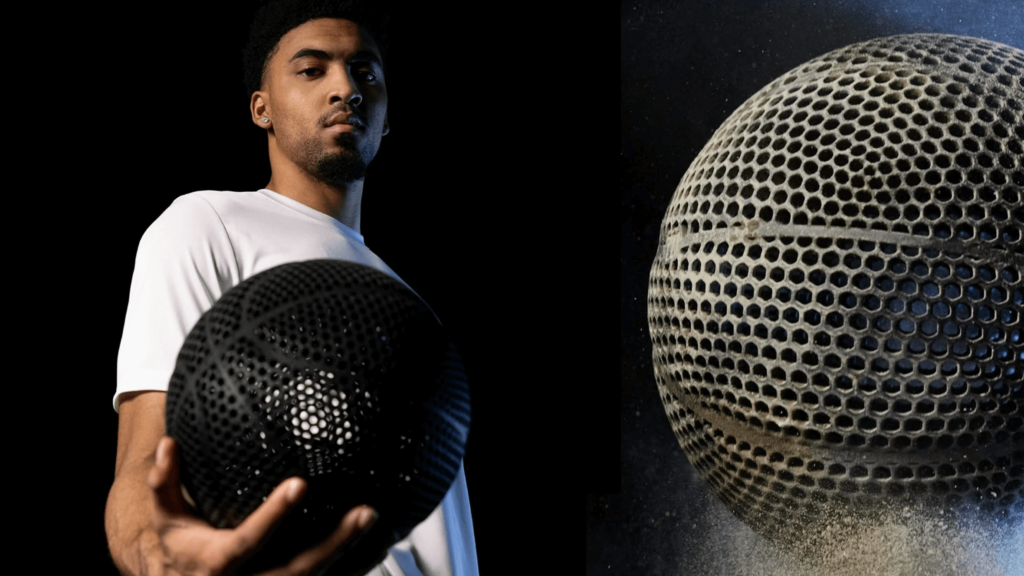
Wilson's basketball prototype may be the first of many innovative twists on the company's traditional sports equipment.
During the recent NBA All-Star Weekend, which featured the wildly popular All-Star Game pitting Kyrie Irving and Donovan Mitchell against Stephen Curry and LeBron James, you'd be forgiven for not noticing the odd black ball that player Kenyon Martin Jr. used for his second attempt in Saturday night's dunk contest. It took three tries, but he nailed it in style.
The prototype basketball was from Wilson Sporting Goods, which produced the standard, leather official NBA basketball from 1946 until it was replaced by rival Spalding for 30 years, but regained the title in 2021.
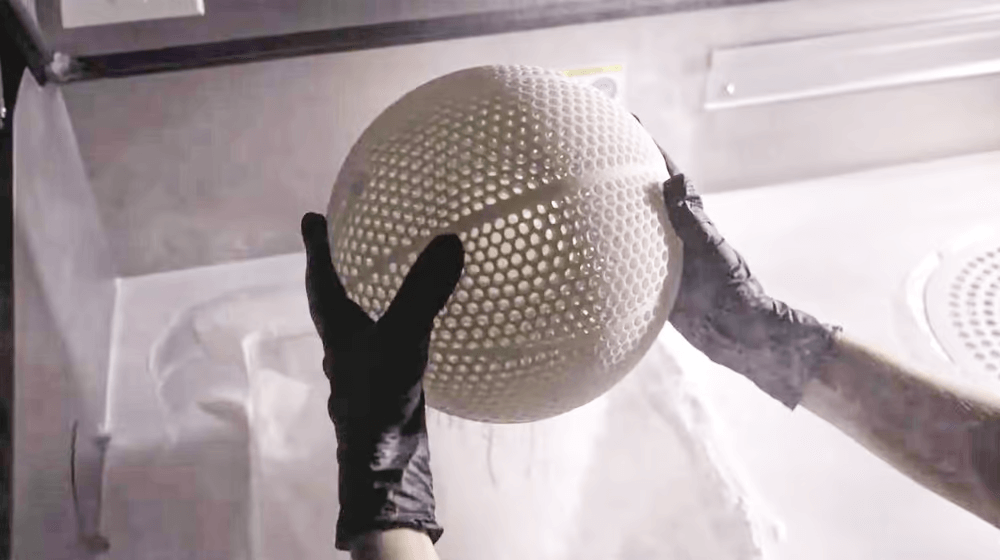
The 3D airless basketball prototype, as it's called, "almost" meets the performance specifications of a standard basketball, including its weight, size and rebound (bounce), according to the company. The ball does not need to be inflated as it consists of a solid transparent grid with eight panel-like sheets.
The debut of the prototype is designed to show the sports company's "continued commitment to sports innovation," says Wilson, but it won't replace the official Wilson NBA game ball anytime soon.
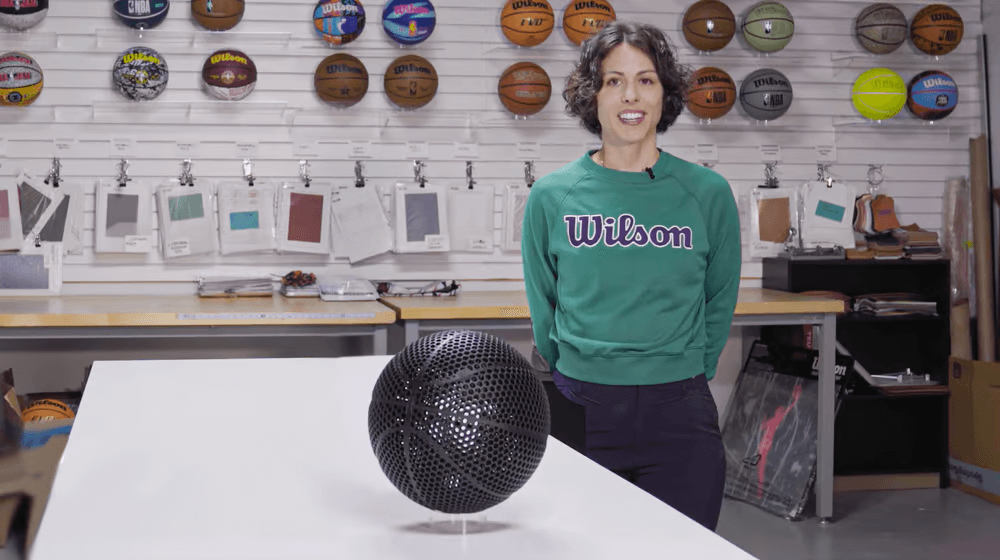
Why 3D print a basketball?
Whether the 3D Airless Prototype Basketball was an advertisement to millions of sports fans or a preview of a product in development, Wilson may have a hard time selling the material change and shape change to NBA players.
In 2006, then-official ball manufacturer Spalding introduced a synthetic basketball that testing showed offered better grip and more consistent bounce than the leather standard. Despite his progress, he was outright rejected by NBA players and traded midway through the season. It didn't feel the same, the players said.
The Wilson Labs team created the 3D Airless Prototype Basketball design at the brand's Innovation Center in Chicago. General Lattice provided computational design services and DyeMansion provided color and finishing solutions.
What Wilson's new prototype ball does well is demonstrate the technical capabilities of 3D printing and the materials it uses. The ball is printed in one piece using selective laser sintering (SLS) technology on an EOS 3D printer and has a flexibility that many consumers don't associate with 3D printed products.
"This is just a point in the development journey," says Bob Thurman, vice president of innovation at Wilson. Will it become the core of a leather basketball or a puncture-resistant consumer product that will never deflate? Time will tell.
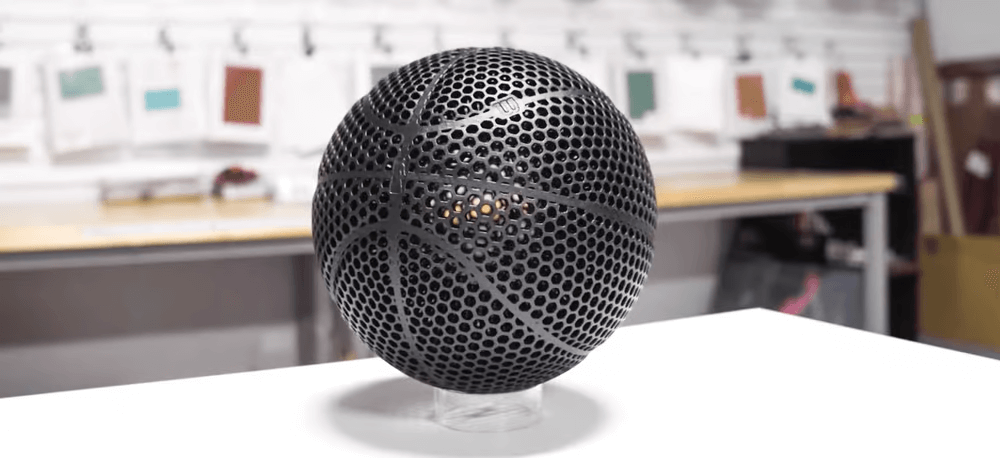
"There's still work to be done before it's ready for floors around the world," Wilson said in a statement, "but we're excited about the possibilities this ball presents. Opportunities for other sports and future Wilson products, revolutionary sustainability through additive manufacturing... This is an innovation made to push the boundaries and open the imagination.”
0 Comments