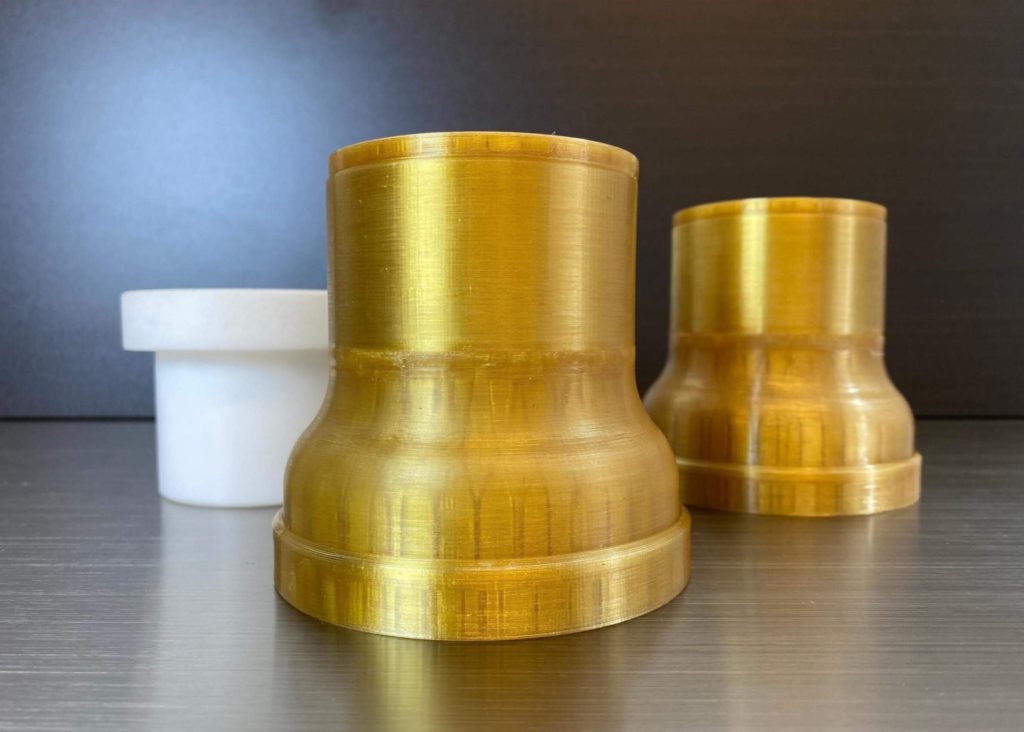
CHANGING THE PRODUCTION LINE WITH 3D PRINTING
Our/Vodka is a global company that produces vodka in micro-distilleries around the world. Their concept is to allow their international partners to put their own brand on products by manufacturing them locally. As the business progresses and expands with new products, new distilleries are needed. 3D printing is very useful in modifying equipment in the company's various facilities.
At Our/Vodka's facilities, in addition to distillation, the manipulation of the brand's carefully designed glass bottles takes place. Bottles must be thoroughly rinsed before being filled and sealed. Thoalfiqar Abbas works to set up and operate microdistilleries in the US and contacted our partner, 3DVerkstan in 2018. Since then, 3DVerkstan Studios has collaborated with them, creating various 3D-printed solutions. As the product range at Our/Vodka is constantly expanding, this means that existing equipment and tools also need to be constantly updated.
“- As we are constantly changing and bringing new products to market, we usually have to quickly and efficiently adapt our equipment to cope and streamline production. Our equipment was originally designed for one specific purpose. When we started to reconfigure our facility, 3D printing provided a flexible and relatively inexpensive solution,” says Thoalfiqar.
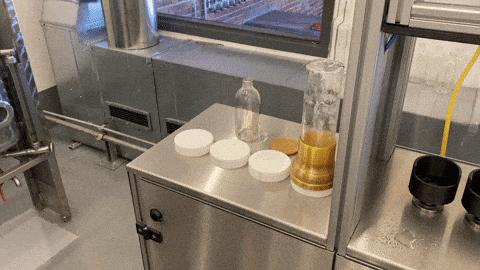
FOOD SAFE MATERIAL
What Thoalfiqar was looking for were custom holders for one of their new product solutions. First, the bottles were scanned with a 3D scanner so they could model the parts according to shape and size. The design of the parts is then determined after extensive testing and reworking and then printed.
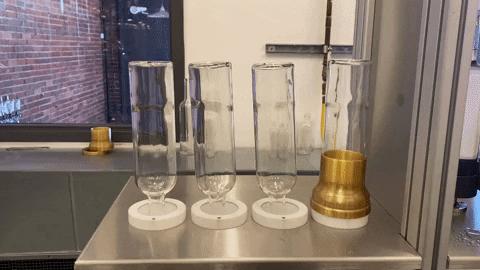
For Our/Vodka, an important requirement for food contact parts, in addition to the design, is that the material on which the part is printed must be FDA (US Food and Drug Administration) approved. The solution must improve efficiency and at the same time maintain the same high quality and standard. This is possible through 3D printing of high performance polymers . One of the requirements is that the material is "food grade". Since the product comes into contact with the alcohol in the bottles, it was chosen Kimya PEI1010.
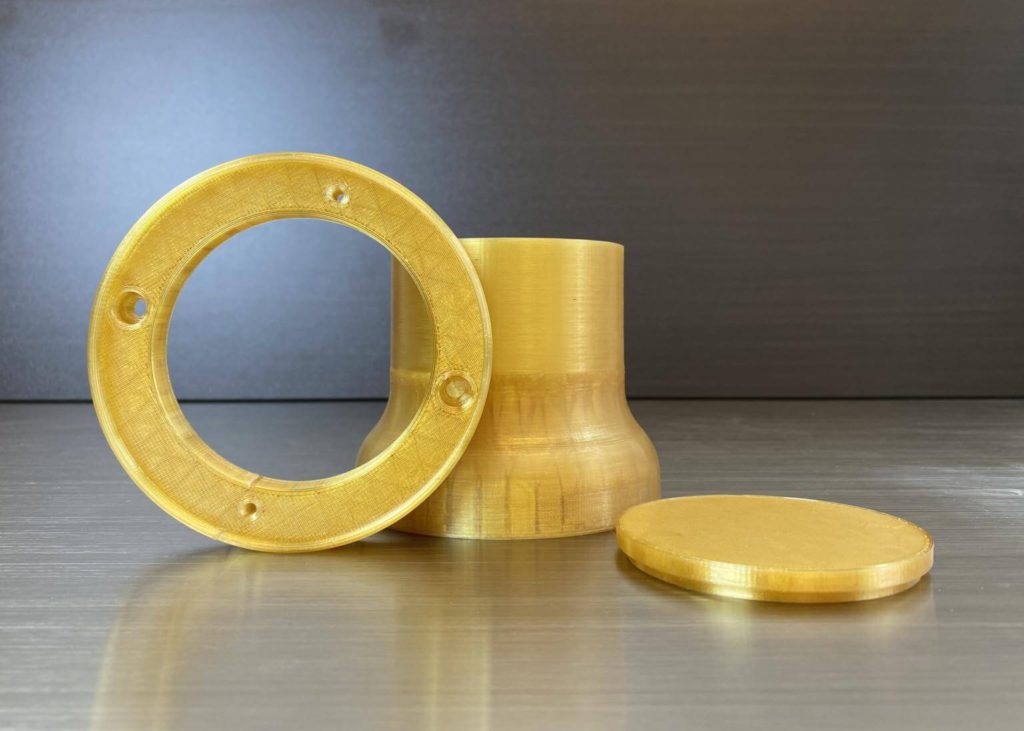
ADDED VALUE IN DEVELOPING BUSINESS
In addition to FDA approval, the material must also be extremely durable and have high chemical resistance. PEI1010 is a food-grade material that also has good heat resistance as well as great chemical resistance, both of which are aspects of the material that are needed for sterilization, for example. In this case, this was necessary as the parts must be sterilized before use. Even if the material is FDA approved, the machine that prints the part is not. Therefore, the parts are treated in 96% ethanol before use.
3D printing is a great solution for a changing business. The finished parts are adaptable and can hold bottles of different sizes. They are also designed to be installed on existing equipment. In a business like Our/Vodka, which is constantly changing and evolving, 3D printing provides a clear added value.
0 Comments