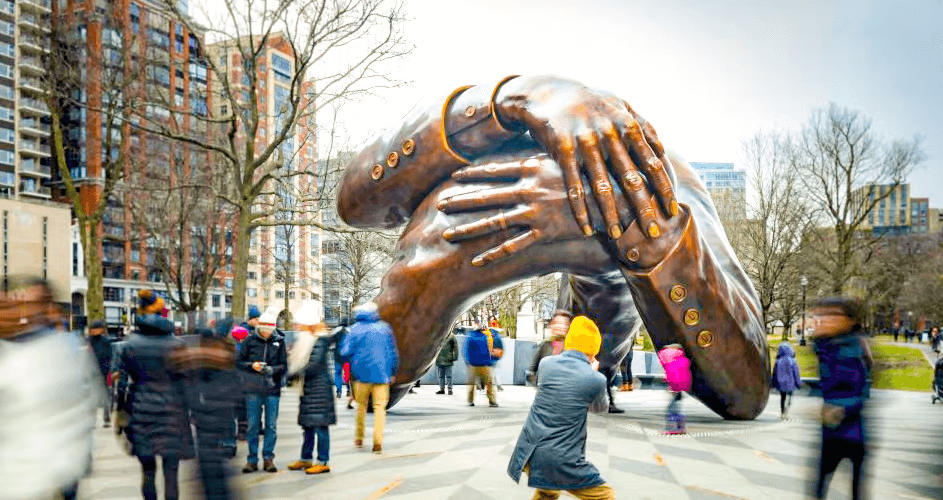
Love it or hate it, Boston Commons' 2023 statue "The Hug" is a triumph of 3D printing.
After the design of The Embrace – Willis Thomas, created a public artwork honoring Martin Luther King Jr. and his wife Coretta Scott King, was selected from among 126 submissions by artists and architects, work began on the actual construction of the statue.
Unlike conventional bronze sculptures, The hug it is not sculpted from clay or stone from which a mold is made and the bronze is cast. Instead The Embrace was a digital design inspired by a photograph depicting the Kings hugging in 1964 after learning that Dr. King had won the Nobel Peace Prize.
Although Thomas, a renowned conceptual artist, envisioned the monument's design, a team of architects, engineers and craftsmen had to transform his computer model into the 20-foot by nearly 20-foot-wide bronze landmark that now stands in Boston Commons, the oldest public park in the USA.

"The only way to construct a statue of this size without having a full-size model is with 3D printing," said Jonathan Follett, president of Walla Walla Foundry, the fine arts company responsible for the statue's construction. Walla Walla was established in 1980 with the sole purpose of facilitating the creation of contemporary art through bronze casting and fabrication.
Follett and his team began construction on The Embrace , by scaling Thomas's digital file to the desired size using Rhino software and splitting it into pieces. Each of the 608 pieces was about the maximum size of the company's Voxeljet VX1000 connector 3D printer. The VX1000's print volume (1000 x 600 x 500mm) can print five or six patterns at a time, or 15 to 20 flatter patterns.
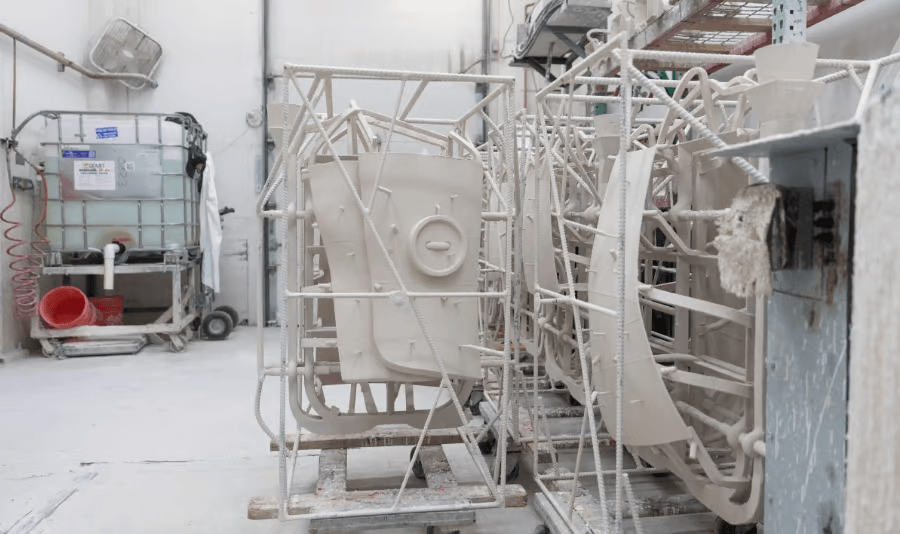
“We 3D printed every single part, the entire sculpture,” says Follett. Each piece is printed in a material called PMMA (polymethyl methacrylate), which is commonly used to print industrial models for investment casting. The pieces were then dipped repeatedly in ceramic material. Once the ceramic shell is built and cured, it is heated to melt the PMMA cleanly, leaving a cavity with the exact shape and texture of the part into which molten bronze is poured.
A key advantage of 3D-printed templates is that "you can have incredibly precise, uniform thickness in different geometries, and that means higher quality castings because your metals are cooling at the same rate," says Follett.
Walla Walla Foundry has two VX1000 3D printers running nonstop to print the parts, but they contacted Voxeljet, which printed many of the parts at its facility outside of Detroit. The statue parts or patterns required nothing more than the removal of the backing and a light sanding before the pottery was dipped.
Although the Walla Walla Foundry has been printing 3D templates for about five years, they are on the cutting edge of bronze sculpture work. Voxeljet 3D printers are used in industrial foundries, but are not common in artistic environments.
"I think the industry took Voxeljet a little by surprise," says Follett, "I don't think they made these printers thinking the art world would use them."
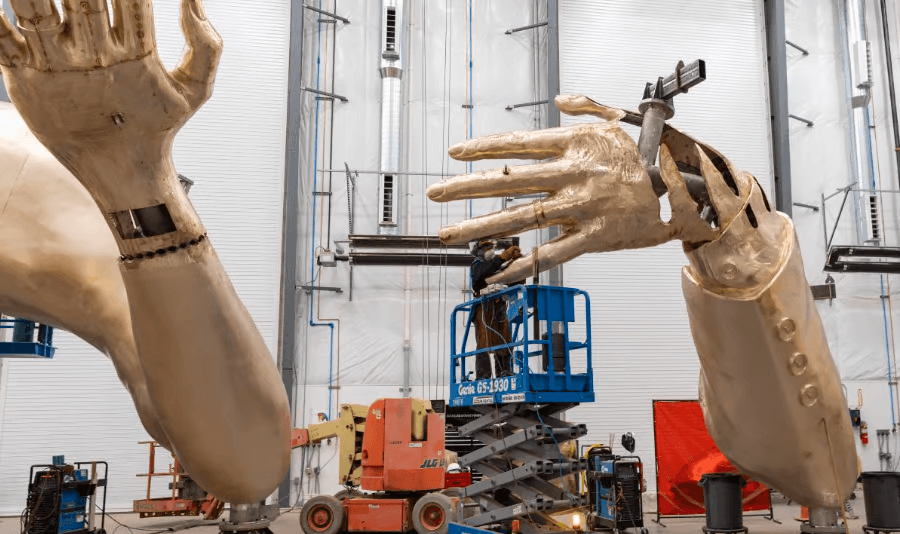
Walla Walla also used its Voxeljet to print a model of the entire statue for reference.
“(The statue) had to be manufactured here, fully assembled, and then had to be disassembled again to be shipped from our foundry in Washington state across the country to Boston,” Follett says. "So having that smaller 3D model was really helpful because the whole team understood the different parts, where the seam lines were, how it came apart and the intricacies of machining each part."
In total, construction, including the circular plaza designed and built by Mass Design Group, took two years. The $10 million statue was paid for entirely by private donations.
Without 3D printing, the only way to produce the statue would be to sculpt a full-scale model. For example, the Statue of Liberty was sculpted in full-size plaster casts as a model for wooden pieces on which copper sheets were hammered and tooled to create the statues' "skin". "Rodin's The Thinker" is sculpted full-size in clay before a plaster mold is made over the clay in which the bronze is cast.
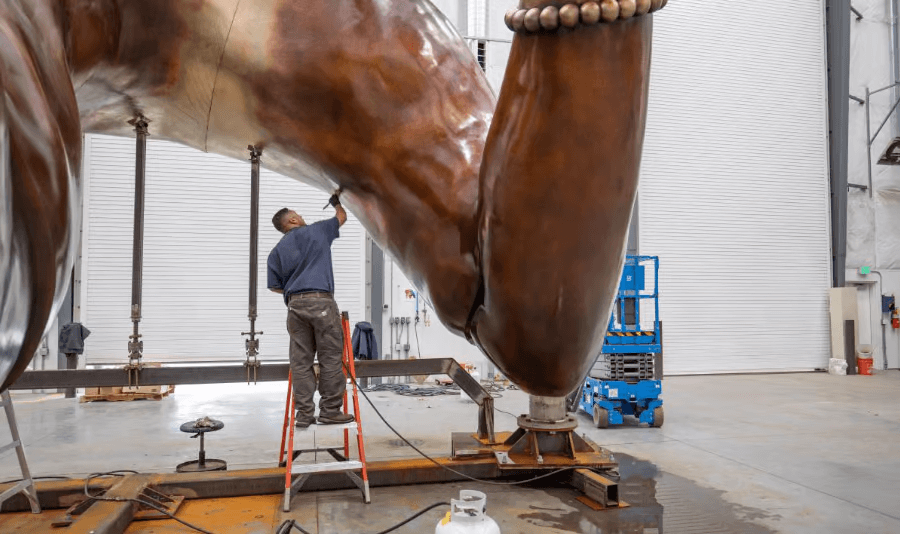
"I think artists will always sculpt originals, but there's definitely a large group of them who work digitally," says Follett. The only downside to this method is that the first time the artist sees the piece, it is already fully cast and assembled. "So it's really important that artists feel comfortable working in a 3D modeling space."
Overall, this method of scaling digital files for 3D printing and casting greatly expands artists' access to sculpture as a medium. With no more need for physical sculpting, there is virtually no limit to creative expression in large-scale bronze art.
0 Comments