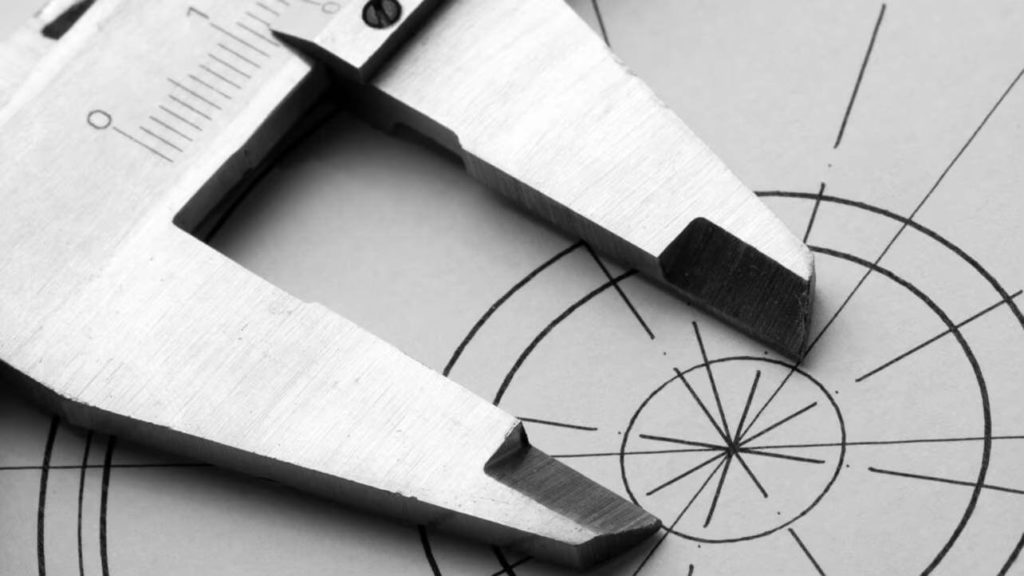
За инженерите толерантността е от решаващо значение. Научете как да сведете до минимум неизбежните неточности на 3D отпечатаните части.
При проектирането или производството на практични и функционални части, тяхната производителност често зависи критично от точните размери . Например, една линийка не би свършила работата си много добре, ако не беше права и маркирана на точни интервали. Две тухли Lego нямаше да паснат една на друга, ако размерите им не бяха подходящи, а дюзата за 3D печат нямаше да екструдира точно, ако диаметърът на отвора й беше неточен.
Допуските помагат да се избегнат тези видове проблеми, като се установява допустимото ниво на неточност на размерите. Допуските са инструкции от дизайнера към производителя за това, доколко даден размер може да се отклони от номиналното си обозначение, като се признава фактът, че перфектното производство на размери често е невъзможно да се изпълни.
Какво представляват толерансите?
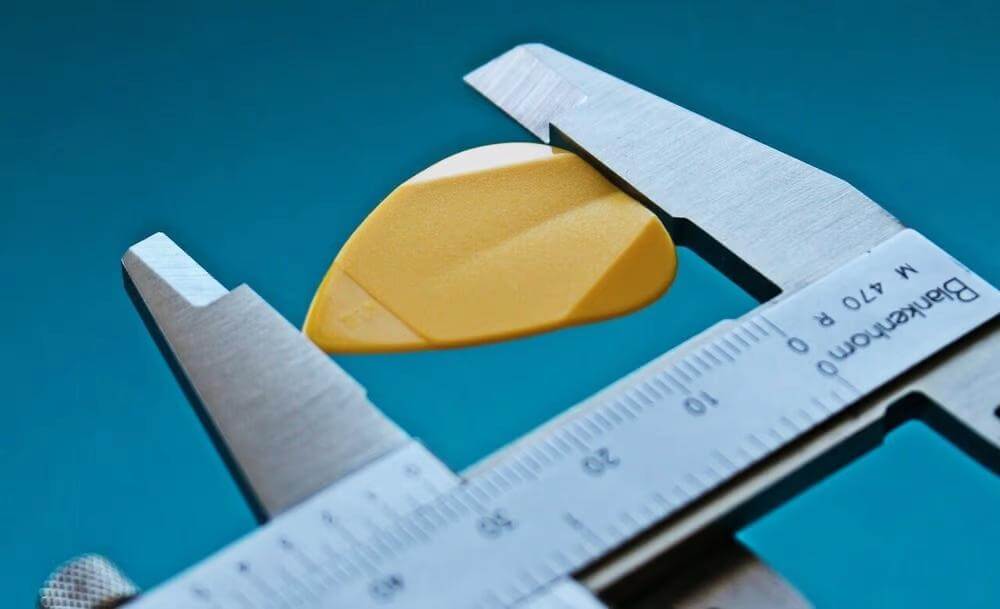
За нашите цели точността може да се дефинира като мярка за това колко близко е едно измерване до неговия „номинален“ дизайн. Например, ако дизайнът на частта казва, че тя трябва да бъде дълга 5 см, версия с дължина 5,01 см е по-точна от част с дължина 5,1 см. Очевидно част, която е с дължина точно 5.00000… cm, би била най-точна, но това обикновено не е възможно при повечето производствени процеси. Факт е, че нищо около нас не е точно ; реалистично всичко е малко по-голямо или по-малко от номиналния му дизайн. Количеството, с което варира, зависи от предназначението и метода на производство.
Начинът за преодоляване на този проблем е, както при всеки проблем, първо да се признае, тъй като едва тогава може да се намери решение. И начинът да се реши този проблем с измерването е да се проектира с допуски. За да се върнем към нашата част от 5 cm, ако толерансът е 0,1 cm, тогава всеки резултат от 4,9-5,1 cm се счита за приемливо точен. Естествено тогава, в допълнение към приспособяването на производствените неточности, задаване на толеранси означава също така да се гарантира, че частите ще функционират правилно навсякъде в този размерен диапазон.
Трябва да се отбележи, че допуските обикновено се отнасят за размерите на частите, а не за работата на машината. Величините, които определят разрешения обхват на работа на машината, се дефинират в метрологията като „точност“, „прецизност“, „повторяемост“ и т.н.
Сега, когато разбрахме какво представляват допуските, нека да разгледаме какво определя толерансите за част: пасване.
Видове сглобки
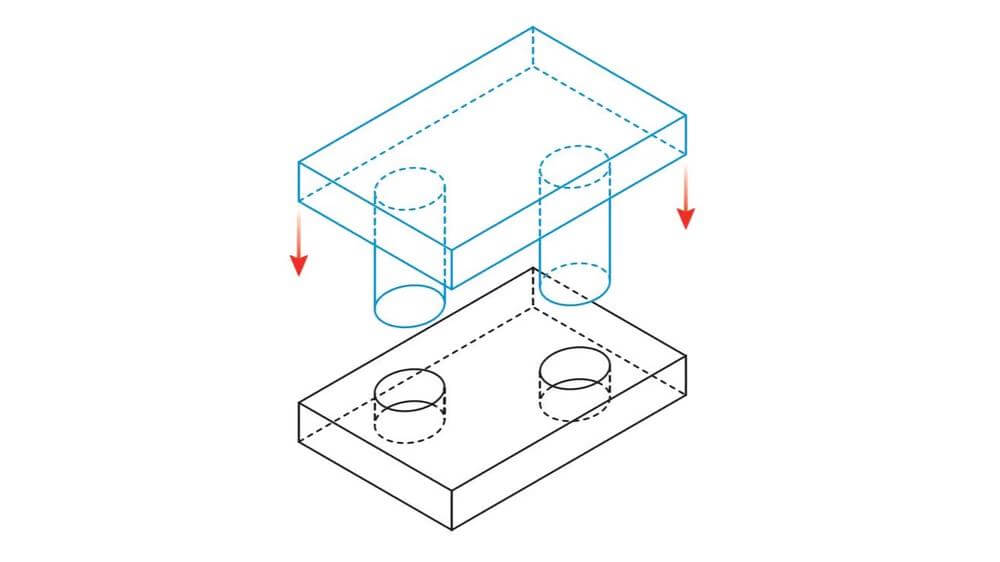
В повечето приложения фугата между две части трябва да изпълнява определена функция. Нека илюстрираме това с пример.
Помислете за кръгъл вал, проектиран с номинален диаметър 50 mm, който трябва да се побере в кръгъл отвор с номинален диаметър 50 mm. На практика има три варианта за това как тези две части могат да се съберат заедно:
- Диаметърът на вала е значително по-тесен от диаметъра на отвора, да речем съответно 49,8 и 50,2 мм. В този случай валът лесно ще се плъзга и излиза от отвора и ще се върти вътре в него. Това води до това, което е известно като хлабина .
- Диаметърът на вала е същият или малко по-широк от този на отвора, да речем съответно 50,2 и 49,8 мм. Валът няма да влезе в дупката без много сила и след като влезе, вероятно няма да излезе, без да счупят частите. Този тип напасване се използва широко, когато се изисква висока концентричност и взаимно движение (като закрепване на вал към лагер). Това е известно като интерференционно прилягане .
- Диаметърът на вала е малко по-малък от този на отвора, да речем съответно 49,9 и 50,0 мм. Валът ще влезе в отвора с минимално усилие и ще поддържа относителна концентричност. Това се нарича преходно сглобяване.
В действителност всеки от видовете прилягане е спектър от допустими комбинации; посочените по-горе размери са само примерни. За да изберете правилно прилягане и дизайн, има няколко международни стандарта (като ISO толеранс), но няма да навлизаме в това в тази статия.
Независимо от това, типът на сглобка трябва да се определи преди задаване на толерансите. Ако са правилно зададени, две взаимодействащи части ще продължат да функционират по предназначение, независимо колко близо са до положителните или отрицателните граници на обхвата.
Проблеми с 3D печат
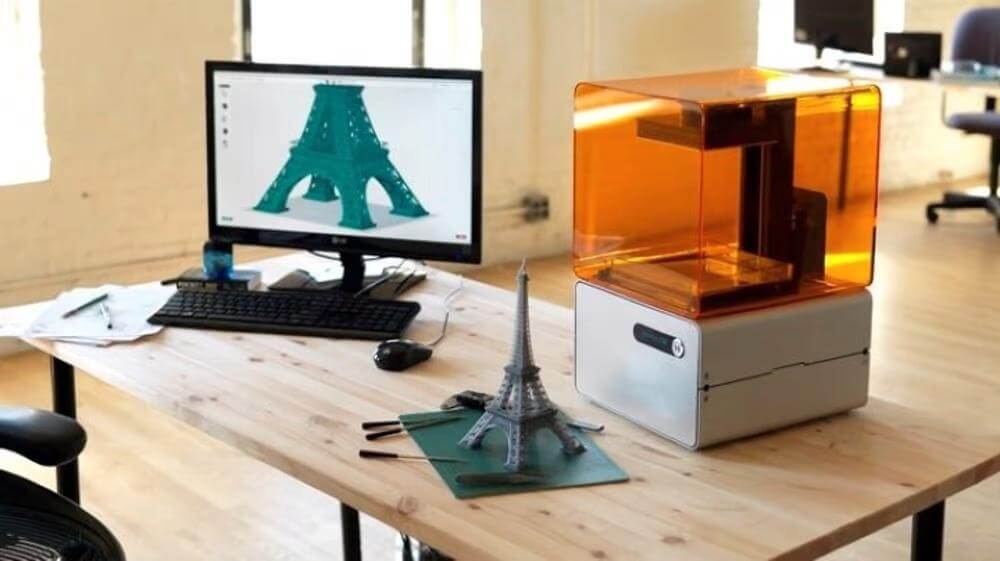
Видът на прилягането (и следователно размерите на монтиращите части) трябва да бъдат осъзнано решени, докато частта все още е във фаза на проектиране. Това, което най-много влияе върху точните стойности на посочените размери и толеранси, е методът на производство. Например, не можете да очаквате да получите сходни резултати с верижен трион, както с фино длето за дървообработване.
При 3D печата често има някои липсващи връзки от конвенционалния процес на проектиране и производство. Обикновено дизайнер проектира частите и ги предава на производителя с необходимите толеранси за частта. Тогава производителят носи отговорността да изпълни тези допуски. Въпреки това, при 3D печат, тъй като цифровият модел се експортира директно в STL и след това се отпечатва, всяка информация относно необходимите толеранси не се прилага в производствения процес. Нито резачката ( Slicer) , нито принтерът ще знаят допустимите отклонения от дизайнера. Това означава, че потребителят ще трябва да контролира както дизайна, така и процеса на печат, за да постигне необходимите толеранси.
Причини за неточности на FDM
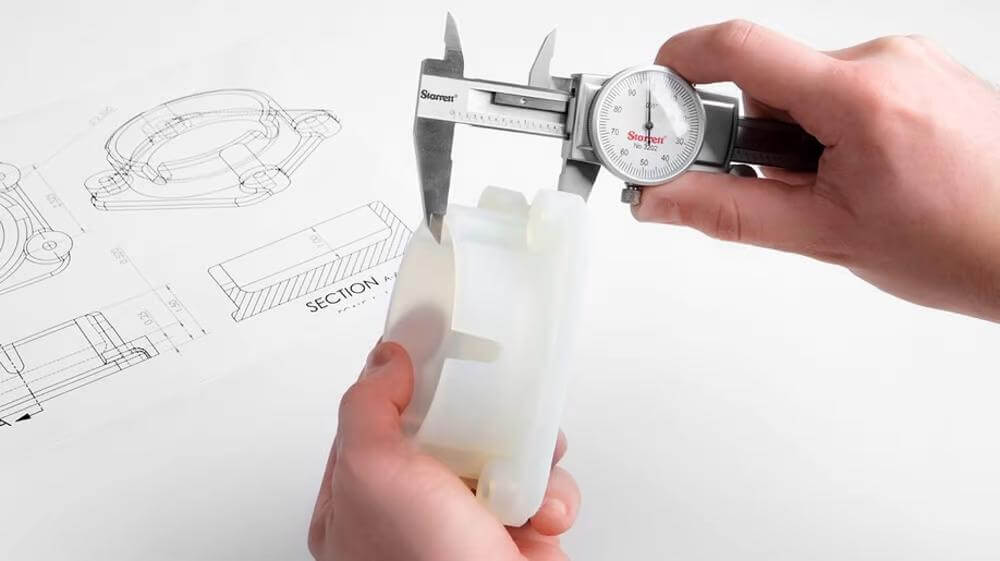
Освен грешки в дизайна (които са ендемични за всеки производствен процес), има няколко ключови причини за неточности, които са присъщи на 3D печат, и по-специално на FDM машини.
СОФТУЕРНИ ГРЕШКИ
Когато цифров модел се преобразува в STL , някои детайли неизбежно се губят. Например, кръгли обекти са фасетирани и преобразувани в прави повърхности и върхове. Въпреки това, колкото по-висока е разделителната способност на преобразуване, толкова по-малка е грешката в размерите, причинена в детайла.
Слайсерите може да въвеждат свои собствени грешки в зависимост от техните специфични алгоритми и настройки. Начинът, по който слайсерите интерполират върховете на STL файл, ще повлияе значително на това как ще изглежда G-кодът и следователно как ще се държи принтерът.
МАШИННИ НЕТОЧНОСТИ
Има няколко начина, по които самият 3D принтер може да причини неточности в отпечатана част. Стъпковите двигатели имат ограничена разделителна способност, така че точността на пътя на движение е толкова точна, колкото и максималната разделителна способност на двигателите. В допълнение, типичните двигатели за FDM 3D печат нямат контур за контрол на позицията, така че малки грешки в позицията могат да се натрупват при дълги задания за печат. Повечето драйвери на мотори също имат функция за термична защита, която ги спира да работят, ако прегреят, което може да накара двигателя да пропусне стъпки. Е-стъпките на стъпковия двигател също са решаваща мярка, която може да причини неточност на размерите, ако не е калибрирана правилно.
Ако осите на принтера не са адекватно ортогонални една спрямо друга, ще се появят структурни неточности. Представете си, че се опитвате да нарисувате правоъгълник с ос, която не е перпендикулярна – в крайна сметка ще получите успоредник. След това, всеки път, когато оста на движение промени посоката, ще има малко луфт. Колкото по-малко е напрежението в ремъчната система , толкова по-изразен е хлабината. Ремъците също така въвеждат други проблеми с времето, като пълзене и удължаване, които не само намаляват точността, но също така могат да причинят приплъзване и липсващи стъпки.
Тъй като принтерът отпечатва линия от нишки, се очаква да създаде еднаква ширина. Въпреки това, началото на линията за печат може да бъде по-тънко и да се разшири до края на линията с увеличаване на налягането на дюзата. Това може да е преувеличено при завой. Общото свръхекструдиране на нишката също ще доведе до по-широка линия на печат, което може да доведе до твърде голям размер, с обратен ефект за недостатъчно екструдиране , а качеството и състоянието на нишката може да доведе до допълнителни проблеми с екструдирането.
И накрая, неправилната първоначална Z височина може да причини „ крак на слон “, когато първият слой се разпространи по-широко от следващите слоеве.
Дизайнерски решения
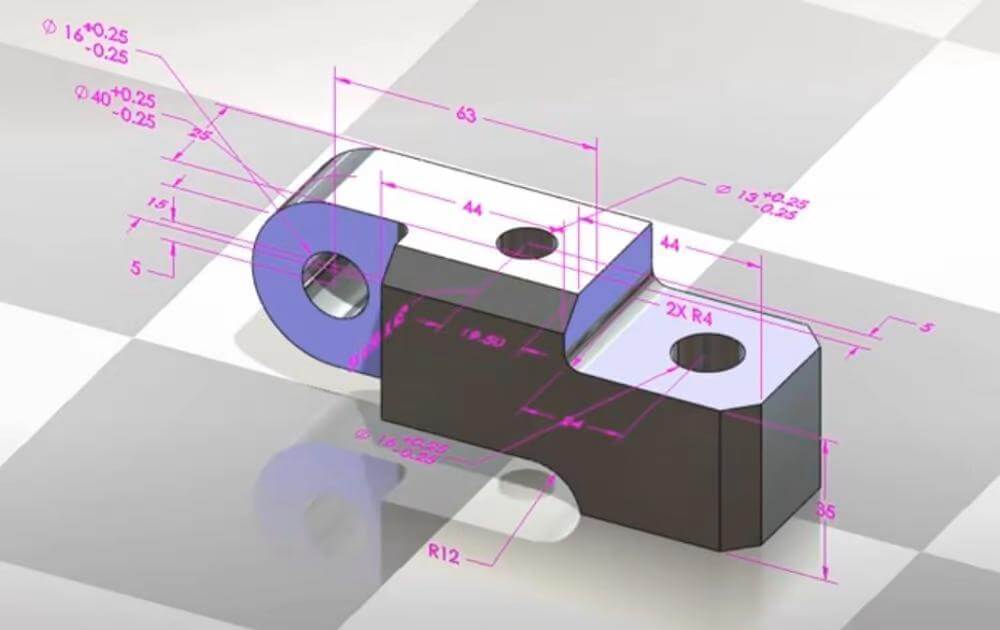
След като разберете възможните причини за неточности във вашите разпечатки, можете да вземете активни предпазни мерки, за да ги елиминирате възможно най-добре. На практика не можете да очаквате обикновен FDM принтер да закове в размер до 100 микрона. Това означава, че всички ваши размери трябва да бъдат проектирани с допускането, че може да излязат по-големи или по-малки с тази стойност.
При сглобяващи се части ще трябва да ги проектирате така, че дори и с неконтролирана грешка в размерите, те все още да работят заедно, както е проектирано. В почти всички случаи това ще означава, че ако имате две части, които трябва да паснат заедно, ще трябва да проектирате една част, по-малка от другата. За стандартна дюза от 0,4 мм, ето общи основни правила за пасване въз основа на съединение на дупка и вал, въпреки че ще трябва да експериментирате и да научите действителните стойности за вашия принтер.
- Хлабина: Разлика от 0,5 mm и повече между диаметъра на отвора и диаметъра на вала. Това води до теоретично разстояние от най-малко 0,25 mm между вала и отвора.
- Преходно прилягане: Разлика от 0,15-0,4 мм между диаметъра на отвора и диаметъра на вала. Това води до теоретично разстояние от 0,08-0,2 mm между вала и отвора.
- Интерференционно прилягане: Разлика от около 0,1 mm или по-малко между диаметъра на отвора и диаметъра на вала. Това води до теоретично разстояние от 0,05 mm или по-малко между вала и отвора.
Тъй като тези правила се отнасят до разликата между частите, те могат да се използват и за нецилиндрични части. Когато разглеждаме нецилиндрични съвпадащи части, като квадратен отвор и съответна квадратна издатина, гореспоменатите правила могат да се прилагат за разликата между най-близките равнини на сглобяване. Например, за да получите хлабина, подходяща за 30 мм квадратен прът, проектирайте отвора така, че да се поддържа междина от 0,25 мм (т.е. квадрат от 30,5 мм).
Друга ключова насока е да се вземе предвид ориентацията на частта , така че да може да се постигне максимално качество. Отворите се отпечатват най-добре хоризонтално (успоредно на равнината XY на принтера). Ако трябва да отпечатате вертикален отвор, използвайте техниката на сълза , при която горната част на отвора е проектирана в заострена форма, а не напълно кръгла. Това елиминира всякакви неточности, причинени от надвисването на нишката при затваряне на горната част на отвора.
В допълнение, поради многослойната природа на FDM 3D печата, вертикалните характеристики обикновено са по-малко точни, тъй като могат да бъдат толкова фини, колкото височината на слоя. Хоризонталната (XY) функция обикновено е по-точна, тъй като те са ограничени само от разделителната способност на стъпковите двигатели и ремъка, както е обяснено в предишните раздели.
Софтуерни решения
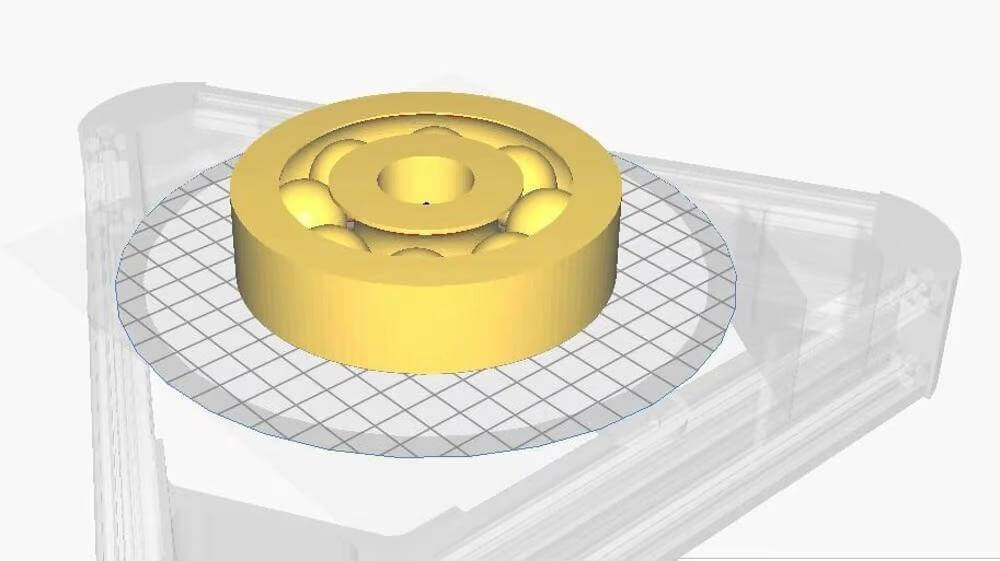
Има няколко софтуерни решения, които могат да помогнат за увеличаване на точността на вашите разпечатки. Когато режете част за отпечатване с максимална точност, обикновено трябва да използвате по-бавна кинематика (скорост, ускорение и ритъм), по-малки височини на слоя и активно охлаждане на частта. Препоръчваме скорост на печат под 60 мм в секунда, ускорение по-малко от 3000 мм 2 /сек. и рязко движение по-малко от 15 мм / сек. за повечето настолни принтери.
В настройките на слайсера има и някои уникални функции, които могат да помогнат за подобряване на точността на размерите. Следните примери са за Cura, но повечето резачки имат подобни характеристики.
- Outer before inner walls /Външни преди вътрешни стени/: Като отпечатате първо външните стени, теоретично можете да подобрите точността на размерите, като не бъдете удряни от вътрешните стени или пълнежа.
- Coasting /Инерция/: Тази функция кара принтера да спре да екструдира към края на движение и вместо това да разчита на остатъчното налягане в дюзата, за да отпечата останалата част от нишката за преместване.
- Horizontal expansion /Хоризонтално разширяване/: С тази функция можете да увеличавате или намалявате всички размери на част с определен процент. В идеалния случай това може да помогне за фина настройка на размерите на отпечатъка, но наистина е полезно само ако целият отпечатък е твърде малък или твърде голям. Ако общите размери на отпечатъка са приемливи и трябва да се коригират само дупки, например, трябва да се използва различен метод, като функцията “Hole horizontal expansion” /„Хоризонтално разширяване на отворите“/.
След нарязване, функцията linear advance в Marlin и някои друг фърмуер регулира потока на нишката според предвидените движения на печат. Функцията за линейно изпреварване предвижда промяната в налягането на дюзата, която може да доведе до непоследователно екструдиране, и го коригира съответно. Това преобразува непостоянната ширина на линията в по-равномерна линия, което подобрява точността на размерите на отпечатъка.
Linear advance има подобен ефект на настройките за инерция във вашия слайсер, но като цяло е по-лесен за настройка. За да използвате тази функция, ще трябва да я активирате в началото на процеса на печат и да предоставите K стойност, за да зададете колко принтерът трябва да регулира потока (тази стойност може да бъде намерена експериментално).
Машинни решения
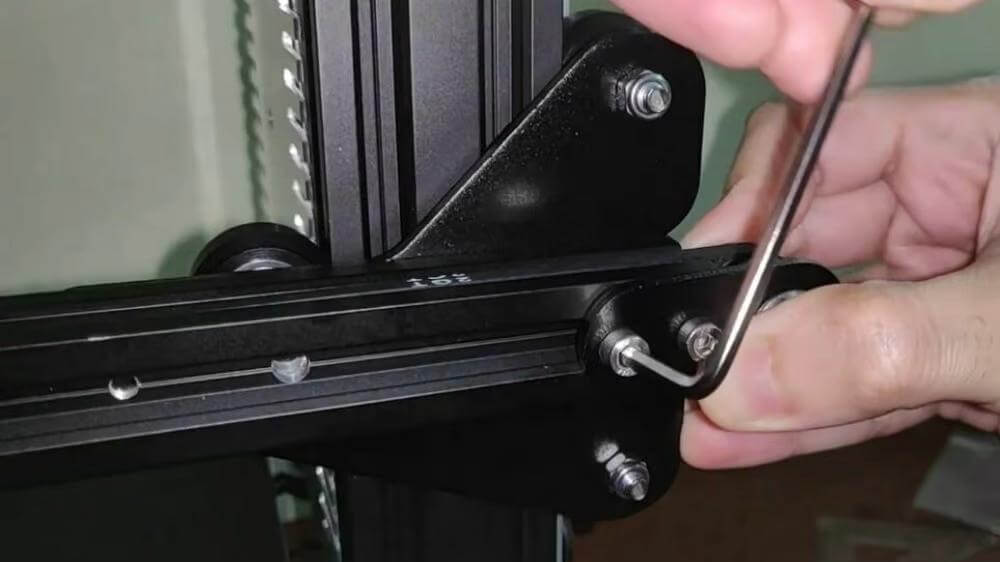
Може би най-важният начин да постигнете максимална точност на печат и да останете в рамките на толеранса е чрез калибриране на принтера. Лошо калибриран принтер ще доведе до части, които не са прави, нямат правилните размери и не пасват една на друга. На всичкото отгоре, винаги помнете, че нито един хоби клас настолни 3D принтери не е идеално и напълно калибриран от самото начало, дори ако се доставят предварително сглобени; те ще изискват допълнително калибриране с течение на времето, като обичайна операция по поддръжка. Машините на професионално ниво може донякъде да компенсират това, но все пак се нуждаят от редовна поддръжка и калибриране.
Тъй като лошото калибриране може да направи всичките ви усилия за проектиране и нарязване напразни, важността на машинното калибриране не може да бъде подценявана. Най-важните елементи за калибриране са екструдерът и Е-стъпките, и винаги е жизненоважно да започнете с добър първи слой .
Също така е важно да изберете дюзи и нишки с добро качество , тъй като точността на размерите на вашата част до голяма степен зависи от предположението, че екструдираната нишка всъщност е с диаметърът, който трябва да бъде. Значителни отклонения в диаметъра на нишката или износени дюзи ще окажат незабавно влияние върху възможните толеранси на вашите отпечатъци.
Решения за последваща обработка
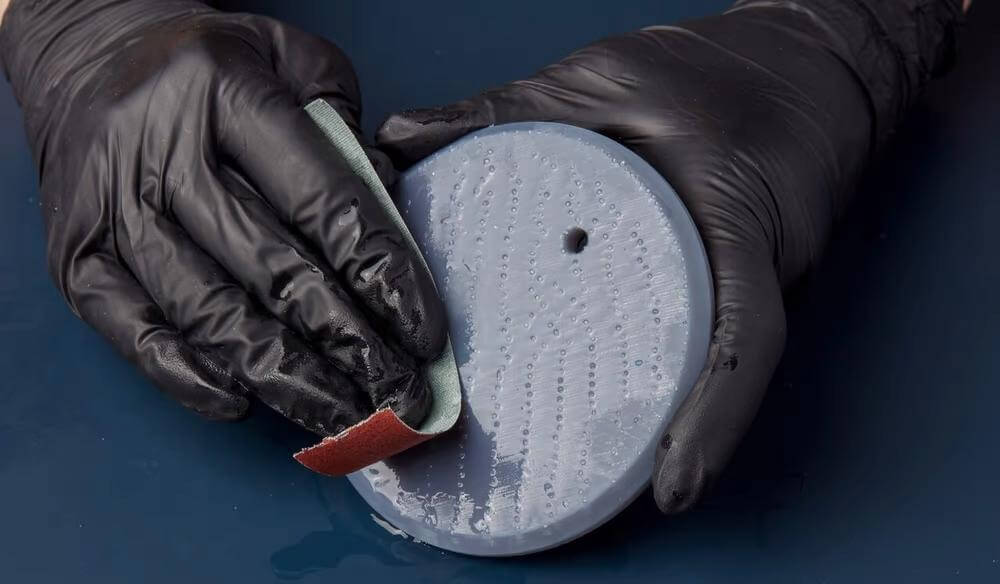
Дори след цялото калибриране, правилния дизайн и специалните конфигурации за нарязване, понякога частите все още ще са извън толеранса. В този случай те ще трябва да бъдат приведени в съответствие чрез последваща обработка.
Няма срам да приемете необходимостта от последваща обработка на част. Дори с изключително точни центрове за обработка с ЦПУ, които струват стотици хиляди долари, понякога е необходимо да се извърши известна последваща обработка на частите, за да се пригодят и да отговарят на спецификациите.
Важно е да се отбележи, че последващата обработка обикновено се отнася до методите на отнемане, така че обикновено е по-подходящо за части, които са с големи размери, отколкото с по-малки. Ето няколко ключови съвета, за да сведете частите си до проектираните размери.
- Продължете да измервате частите, докато ги обработвате, докато достигнете желаните размери.
- Пробийте или калибрирайте всеки 3D отпечатан отвор.
- Опитайте се да избягвате опори, ако е възможно. Много по-лесно е да пробиете отново дупка, отколкото да се опитате да извадите малки опори с чифт клещи.
И накрая, в един момент трябва да признаем, че определени изисквания за геометрични размери и толеранс (GD&T) не могат да бъдат лесно изпълнени на ниво „Направи си сам“.
0 Comments