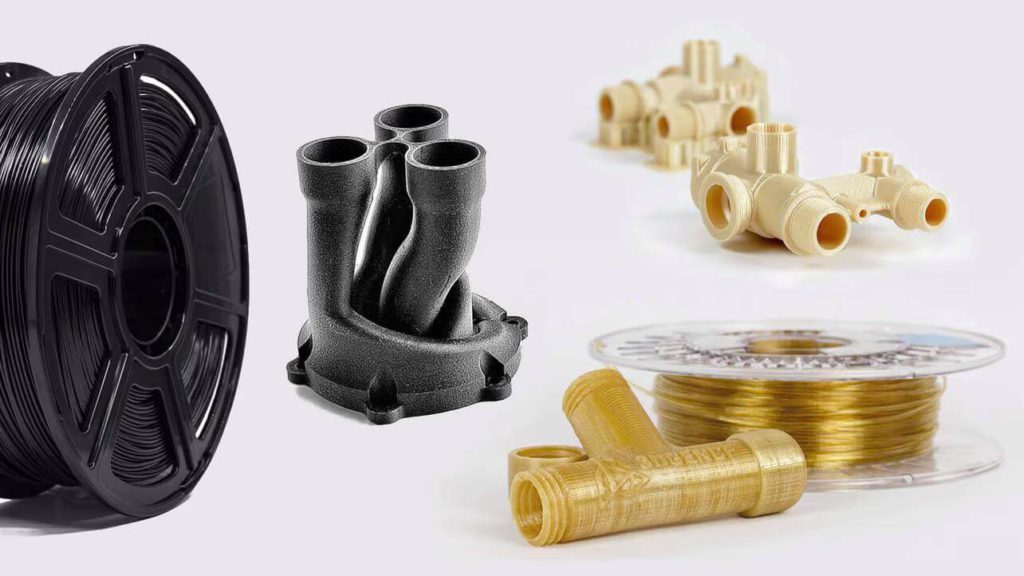
Producing strong, durable, lightweight and corrosion-free alternatives to metal parts requires 3D printed polymers up to the task. Think and move beyond metal!
From aerospace, automotive to healthcare, most industries are moving from metals to non-metals for structural components, equipment parts, implants and tools. High-performance polymers have been proven to outperform their metal counterparts. They are also lighter, cheaper and faster to produce in smaller quantities than metal parts.
3D printed polymer parts can be more durable; more resistant to corrosion, chemicals and heat; have greater impact strength at high temperatures and sub-zero temperatures, and exhibit high electrical insulation and noise-absorbing qualities. Polymers can also be customized and manufactured into shapes often not possible with metal, and 3D printed into monolithic forms, so there is no need for assembly or welding.
There are dozens of 3D printing plastics with varying degrees of strength, durability, wear resistance, heat tolerance, biocompatibility, and other qualities you may need in your final part. But how do you choose the right one?
In this review of high performance materials, we will introduce you to the characteristics of the best polymers used in additive manufacturing today to help you make the best choice.
What are high performance materials?
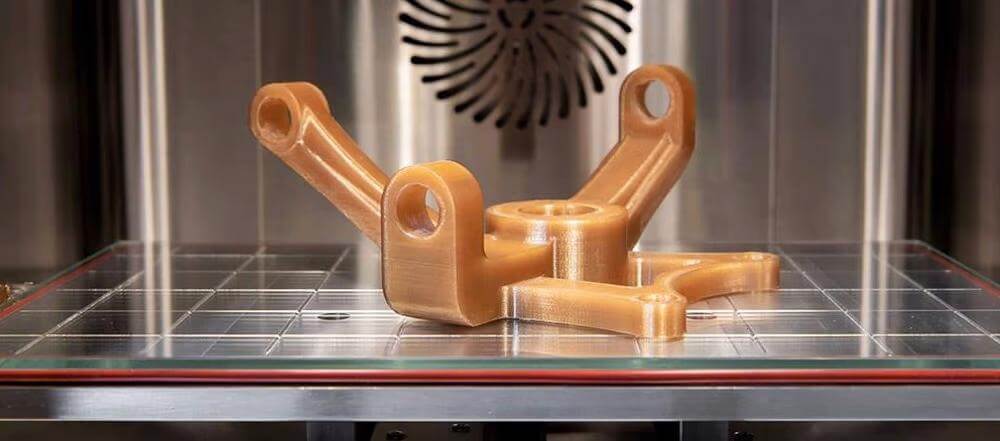
As for plastics, the term "high-performance" is not a scientific classification, and sources disagree about which polymers to include. You may hear terms such as engineering grade, engineering polymers, or performance plastics to refer to materials with higher strength, purity, stiffness, and resistance to wear and chemicals than the most common 3D printing materials, such as PLA and ABS.
In addition to the wide variety of polymer types available is a sea of polymer blends, glass or carbon fiber reinforced polymers, and branded composite materials.
In general, however, you'll find that high-performance plastics are those that retain their desired mechanical, thermal, and chemical properties when subjected to harsh environments, such as high temperature, high pressure, and corrosive chemicals. In other words, they don't bend, warp, crack, or chip.
Commodity or Common Plastics
PLA | ABS | ASA | PP | PMMA | HIPS |
Engineering Plastics
PC | PA | PET | TPU | TPE | TPC | PETG |
High-Performance Plastics
PEI | PEEK | PEKK | PVDF | PPSU |
MECHANICAL PROPERTIES OF ENGINEERING AND HIGH PERFORMANCE PLASTICS
Polycarbonate
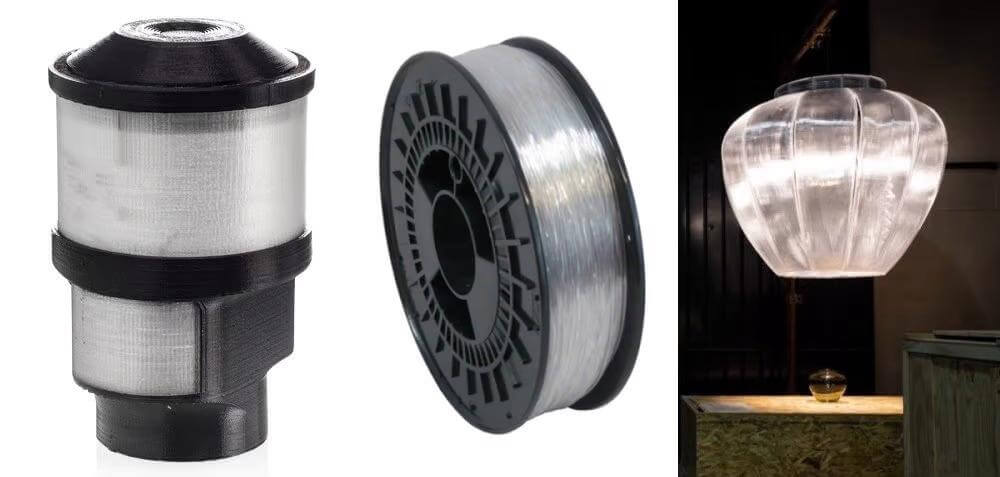
Polycarbonate (PC) is a strong material that stands out with three main characteristics: optical clarity, heat resistance and incredible strength. When 3D printed, it is used in a variety of industries for automotive headlight prototypes, lampshades, and translucent housings for electrical components.
- Highly transparent and glass-like
- High durability down to -20 °C
- High mechanical retention up to 140 °C
- Proprietary flame retardant
- Good electrical insulation properties that are not affected by water or temperature
- It has good abrasion resistance
- Withstands repeated steam sterilizations
PA (Polyamide, Nylon)
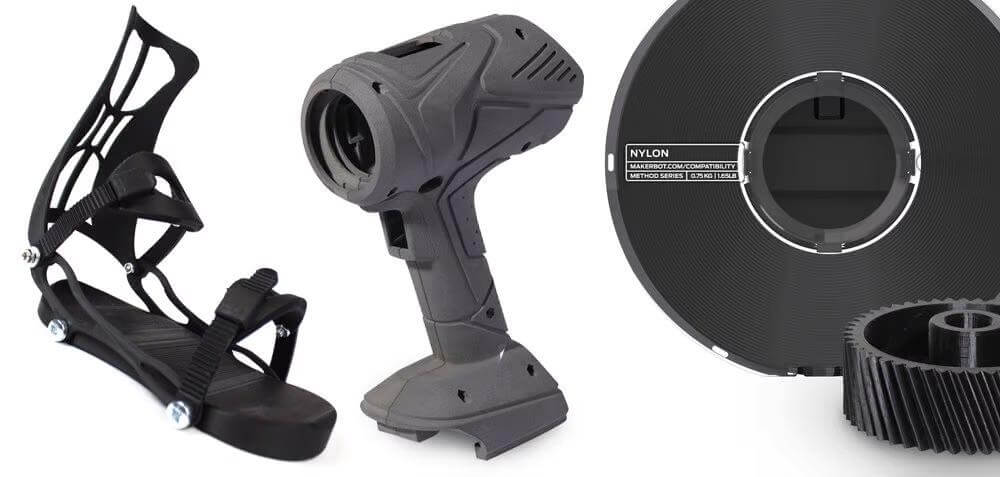
Polyamides (also called nylons) as a class of plastics – available in PA6, PA11, PA12 and others – are valued for their good balance of properties. Typically petroleum-based (except for PA11, which is a bioplastic), they exhibit both strength and wear resistance while being easy to work with. PA is usually reinforced with carbon, glass and Kevlar fibers or embedded with continuous carbon fibers for additional reinforcement. Widely used in high-end engineering applications such as gears, fixtures, welding fixtures and tools, PA is available as filaments and powder.
- High strength and hardness at high temperature
- Good impact strength, even at low temperature
- Very good flow for easy processing
- Good resistance to abrasion and wear
- Highly resistant to fuel and oil
- Good electrical insulation properties
- High resistance to cracking, aging and abrasion
- Highly water absorbent
- Vulnerable to mineral acids and solvents
PETG / PET (polyethylene)
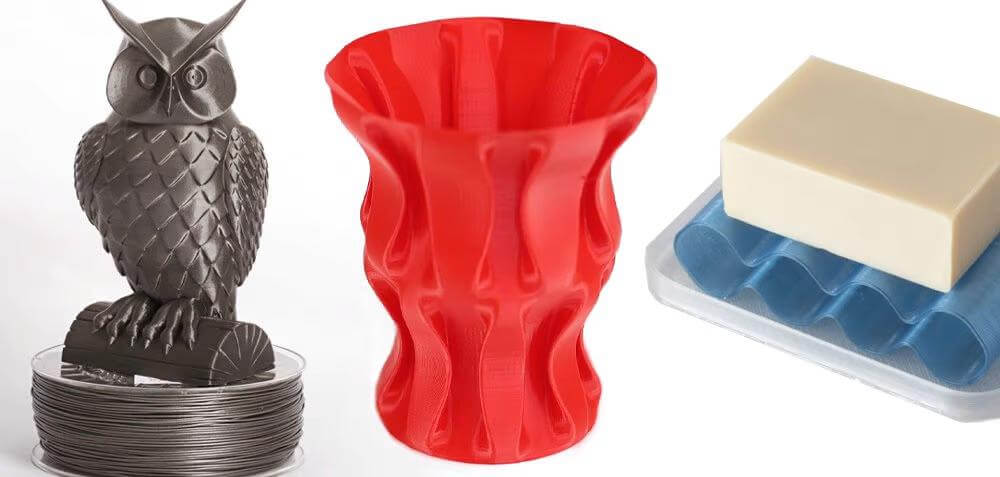
PET and PETG are from the same polyethylene terephthalate family. PET is one of the most used plastics in the world, especially for food and beverage packaging, but it is not very popular for additive manufacturing due to its low heat resistance. PETG, on the other hand, is widely used for 3D printing due to its significant chemical and heat resistance, good durability and formability (compared to other plastics). Probably not an engineering polymer due to its low strength, the wear and impact resistance of PETG makes it suitable for a number of industrial applications where cost-effective plastic is a priority. Applications for PETG include gears, pointer and graphic displays, and electrical equipment boxes.
PETG
- Significant resistance to chemicals and heat
- Good durability and shape
- Only moderate hardness and strength
- Food safe and non-toxic
- Transparent and has a glossy finish
TPE / TPU / TPC (thermoplastic elastomers)
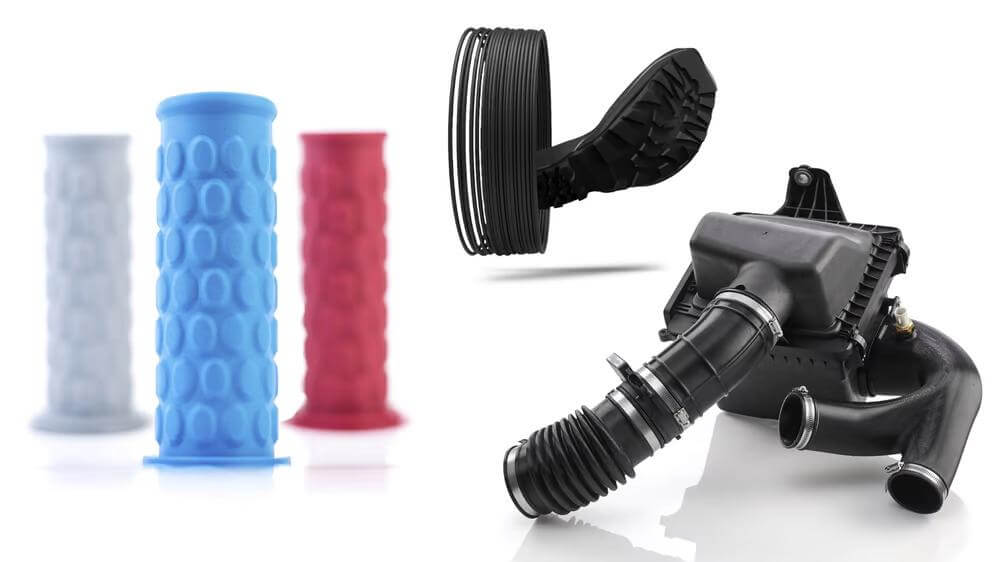
TPEs (Thermoplastic Elastomers) are a class of materials that are a blend of plastic and rubber, and include TPU (Thermoplastic Polyurethane), TPC (Thermoplastic Copolyester), and others. These plastics are very soft and flexible. They are becoming increasingly common in additive manufacturing to produce parts that can be bent or stretched without any deformation. TPUs are also generally more durable and can offer greater resistance to abrasion, oils, chemicals, and high and low temperatures than TPE filament. TPC boasts high temperature resistance and excellent UV resistance. It is particularly valuable in biomedical applications and for wearables and medical devices. TPEs are available in filament, powder, and resin.
- High elasticity throughout the hardness range
- Excellent low temperature and shock resistance
- Resistant to oils, greases and solvents
- Weather resistance and high energy radiation resistance
- Very good electrical insulation properties
- It can be produced in different degrees of hardness
PEI (polyetherimide / Ultem)
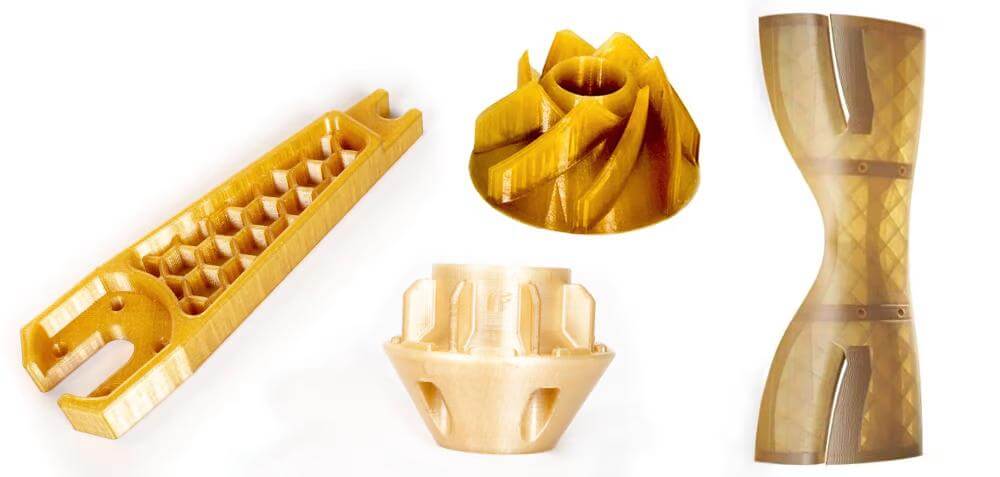
Polyetherimide (PEI) was first developed in 1982 by the General Electric Company (now known as SABIC) under the trade name Ultem, as it is still widely known. This high performance plastic is characterized by exceptional thermal, mechanical and electrical properties. PEI offers manufacturers a high strength-to-weight ratio, making it a cost-effective metal alternative that is strong enough to replace steel in some applications and light enough to be used in others to replace aluminum, particularly in aerospace space. Other PEI applications include gear components, valve bodies, sensor and thermostat housings, demanding electrical applications, printed circuit boards and camera devices. There are many grades of Ultem, the most common being Ultem 1000. Ultem 1010 is resin and Ultem 2300 is glass reinforced 30%.
- Very good retention of mechanical properties at extremely high temperatures
- Outstanding specific strength, stiffness, flexibility and dimensional stability
- Good electrical properties
- Good resistance to UV rays and weathering
- Inherently refractory
- Resistant to alcohols, acids and hydrocarbon solvent, but dissolves in partially halogenated solvents
- PEI also shows good hydrolytic stability
- Works especially well in hot air and water environments
- Most PEI grades are compatible with food contact
PEEK (polyetheretherketone)
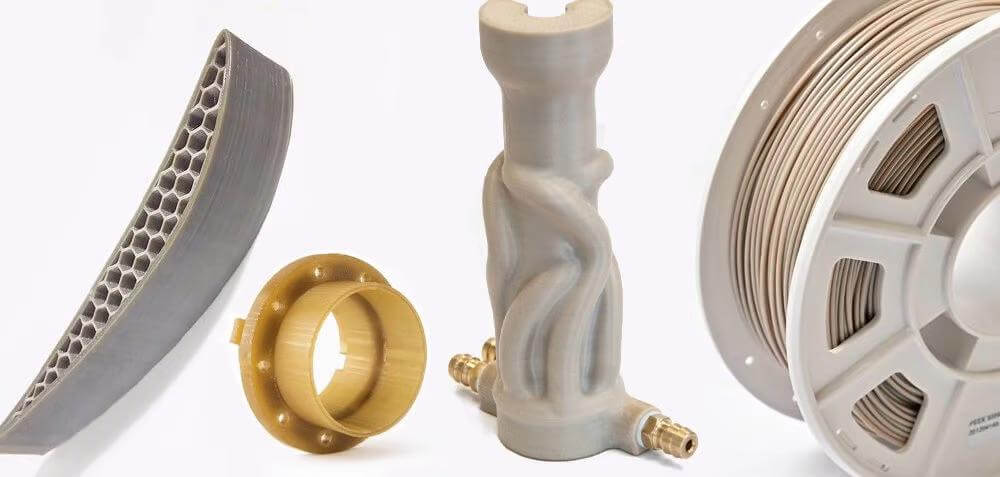
PEEK belongs to the polyaryletherketone (PAEK) family of polymers and is enjoying increasing popularity for applications in military, pharmaceutical, petrochemical and food packaging. However, its high cost and complex processing limit it to industrial use with specific printers. PEEK has less than half the weight of aluminum and one-sixth that of steel, making it excellent substitutes for metal spare parts in the oil and gas and aerospace industries. The properties of PEEK can be further enhanced by combining it with composite materials such as glass fiber, graphite or carbon reinforcements that help combat shrinkage. PEEK is also used for medical implants (as it is fully biocompatible and X-ray transparent), but there is a huge difference between industrial and implantable PEEK, with Evonik offering the only fully medically approved PEEK filament on the market to date (priced around 5000 $ /kg).
- Extremely resistant to extreme temperatures up to 260°C
- Resistant to corrosive liquids, gases and high pressure
- Highly resistant to water or high pressure steam
- High self-lubricating ability and low friction
- Exceptional resistance to resistance
- Good dimensional stability
- Low flammability and low smoke on combustion
- Exceptional insulating properties
- Excellent resistance to sterilization at high temperatures
- Completely biocompatible
PEKK (polyether ketone ketone)
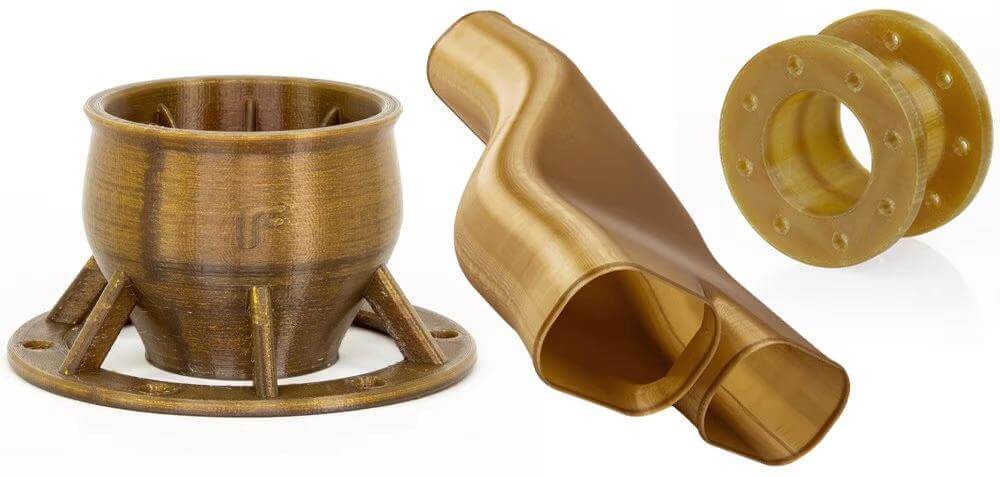
PEKK is another polymer in the polyaryletherketone (PEAK) family and is one of the most effective polymers in the world. PEKK has extremely good mechanical, thermal and chemical resistance properties, but boasts much easier printing than PEEK. In fact, PEKK can be processed at lower 3D printing temperatures than PEEK-based filaments, does not require an overheated chamber (like PEEK), and has excellent layer bonding, resulting in parts with exceptional dimensional accuracy and z-strength. It is another versatile high-performance 3D printing polymer that can replace metal and composite parts in a variety of industries, from aerospace and automotive to medical and marine. The material is resistant to hydrocarbons and liquids.
Parts printed with PEKK can be heat treated (annealed) after printing to achieve maximum mechanical, thermal and chemical resistance properties. The printed parts will be transparent golden in color and after annealing will acquire an opaque complexion.
- High temperature resistance of 255+ ºC
- Very high hardness, tensile and compressive strength, impact resistance
- Easy to print
- Flame retardant, low outgassing
- Very limited distortion
- Resistant to almost all organic and inorganic chemicals
PVDF (polyvinylidenefluoride)
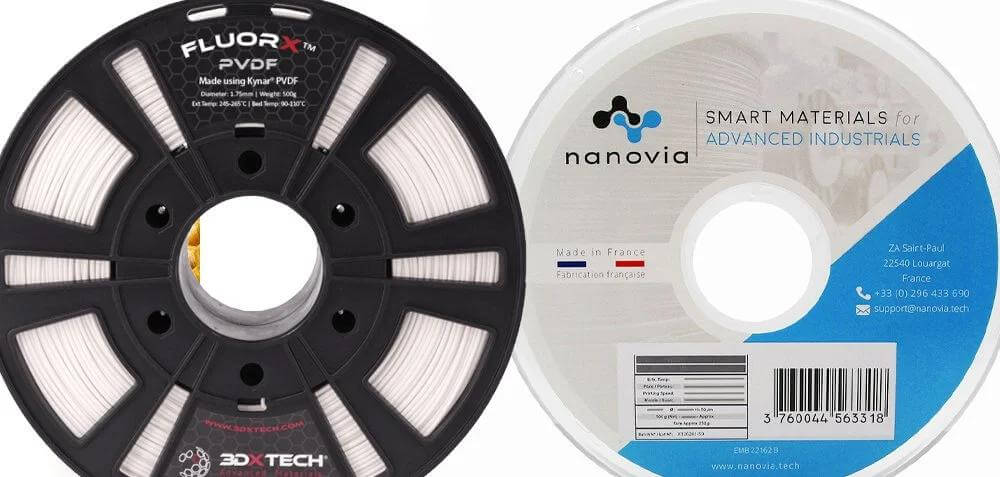
PVDF (Polyvinylidene Fluoride) is another polymer gaining application in additive manufacturing because of its unique set of properties. PVDF is widely used in high-tech applications such as chemical process equipment, semiconductors, lithium-ion batteries and other electrical, electronic and energy applications. In 3D printing, PVDF shows very low deformation and withstands the most extreme conditions, even nuclear radiation. PVDF panels are used for space probes and satellites.
- High thermal properties up to 150 °C
- Very low distortion
- Excellent resistance to most chemicals, including fully halogenated hydrocarbons, alcohols, acids and bases
- Non-hygroscopic, does not absorb moisture.
- Long-term hydrolytic stability
- Resistant to nuclear radiation
- Very good abrasion resistance
PPSU (polyphenylsulfone)
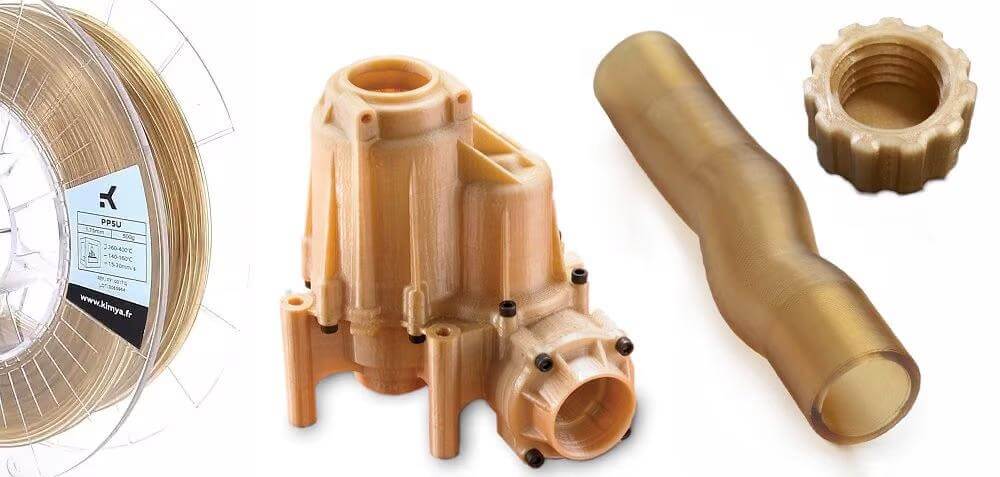
Sulphone polymers (PPSU, PESU, PSU) are another family of high-performance plastics that combine excellent thermal stability, high strength and durability, excellent hydrolytic stability, transparency, and good resistance to environmental stress cracking. Distinguishing them from the PEAK family is their high heat deflection temperature (similar to PEI) and they are the only thermoplastics that remain transparent at super high temperatures (204 ºC), even after long-term exposure. PPSUs provide long-lasting performance in hot water and steam, even under pressure, so they are often used to replace brass in pressurized hot water applications. They can be used as a lightweight alternative to metal in surgical sterilization boxes and trays, implants, surgical instrument handles, and numerous other medical and dental devices.
- Exceptional long-term resistance to resistance at temperatures up to 150 ºC.
- Easy to handle
- Excellent wear resistance under long-term loading at high temperatures
- Resistant to acids, bases, oils, greases and aliphatic hydrocarbons and alcohols.
- Good optical clarity
- Very good hydrolytic and sterilization resistance
- Biocompatibility
- Excellent insulating properties
- Exceptional hardness even at high temperatures
- Low resistance to UV light
What are high performance plastics used for?
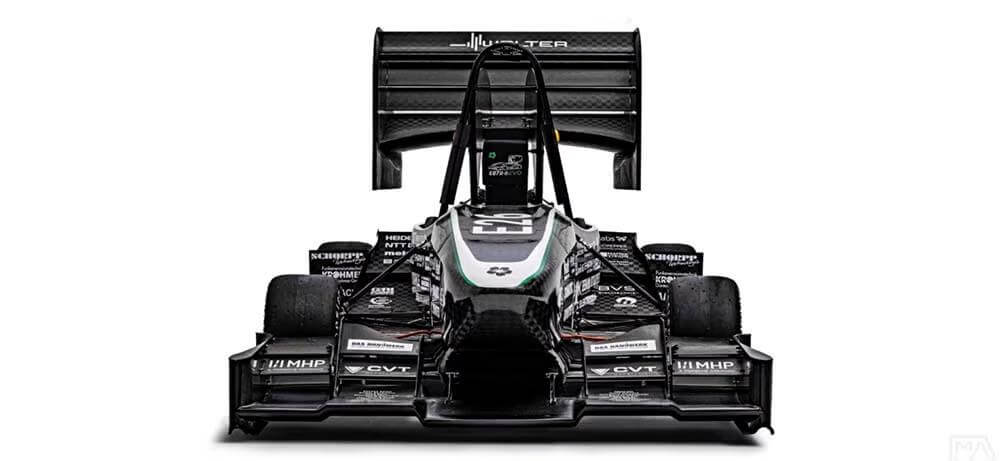
High-performance plastics are most often used for end-use, functional parts due to their high cost. They are also used as functional prototypes for parts that will eventually be made of metal, glass, or parts that will be mass-produced, such as automotive parts prototypes. They are an alternative today as a substitute for expensive and environmentally unsustainable metals, such as copper, brass, titanium and aluminum. High performance polymers are resistant to oxidation, corrosion and chemical contamination.
Rapid prototyping in motorsports
In an industry that relies on multiple experimental design iterations, the ability to quickly print a prototype part that can actually withstand functional testing devices allows racing teams to innovate faster. Additionally, increasingly high-performance 3D printed end-use parts are finding a place in electric racing cars due to the non-conductivity of the material.
Lightening in outer space
Replacing metal parts with strong, high-performance plastic parts has been shown to dramatically reduce the weight of aircraft, spacecraft, and satellites, resulting in fuel and size efficiency. High-performance plastics combined with generative design have resulted in parts like brackets and walls that use fewer materials but are stronger than aluminum. High-performance plastics, such as PEEK, which has a useful temperature range of -184 ºC to 149 ºC, are ideal for the harsh conditions of outer space.
Molds and tools for rapid production
3D printing complex injection molds and tooling, especially for one-off or short-run production, is significantly cheaper and faster than CNC milling. In addition, there is no material waste and fast 3D printing allows manufacturers to offer more customized options to their customers.
Manufacturers are finding that high-performance plastics are more than a match for metals in machine assembly processes, plus they can be printed on-site or at a 3D printing service desk faster and at a fraction of the cost.
Patient-specific implants
Biocompatible high-performance polymers are used in countless custom-designed implants to meet specific patient needs. Additive manufacturing produces these parts faster and with less material waste than milling/turning. 3D printed PEEK is used in bone replacement patients due to its osseo-integration.
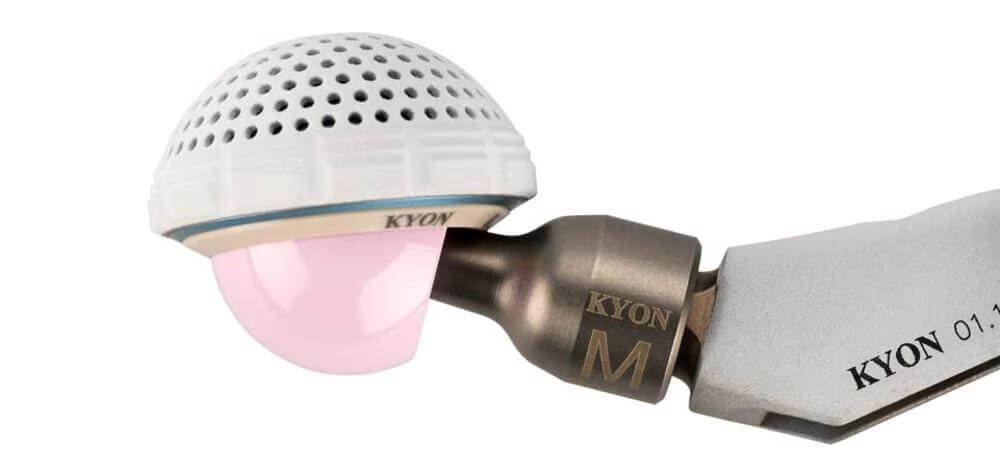
One important point to consider when shopping for high-performance materials is whether the final part you make will be used in a regulated industry. Just because PPSU is biocompatible does not mean that all PPSU filaments are certified and approved as medically biocompatible. Individual material manufacturers must submit their specific materials to regulatory authorities for approval, so be sure to check that your brand of filament comes with these approvals.
0 Comments