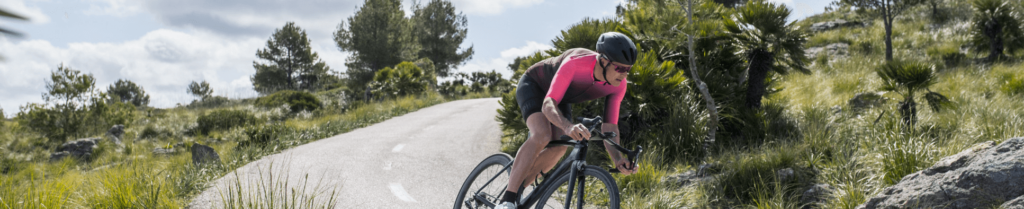
Специалистът по материали Lehvoss Group си партнира с производителите на E-bike Buddy Bike и Isoco Bikes, за да разработи E-bike Isoco X1.
Продаван също като Buddy X1 , E-bike велосипед е проектиран с мисъл за устойчивостта. Съобщава се, че термопластичните рамки на велосипеда имат 68% по-нисък въглероден отпечатък от традиционните алуминиеви рамки.
В допълнение, рамките са 100% рециклируеми, като същевременно са леки и издръжливи. В края на техния жизнен цикъл материалът може да се използва повторно в производството на нови висококачествени компоненти.
Директорът по маркетинг на персонализираните полимерни материали на Lehvoss, Томас Колет, каза, че 3D печатът е използван за разработване и прототипиране на някои от частите на ISOCO X1.
Произведени чрез комбинация от леене под налягане и fluid injection technology (FIT), рамките ISOCO X1 са по-леки от техните алуминиеви “колеги”. Термопластичните пластмаси от въглеродни влакна от Lehvoss се използват в производствения процес. Според ISOCO, това са първите шприцовани рамки за велосипеди от въглероден композит, които излизат на пазара.
Устойчивият E-bike в момента се подлага на тестове като част от експедицията Lehvoss Xtreme-Tech, 1300 км цикъл през Северна Африка. Колоездачите Майк Фукс, Оливър Геркинг и Дейвид Арландис участват в мисията, която има за цел да докаже дали термопластичните велосипедни рамки и компоненти могат да издържат на тежките изисквания на планинското и шосейно каране на дълги разстояния.
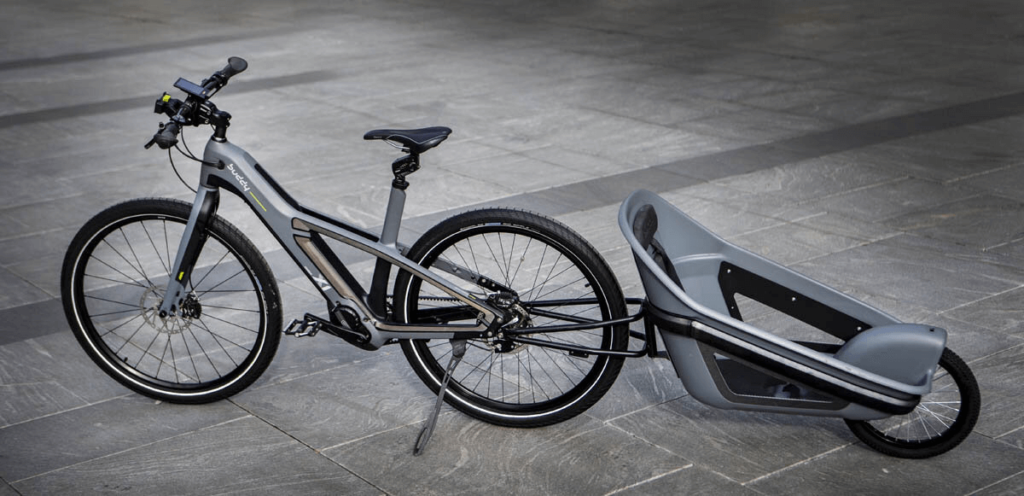
Велосипедът Isoco X1, разработен в сътрудничество с Lehvoss и Buddy Bikes. ( Снимка чрез Isoco Bikes).
Материалите на Lehvoss позволяват устойчиво производство на велосипеди
Разработването на ISOCO X1 започна миналата година, след като Lehvoss подписа ексклузивно споразумение с Isoco Bikes и производителя на рамки за велосипеди V Frames за въвеждане на подсилени с влакна съединения в производството на велосипеди.
Като част от това споразумение V Frames се надява да постигне масово производство на шприцовани рамки, вилки, пилотски кабини и други компоненти за няколко OEM производители до 2027 г. Компанията цели производствени обеми от 1 милион компонента в завода на Isoco в chmiedefeld, Thuringia.
Isoco твърди, че неговата технология за леене под налягане WIT вече може да произвежда до 1000 рамна ден, достигайки 3 милиона части за крайна употреба годишно.
Това не е единственият път, когато материалът на Lehvoss е използван за производството на крайни велосипедни компоненти. Германският производител на велосипедни седла BLOBBER използва термопластичните материали на Lehvoss за 3D отпечатване на своите велосипедни седла.
Материалът LUVOTECH eco PA GF15 HS BK на Lehvoss се използва за производството на опорната структура на седлото. В допълнение, вътрешната решетка е 3D отпечатана от LUVOSINT TPU, което позволява персонализирано омекотяване.
Продуктите BLOBBER са проектирани да предложат оптимален комфорт при колоездене и се смята, че са първите въздушни седалки, които включват двукамерна система и интегриран 3D елемент за амортизиране на налягането. Тези функции са предназначени да осигурят равномерно и бързо разпределение на въздуха, поддържайки естественото движение на махалото при колоездене.

Седло за велосипед BLOBBER. Изображение чрез BLOBBER.
3D отпечатани велосипеди
Проучване за бъдещето на 3D печата подчерта, че използването на адитивно производство нараства в рамките на потребителския пазар и производството на крайни продукти.
Това е тенденция, която вече може да се види в производството на велосипеди от висок клас. През 2022 г. базираната в Обединеното кралство инженерна фирма Renishaw разшири партньорството си с уелския производител на велосипеди по поръчка Atherton Bikes, за да развие собствените си възможности за 3D печат.
Производителят на велосипеди възприе допълнителна собствена производствена технология, за да увеличи издръжливостта на своите велосипеди, спечелили Световната купа, и да намали времето за производство на части. Atherton Bikes инвестира в RenAM 500Q за 3D отпечатване на металните компоненти на велосипеда, които включват титанови накрайници за неговите рамки.
Преди това Renishaw си сътрудничи с Great British Cycling Team, Lotus Engineering и Hope Technology за разработването на частично 3D отпечатан пистов велосипед за Олимпийските игри в Токио 2020 г.
През 2022 г. производителят на велосипеди Canyon дебютира и с концептуален 3D отпечатан прототип на планински велосипед, който имаше за цел да демонстрира по-устойчив метод за производство на велосипеди. Сътрудничейки със софтуерната компания за 3D печат Materialize , Canyon 3D отпечата рамката и вилката на велосипедите като част от кампанията „Ride Green“ на Bike Magazine Germany.
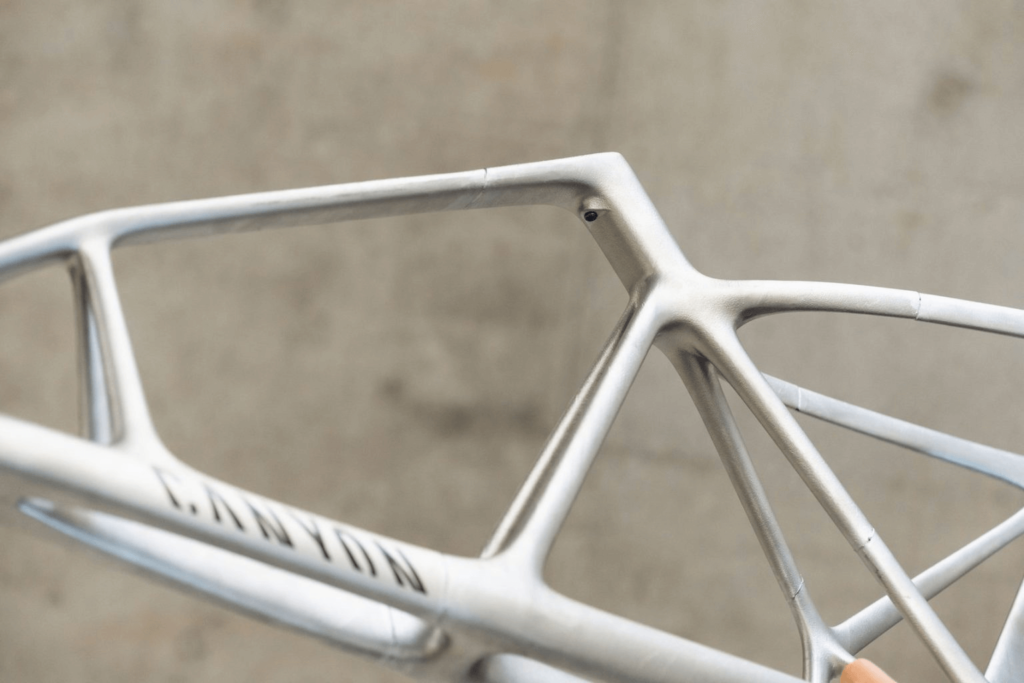
3D отпечатана велосипедна рамка на Canyon. (Снимка чрез Bike Magazine).
На друго място, лайфстайл марката Kimoa на бившия световен шампион от Формула 1 на Фернандо Алонсо пусна е-велосипед с 3D отпечатана велосипедна рамка . Рамката от едно тяло е проектирана така, че да може много да се персонализира, както и да е по-здрава и по-лека от компонентите, които са свързани с болтове.
Рамките бяха 3D отпечатани от 3D принтерите AQUA 3D на компанията Arevo за производство на добавки.
0 Comments