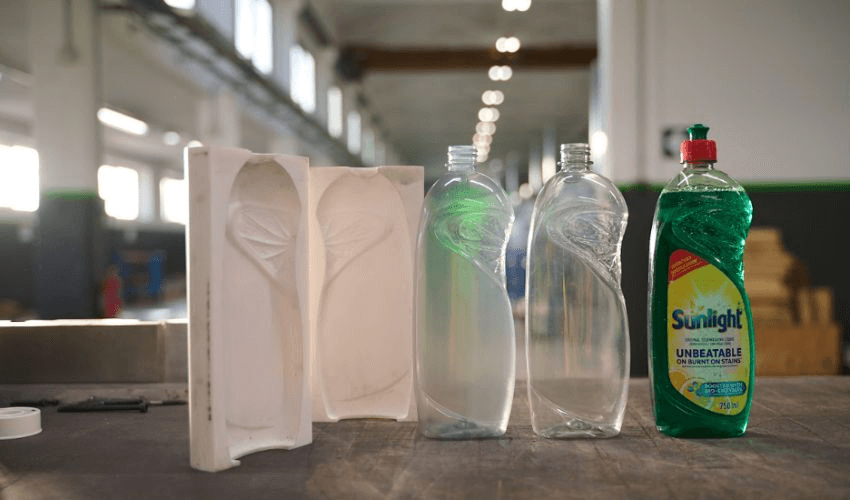
Една по-малко обсъждана област, в която наблюдаваме растеж на 3D печата през последните години, е опаковъчната индустрия . С пазар, оценен на $1,21 милиарда през 2023 г. и се очаква да нарасне до $2,56 милиарда до 2023 г., според Future Market Insights, през последните години виждаме все повече и повече големи имена, включително L’Oréal и Pepsi , които се обръщат към адитивното производство. Сега имаме още един, който да добавим към списъка, Unilever, който се обърна към 3D печат на смола от Formlabs, за да направи форми за пластмасови бутилки.
Може би не сте чували за Unilever преди. Определено обаче сте чували за някои от продуктите и марките на британската компания, включително Axe, Ben & Jerry’s, Dove и Knorr, сред много други. Конгломератът за бързооборотни потребителски стоки (FMCG) е най-големият производител на сапун в света, с продукти, предлагани в над 190 страни. Все пак секторът на бързооборотните стоки има ожесточена конкуренция и поради това Unilever непрекъснато търси начини за иновации, включително този последен ход за използване на 3D печат за бутилки.
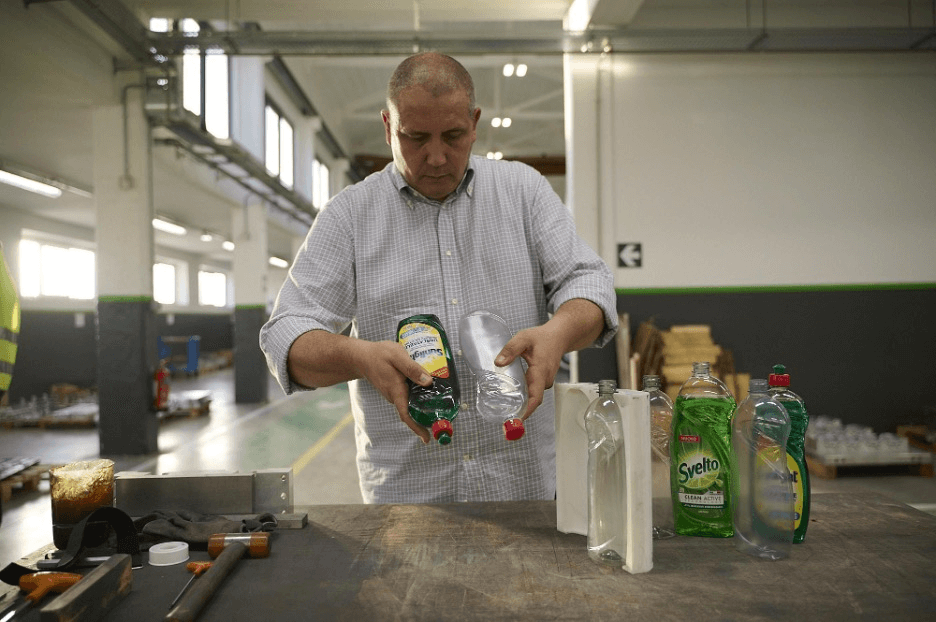
Сравняване на прототипи на бутилки, направени с помощта на 3D отпечатана форма
Stefano Cademartiri, собственик на CAD & Prototyping, Unilever, допълва: „Компания за потребителски стоки като Unilever трябва да бъде на пазара възможно най-скоро или преди вашите конкуренти. Трябва да предложите на потребителите най-добрия продукт на най-добра цена за възможно най-кратко време. 3D принтирането ни помага да ускорим този процес.“
Как Unilever използва 3D печат за производство на бутилки?
Традиционно правенето на обикновена пластмасова бутилка отнема много повече време, отколкото бихте очаквали. От проектирането до крайния продукт, включително правенето на форми преди преминаване към формоване с раздуване, често отнема месеци. Освен това има малка възможност да се изпробват различни прототипи и дизайни поради времето, необходимо за създаването на само една форма, което се оценява на около 6–8 седмици.
Чрез интегрирането на 3D печат в процеса, това драстично намалява, тъй като 3D отпечатана форма може да бъде завършена само за два дни, което води до пилотно тестване само за две седмици, като същевременно струва значително по-малко. Flavio Migliarelli, мениджър дизайн на R&D, Serioplast Global Services, обяснява още: „С 3D отпечатаната форма можем да спестим до 70% време и 90% разходи в сравнение със стандартната форма. В миналото [клиентите] трябваше да чакат до 12 седмици само за един дизайн, сега можем да направим пет дизайна.“
Както трябва да е ясно, 3D печатът в този случай се използва заедно с по-традиционни методи. По-конкретно, формите се създават с помощта на 3D принтер Form 3L от Formlabs и Rigid 10K Resin, което позволява прецизни форми с гладка повърхност, като същевременно може да издържи на вътрешно налягане и температура. Използването на SLA също помогна на Unilever да интегрира повече детайли в бутилките, като лога и други фини детайли излизат добре.
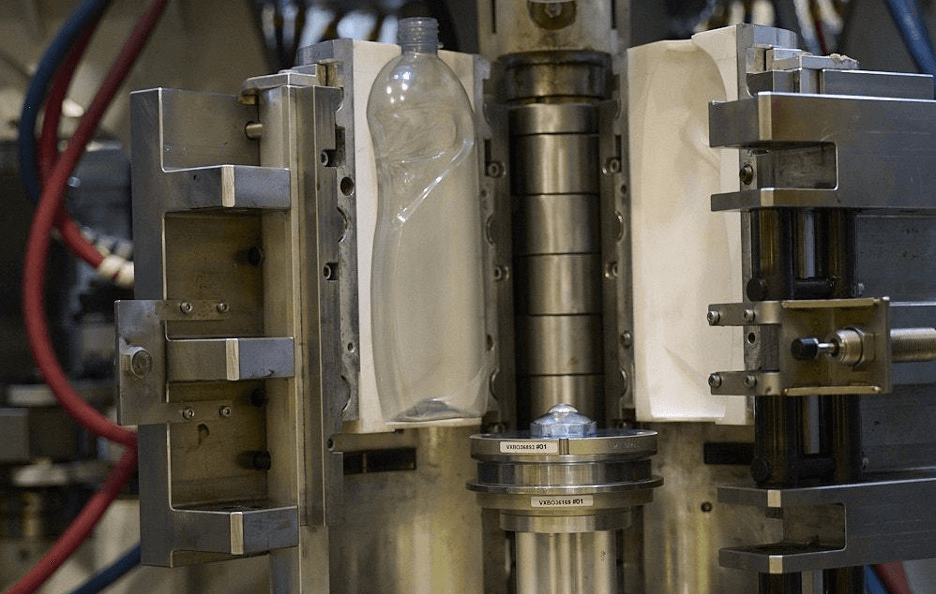
3D отпечатаната форма е прикрепена към метален апарат и след това може да се използва заедно за създаване на пластмасови бутилки
След създаването на матрицата, бутилките могат да бъдат направени чрез формоване чрез раздуване, в този случай формоване с раздуване с разтягане (SBM), което обикновено се използва за създаване на висококачествени, прозрачни като стъкло PET контейнери. Приложенията за комбинация от тези технологии включват тестване на аспекти на производствената линия в ранен етап благодарение на сходството на бутилките с крайния продукт, валидиране на процеса SBM и PET заготовката и ускоряване на прототипирането.
Може да намерите принтерите и материалите на Formlabs и при нас. Изпилвайте линка за по-лесно:
https://shop.3mgbonev.com/category/3d-printeri-formlabs
*Всички снимки: Formlabs
0 Comments