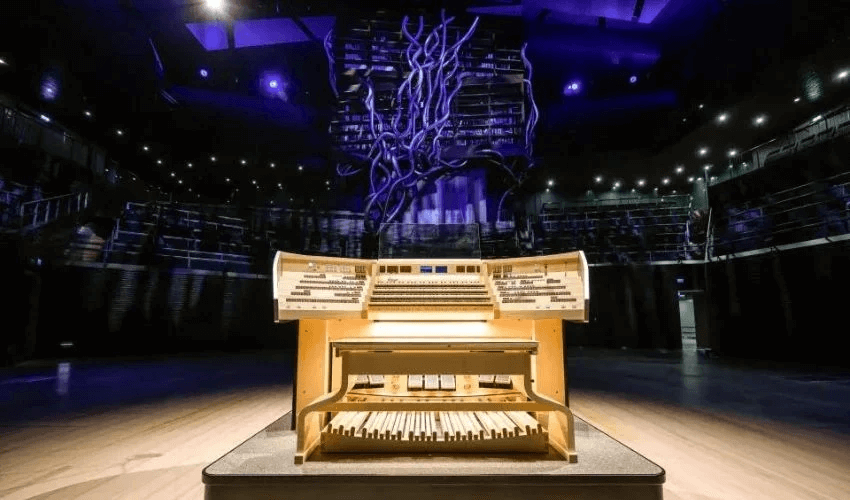
Every year on January 1, concerts around the world welcome the New Year in a lively and musical way. The traditional New Year's concert of the Vienna Philharmonic, for example, attracts millions of people every year who do not want to miss the traditional concert. But other cultural centers and capitals also attract attention with their musical performances at the beginning of the year. At the Helsinki Music Center, a 3D-printed organ by organ builder Rieger celebrated its premiere on January 1 and set the mood for 2024. French musician Olivier Latry was on the bench for the organ's unveiling, and the 3D-printed Rieger organ is expected to be used by other international famous musicians in the following concerts.
The 3D printed Rieger organ is not only the largest organ in Finland and all of Scandinavia, but also one of the largest in the world. It combines elements of traditional organ building with modern 3D printing technology and has a total of over 260 meters of sounding pipes and brass lines. They are made from 100% recyclable Finnish biocomposite UPM Formi 3D on a wooden base for a special sound. The Rieger organ is also visually impressive as the pipes and wind lines are woven into a modern sculpture in front of the organ case.
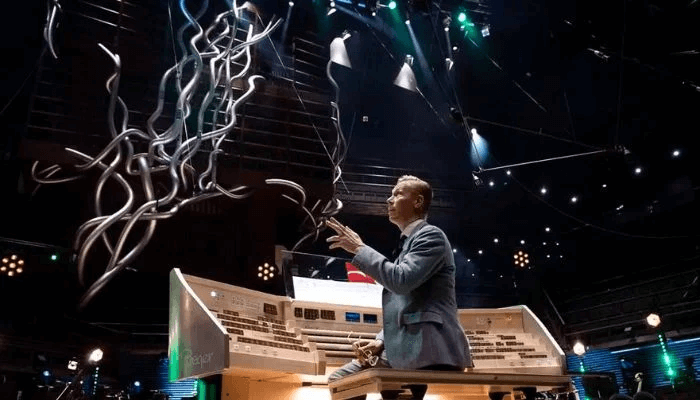
In terms of sound, the organ covers a wide spectrum. Being a hybrid organ, it follows neither geographical nor musical-historical sonic ideals and allows for a varied repertoire. It offers a variety of features for sound capabilities and playing technique. The movable soundboard, for example, turns the organ into a super synthesizer that controls the sound. This is of particular interest to organists who specialize in more modern works. Listeners could enjoy a variety of sounds, with the program ranging from Johann Sebastian Bach to the Romantic era and the 20th century.
"One of our goals throughout the project was for the sound of the organ to envelop the listener and reach the skin," explained the Finnish virtuoso Jan Lehtola, who has been involved in the project from the beginning. However, the aforementioned goal was also associated with a number of challenges.
On the one hand, concert hall organs have not always shown their worth, as the acoustics in concert halls are much more sensitive than in churches. Also, organs need space to work in order for their sound to fully develop. If an organ is placed with its back to the wall, for example, this results in a loss of sound and leads to an unsatisfactory sound experience. In addition to the serious challenges, there were also financial obstacles. Although Musiikkitalo, which was completed in 2011, envisioned a concert organ from the beginning, the organ project was only able to take shape in 2015 due to financial reasons.
From the idea to the finished 3D printed organ
The instrument has come a long way before its completion, both in terms of time and geography. The 3D printed Rieger organ is an international project that involved a group of expert organists from the start. The last organ with its 124 parts is the result of a collaboration between Finland, Spain and Austria. UPM of Finland supplied the biocomposite material used, which was printed into a mold in Burgos, Spain. The 3D-printed pipes were then sent to organ builder Rieger in Vorarlberg, who were commissioned to build the organ.
After the organ was handcrafted, the parts were shipped to Helsinki and reassembled in the concert hall. Each pipe is adjusted on site, so it's hardly surprising that building an organ takes several weeks to months. The project was completed in late 2023 and the 3D printed organ was officially unveiled just recently. “The organ sounds magnificent. It is wonderful to open the concert hall to the public and enjoy both the music and the visual experience that our new organ and performers will provide from January,” comments Kaisa Näreranta, executive director of the Helsinki Music Center Foundation and head of the Organ project
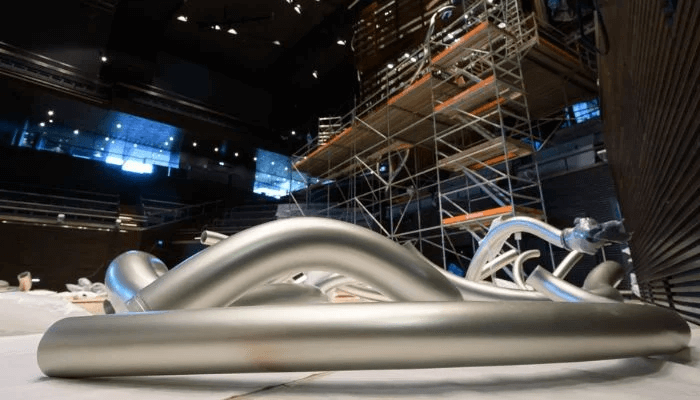
The manufacturing process and material played a role in the sound. The wood-based biocomposite used has acoustic properties and is ideally suited for large-format 3D printing as it shrinks very little and cools quickly. A sustainable approach was also adopted for the organ project. The material is 100% recyclable and 3D printing is also considered a sustainable manufacturing method.
However, there were other reasons behind the decision to use additive manufacturing for the body. 3D printing is reliable, flexible and cost-effective. The latter played a particularly important role, since the cost of the organ project amounted to more than 4 million euros, of which about 3.17 million were spent on the production of the instrument alone.
To promote the project and produce more organ concerts, the Helsinki Music Center Foundation launched a campaign to name the organ pipes. Materials manufacturer UPM is also participating through its Biofore Share and Care program, highlighting its support for the arts: "At UPM, we have a long tradition of supporting the arts and wanted to participate in the Helsinki Music Center Foundation's donation campaign. We named all the fantastic front pipes of the organ,” concluded Hanna Maula, Vice President of Communications at UPM.
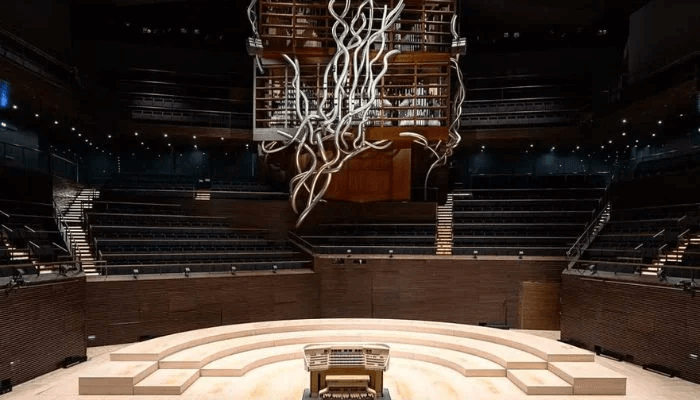
0 Comments