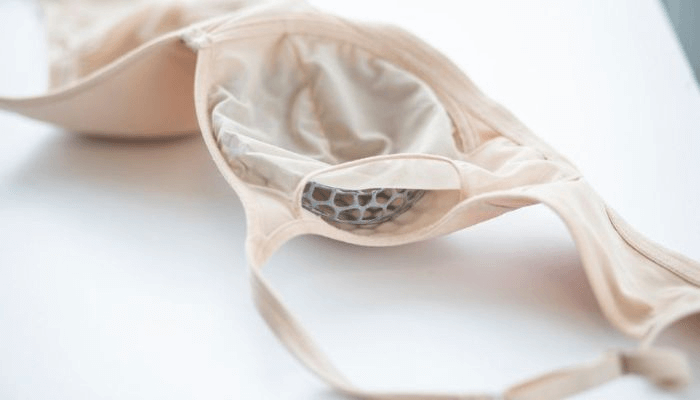
The Italian startup ONEBra highlights a problem that affects many women: those who have undergone a mastectomy often suffer from asymmetry of their breasts. ONEBra counters this with custom 3D printed cups. Through this, the 3D startup aims to help women improve their self-image and quality of life. The process is also simple. On the website, you can create a 3D breast scan by following simple video instructions. The ONEBra team then uses this scan to create a custom bra cup. The team used a combination of MJF and FDM technology. The TPU/TPE cup is coated with a skin-friendly material and shipped directly to the customer. 3D printing allows ONEBra to produce customized cups with as little waste as possible and with high precision. ONEBra also wants to offer cups for sports bras and swimwear.
HETEROMERGE
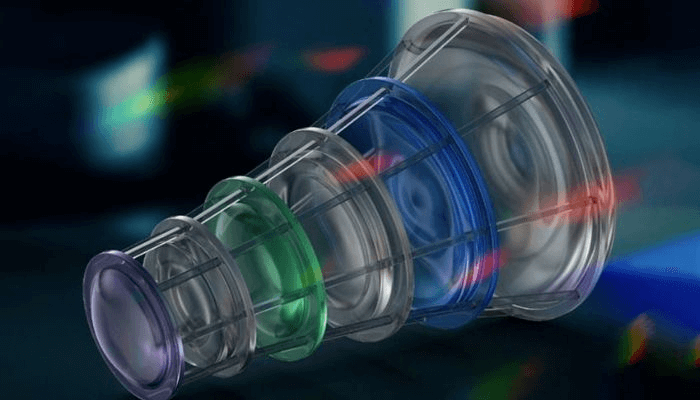
The next 3D startup, HETEROMERGE, emerged from the University of Dresden with the goal of creating a multi-material production head for more efficient micro 3D printing. During their research work, the HETEROMERGE team encountered several challenges in micro- and nanoscale 3D printing. First, there are more limitations in this submillimeter range and, more importantly, it was difficult to process multiple materials using 2PP technology. The patented multi-material head is designed to counteract this problem by allowing perfect readjustment after automated material changes. This technology opens interesting areas of application in micro-optics, photonics, in the development of medical devices, as well as in tissue engineering and bioprinting.
Carcinotech
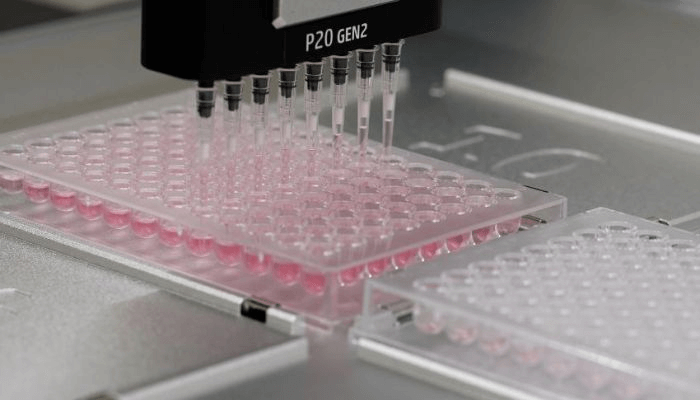
Founded in 2018, Carcinotech was one of the most prominent 3D startups in 2023. It specializes in creating tumors using 3D printing for cancer research. The team used 3D bioprinting to create living tumors from biopsies, primary cells, immune cells and cancer stem cells from patients. After fabrication, the tumors grow and are ready for drug testing within a week. This enables fast, accurate and ethical drug screening as results are available 14 days after the test. With its approach, Carcinotech aims to give millions of cancer patients access to innovative therapies. It is the only company using 3D printing to produce live tumors to obtain representative and meaningful data.
Balena
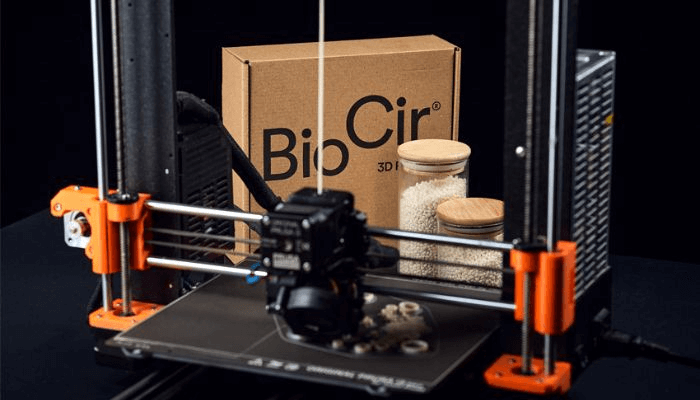
Balena tackles one of the fashion industry's biggest problems: extending the useful life of products. About 60% of today's clothes are made of plastic that is rarely recycled and ends up in the trash. To create sustainable fashion for the future, the Israeli company is developing compostable and biodegradable thermoplastic materials for this industry. The BioCir material can be used for injection molding or 3D printing and recycled at the end of its useful life. In this way, Balena aims to create a circular model for consumer goods.
BIO INX
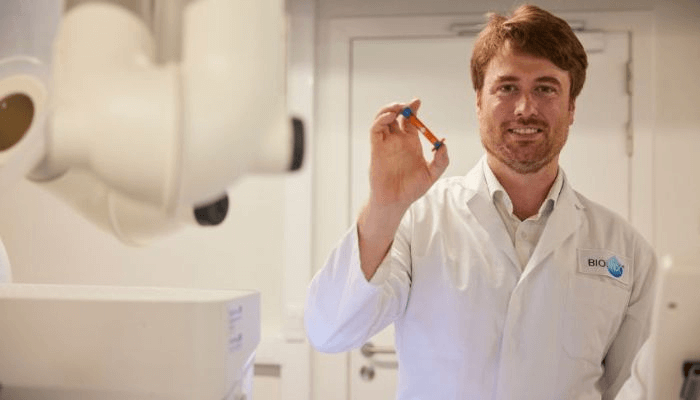
3D printing of organs, muscles and tissues are the main goals of the medicine of the future. Bioprinting involves not only science but also industry. Currently, the main challenges lie in standardization, regulations and different requirements for materials. Each printing technology requires a different material to process effectively. Belgian startup BIO INX has specialized in the development of bio-inks for various 3D bioprinting technologies. These inks are designed to mimic natural tissue as closely as possible without having to resort to animal testing. BIO INX wants to actively shape the field of biomanufacturing and contribute to the research of 3D printed tissues and organs.
Craft Health
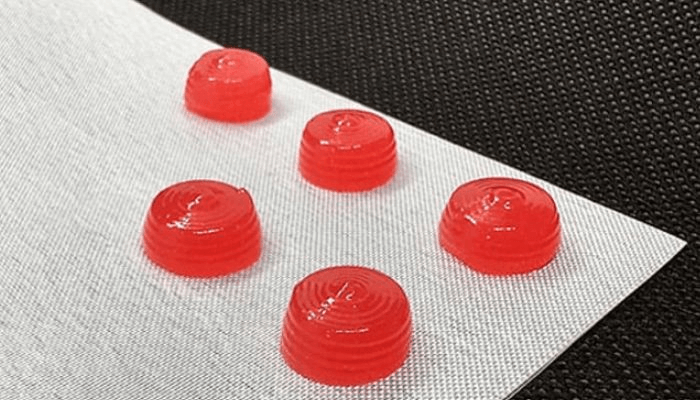
Craft Health, a Singapore-based pharmaceutical startup, wants to tackle the problem of polypharmacy and is counting on 3D printing as an ally. Polypharmacy, i.e. taking too many drugs often leads to interactions and therefore discomfort for patients. Thanks to 3D printing, Craft Health can combine several active ingredients in one tablet and thus create a personalized medicine. It is also possible to influence the dosage, shape, color and taste. Drug release can be immediate, sustained or delayed. Craft Health hopes its approach will help people take their medications and open up new treatment options.
0 Comments