Meet Pat, a visionary entrepreneur who revolutionized the automotive aftermarket industry with his innovative creation, the 'Cup Keeper Plus'. This ingenious product adapts to hold a variety of beverage containers, including flasks and water bottles, making it a must-have accessory for any car owner. Pat's success story took an exciting turn when a major US retailer placed a massive order for Cup Keeper Plus.
However, with great opportunities come great challenges. The retailer had specific labeling and packaging requirements. They requested labels with the exact size and orientation of each Cup Keeper Plus.
Pat's distinctive design, marked by its curved and pointed structure, presented a significant challenge in the manufacturing process. Additionally, the task of consistently labeling thousands of Cup Keepers proved to be an additional obstacle, compounded by the varying sizes that required the use of special devices. Meeting these requirements necessitated the use of high-strength and wear-resistant engineering materials.

Pat was not one to back down from a challenge. He enlists the help of his talented designer, who sets out on the path of innovation. Using the power of 3D printing technology from INTAMSYS, the designer created custom tools and fixtures to meet these demanding requirements.
Their joint idea culminated in the creation of the "label peeler," an innovative device that automates label placement by expertly peeling labels from a reel. Consisting of a 3D printed label peeler and label winding hub, this kit integrates seamlessly into a wooden fixture as shown below, forming a complete and functional unit. In addition, they developed a "Cup Fixture Assembly" precisely engineered to align with the internal geometry of the Cup Keeper Plus, providing stability and proper orientation for precise worker label placement.
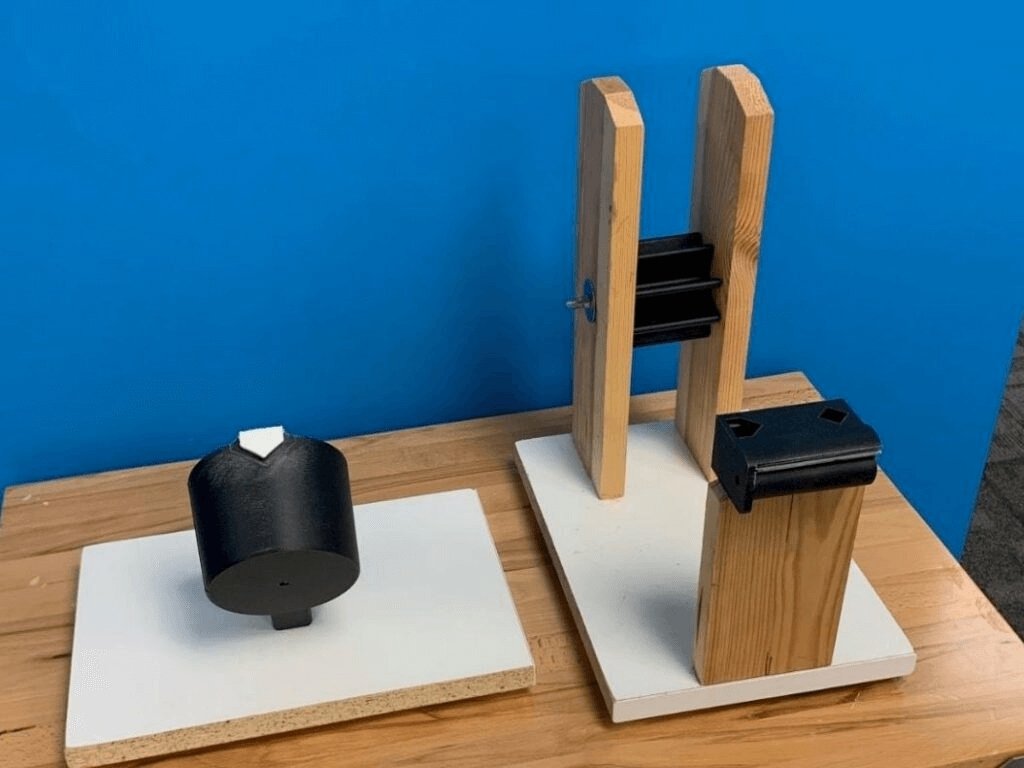
INTAMSYS became the chosen technology partner for this project, using the advanced FUNMAT PRO 310 3D printer to transform ingenious ideas into practical tools. Pat strategically chose INTAMSYS Nylon 12-CF, a material expertly reinforced with carbon fiber. This advanced nylon variant significantly improves mechanical stiffness, strength and thermal properties. Moreover, its exceptional wear resistance becomes a major consideration, especially when specifying materials for precision assembly tools of this nature.
The printer – the capacity of the FUNMAT PRO 310 with PA12-CF and its integrated drying chamber ensure optimal material performance. Its specialized support materials facilitate easy removal, ensuring a high-quality surface finish. With exceptional dimensional accuracy, the printer meets the precise requirements of tool and fixture manufacturing, setting a new standard for advanced 3D printing in precision applications.
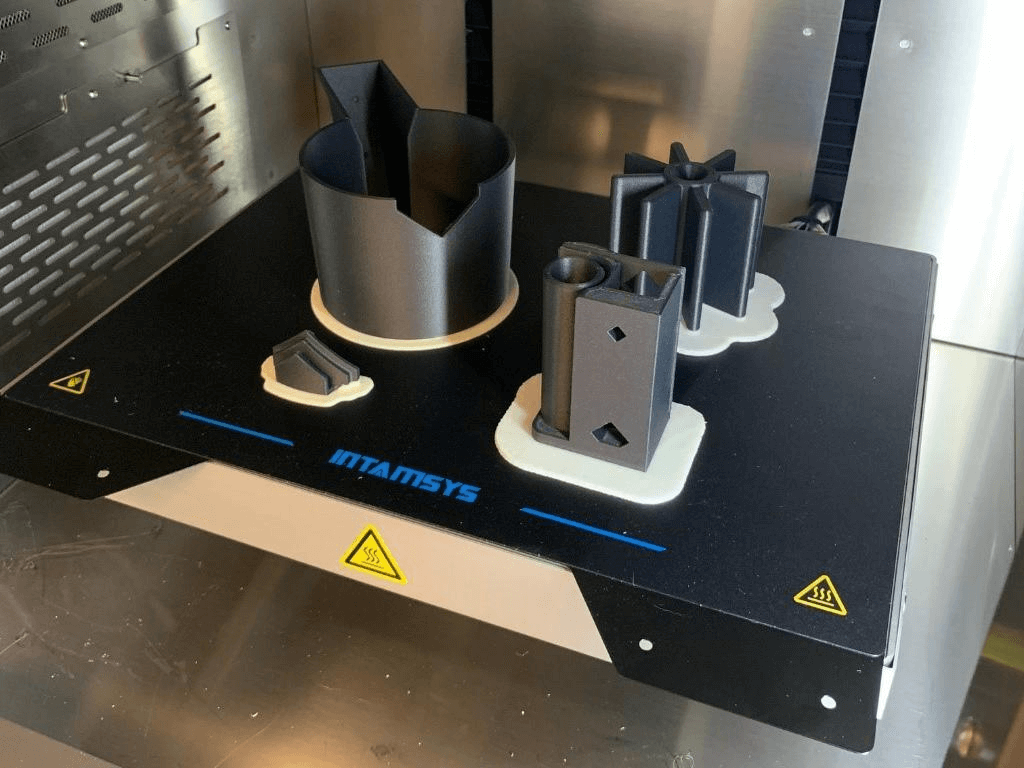
With the 3D CAD files expertly converted to STL files, Pat was ready to embark on the printing journey. INTAMSUITE software turned digital dreams into tangible realities. The FUNMAT PRO 310 swung into action by 3D printing every tool and fixture with precision and speed.
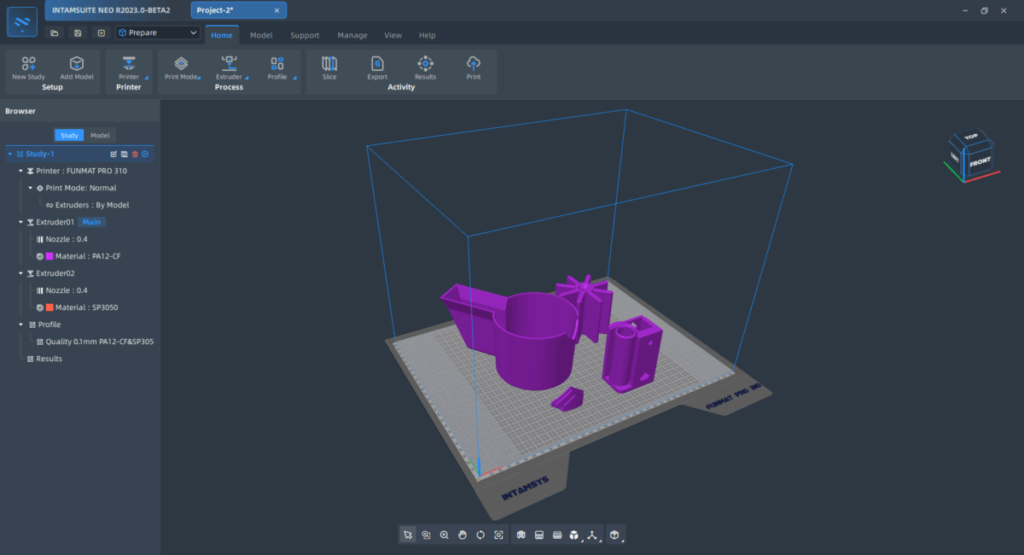
The results exceeded expectations, demonstrating phenomenal results. The Label Peeler and Cup Attachment assemblies have emerged as indispensable tools. Beyond simply printing a set of fixtures, the team faced the challenge of customizing multiple sets of fixtures to accommodate the various sizes of Cup Keepers. In addition, the bodies were tailored to different states, optimizing local use and streamlining efficiency. With this comprehensive approach, Pat's team established a highly efficient and reliable labeling process, seamlessly transitioning from loading the Cup Keeper Plus onto the alignment fixture to placing labels with remarkable precision.

This success story eloquently demonstrates the harmonious combination of innovation and technology. INTAMSYS, a pioneer in the 3D printing industry, not only enabled Pat to meet the retailer's packaging requirements, but also facilitated significant benefits in terms of design flexibility, cost efficiency and time savings. The ability to improve design freedom, combined with the advantages of prototype validation, tooling fixtures and small batch production, played a key role in securing further orders for the Cup Keeper Plus.
0 Comments