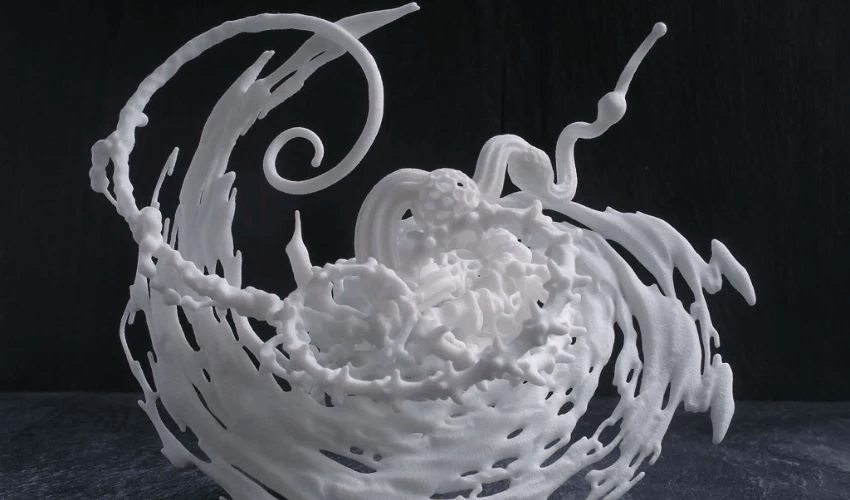
In additive manufacturing, avoiding printing errors is paramount, regardless of what technology is used. And for both beginners and experienced users, there are various traps they can fall into that make their part less than desirable. One of these extremely important but often overlooked considerations for 3D printing is wall thickness.
Not to be confused with infill or layer height, wall thickness refers to the measure of the thickness of the outer wall or casing of a 3D printed part, excluding the top and bottom. Unlike internal structures, which can vary in strength (usually determined by percentage and template), walls are always rigid and play a critical role in providing stability and strength to a part. But what is the minimum wall thickness? How can users know if their settings are correct? Why does it matter? We took a closer look at these questions and more.
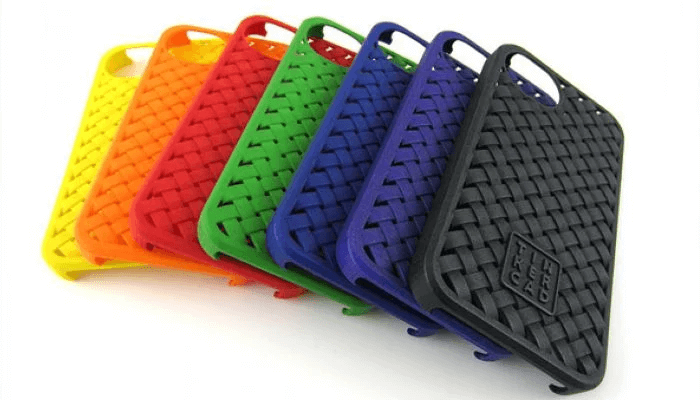
Why is wall thickness important in 3D printing?
Now you may be wondering, with so many different parameters to keep track of when 3D printing, what makes wall thickness so important? Well, it is crucial to ensure not only aesthetic qualities, but also strength and durability. If the wall is too thin or too thick, the part may not work as intended. Indeed, some say it may even be more important than the infill to the quality of the final 3D printed part.
There are many factors it can influence. For example, as with many of these 3D printer parameter optimizations, one of the main benefits of having the right wall thickness in 3D printing is that it will help prevent warping. This is because it can help reduce internal stress. Indeed, it is generally safe to say that the danger of the walls being too thin is that the parts will be brittle and therefore more likely to break, crack or deform during or after printing.
Walls that are too thin can also be negatively affected by post-processing. Especially if they are used subrheavy constructions or processes are required such as steam ironing , thin walls will not survive. In this case, it is extremely important to ensure that you meet the minimum requirements for the material.
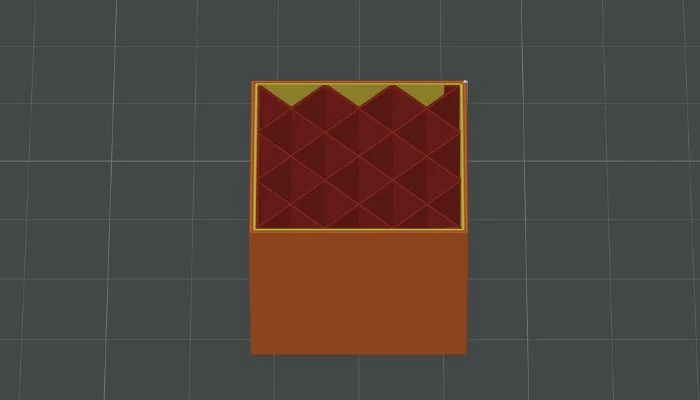
Walls that are too thick can also cause problems. It should be noted that if you have extremely thick walls, you waste material and money, and the print will take longer to complete. But there may be other impacts.
For example, walls that are thick enough are critical for reducing internal stress, but with some materials (metals for example), too much material can also cause more internal stress. This can also cause plastic parts to crack. Walls that are too thick can also cause problems with heat dissipation in the part. Also, the thicker the walls, the greater the shrinkage of the stamp material, which also leads to warping.
How to determine wall thickness
As mentioned above, wall thickness refers to the thickness of the shell of a 3D printed part, with both too thin and too thick walls causing problems. This is a factor in all 3D printing processes, but we want to focus specifically on FDM 3D printing. However, it should be noted that thickness is related to the material, not the process.
This means that even with certain rules, there will still be minimum and maximum requirements that users need to keep in mind. For example, a material like PLA has a minimum wall thickness of 0.8mm (although in some cases it can be lower), but the ideal is closer to 1.5mm. The range for many other solids is similar. Meanwhile, rubber-like materials like TPU should have a larger wall thickness, around 2.0mm, but if you want your part to be flexible, users don't want walls that are too thick, as it will make the part bulky.
However, there are a few tricks you can use, especially for determining wall thickness when using FDM 3D printing. They refer in particular to the nozzle. A common determinant of wall thickness is a multiple of your nozzle diameter.
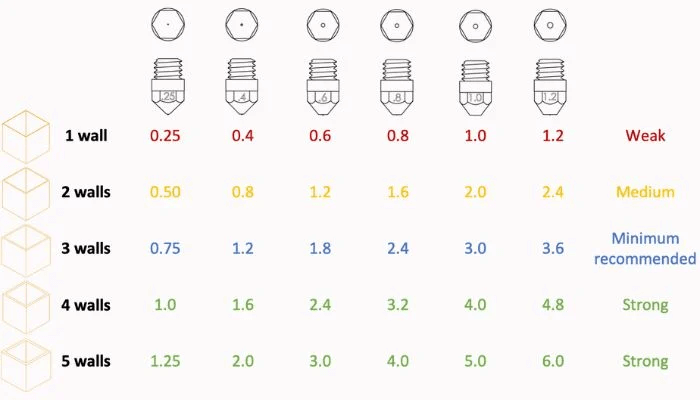
Since most FDM print nozzles are around 0.4mm, many recommend a wall thickness of at least 0.8mm, or about twice the nozzle. If you want a stronger part as well, you can increase the multiple to three or four times, or about 1.2mm to 1.6mm. But be warned, it's often advised not to go any thicker than this, with the 'magic range' varying between 0.8-1.6mm for many common plastic materials.
An additional consideration? Try to keep integer multiples of the nozzle. This means users can specify the wall thickness by 2x, 3x, 4x, etc. But if you try to have a wall thickness that is 1.5x the nozzle, it can cause the outer wall layers to overlap and slow down your 3D print.
Useful tools for wall thickness in 3D printing
Although, of course, ensuring consistent and correct wall thickness should not be done alone. Not all 3D modeling software will take wall thickness into account, so it's something users need to keep in mind from the start of their design. This is where slicers can come to the rescue again. 3D printing slicers often have features to ensure that there are no walls that are too thin in the design. This can be essential in finding these problems before printing.
Also, despite these recommendations, the walls can sometimes be thinner than twice the diameter of the nozzle, which is also where slicers are used. For the fine detail found in modern slicers, it allows users to print walls as thin as the diameter of the nozzle. Vase mode is another parameter that allows printing walls the width of the printer nozzle diameter, as this feature (ie vase mode) allows the printer to print vase-like objects in one continuous extrusion , to produce waterproof prints.
In addition, the thickness of the wall can be played with, depending on factors such as support structures. If your part has a lot of support structures, especially in areas that may be particularly fragile, it may be possible to have thinner walls (although remember that removing these structures would be difficult even with walls that are too thin), as these other factors contribute to the strength of the part. Also, higher resolution printers will be able to create parts with thinner walls, although minimum requirements should always be considered.
0 Comments