How does SEAT use 3D printing in production?
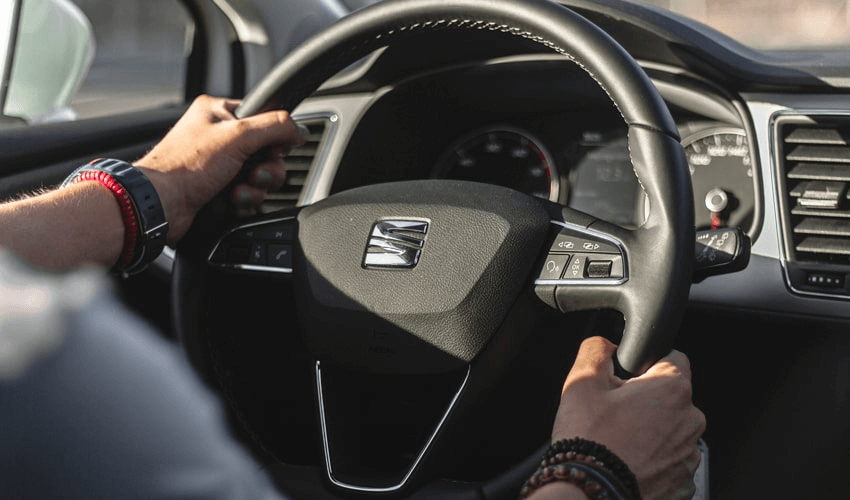
Photos: SEAT
The combination of 3D printing and car manufacturing has proven to be extremely successful. Many automotive companies have already adopted additive manufacturing as an integral part of their manufacturing processes. Notably, we can point to industry leaders such as BMW and General Motors who have established centers dedicated to 3D printing components for their vehicles. And while of course this is a huge trend in the US, it's increasingly evident in Europe as well. SEAT, a well-known car manufacturer, recently opened a 3D printing center to improve its production capabilities with state-of-the-art technology. To gain further insight into how the Spanish automaker uses this method, we're sharing an interview with their team.
Can you introduce yourself briefly and tell us more about how you got into 3D printing?
My name is Marc Travesset and I am a chemical engineer based in Barcelona. During my studies in 2007, I had an enlightening experience during a visit to Ascamm, now Eurecat, where I came across a fascinating machine that uses lasers to apply plastic powder. Although I initially pursued other interests in membrane technology and epoxy manufacturing, the memory of this "magical machine" stayed with me. It wasn't until years later, when I encountered the same technology at SEAT, where I worked as the person responsible for prototype parts, that my passion for 3D printing really ignited. Since 2018, I have been fortunate enough to actively engage with these technologies and deepen my understanding of the subject. I may not fit the typical Creator profile.
When did SEAT decide to integrate 3D printing into its processes?
For more than 20 years, we have harnessed the power of 3D printing in our operations. In the field of product development, flexibility is critical because of the inherent complexity of the work performed. Fortunately, we at SEAT have the ability to quickly and confidently validate concepts and achieve milestones in our development journey.
What 3D printing projects are you currently working on at SEAT?
During a presentation by Felip Fenollosa, director of CIM at the Technical University of Barcelona and an industrial engineer, the potential benefits of additive manufacturing were highlighted, emphasizing its flexibility, adaptability and sustainability. Flexibility has proven to be a remarkable advantage, allowing us to achieve significant development and launch milestones by drawing on our extensive experience. To maximize this capability, a study was conducted in collaboration with EURECAT and RMS, as part of CIAC, to explore the use of 3D printed components as a means of preventing future supply bottlenecks.
In terms of customization, we have successfully created numerous assembly and test bodies to date. Moving forward, our goal is to enter further into this area and take the next leap forward. In the context of sustainability, we have a unique opportunity to create lighter vehicle components by leveraging the limitless design possibilities offered by additive manufacturing. We are currently actively conducting trials in this area as we seek to improve our sustainability efforts.
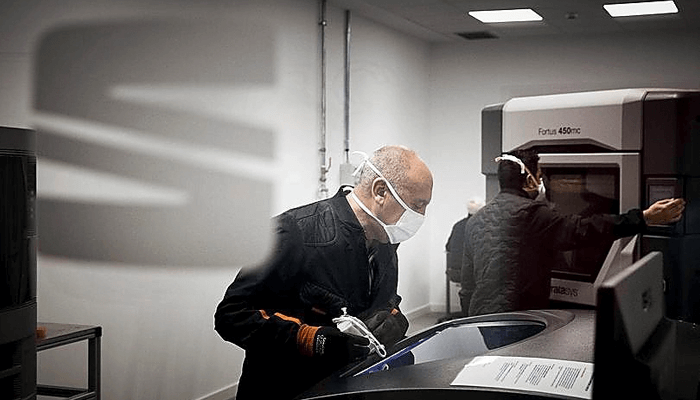
What are the advantages and limitations of additive manufacturing?
The automotive industry has greatly benefited from the inherent flexibility of 3D technologies. The ability to have an assembled and tested part within a week brings significant value to our processes. In addition, when combined with other technologies such as machining, we can acquire different types of tools suitable for almost any application. However, it is important to recognize the limitations of these technologies, such as the relatively high cost of materials and lower productivity compared to traditional manufacturing methods. At present, it remains unlikely that these technologies will be widely used for mass production purposes.
How do you see the future of 3D printing in the automotive industry?
First of all, it is important that all players in the sector understand the potential that 3D printing offers us. The automotive industry is a huge industry, so any improvement, no matter how small, can have a very big impact. With 3D printing, we have the flexibility to implement small changes almost immediately. As materials and processes become more powerful and repeatable, we can get even more out of them throughout their life cycle.
As an automotive company, we often use 3D printing for our internal processes. Steve Jobs once said that the best technology is the invisible one. So I would encourage you to keep looking and thinking about ways to improve our lives with these "magic machines".
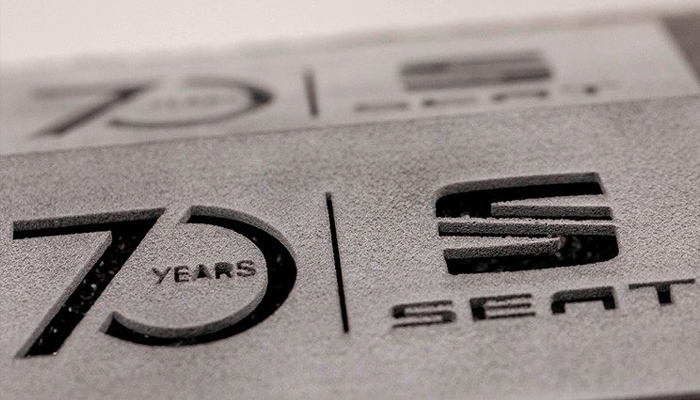
0 Comments