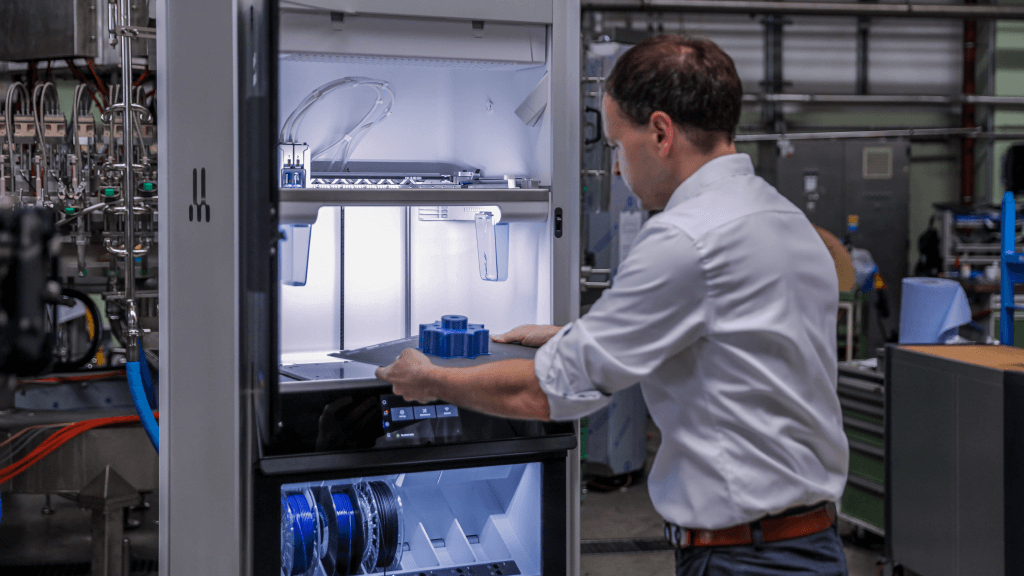
Акценти в UltiMaker Factor 4: Директно задвижване и гъвкавост
...
Проектиране, моделиране, отпечатване и сканиране - експертно изпълнение на вашите 3D проекти от 3MG Bonev Ltd.
Основани през 2019г.
С над 5 години опит в областта на 3D технологиите
3MG Bonev Ltd. е създадена през 2019г. и е специализирана в областта на 3D технологиите за принтиране. Ние предоставяме цялостни решения в 3D проектирането и моделирането, 3D отпечатването и довършителните процеси, както и 3D сканирането и реинженеринга.
Нашият екип от професионалисти е посветен на това да предоставя най-високо качество на услугите и продуктите, които предлагаме. Работим с най-новите технологии и материали, за да гарантираме отлични резултати за всеки проект.
Прецизност и внимание към детайла във всеки проект
Използваме най-новите технологии в областта
Специалисти с богат опит в 3D технологиите
Доверието на клиентите е нашият приоритет
3MG Bonev Ltd. предоставя цялостни решения в 3D проектирането и моделирането, 3D отпечатването и довършителните процеси, както и 3D сканирането и реинженеринга.
CAD или компютърно проектиран дизайн e използването на компютърен софтуер за проектиране на физически обект, част или продукт. CAD ни позволява да изградим модел в неговата цялост, във въображаемо пространство.
Ние предлагаме програма за завършване на дизайна, в която можем да съставим вашите изисквания или просто да изработим и принтираме Вашият дизайн.
Нашата услуга за 3D сканиране е бързият и точен начин за 3D заснемане на физически обекти. Лесно можем да сканираме 3D малки и големи елементи, запазвайки всички детайли.
3D печат ви позволява да отпечатвате обекти, включително фигури, прототипи и други. 3MG Bonev Ltd. предлага един от най-добрият 3D печат с качествени материали.
Предлагаме последните модели 3D принтери от водещите световни производители.
Следете нашия блог за новини, съвети и задълбочени анализи от света на 3D технологиите.
...
...
Ford Motor Company е използвала SLA и SLS 3D принтери от Formlabs, за да създаде прототип на няколко компонента за своя ...
Получавайте последните новини, съвети и специални предложения директно във вашата пощенска кутия.
Ние уважаваме вашата поверителност. Можете да се отпишете по всяко време.
Ние си сътрудничим с най-добрите в индустрията, за да предоставим високо качество на услугите и технологиите, които предлагаме.
Имате въпроси относно нашите услуги или искате да обсъдите вашия проект? Свържете се с нас и ще ви отговорим възможно най-скоро.
ул. Жорж Папазов No14, кантора 407
Ямбол, България
Понеделник - Петък: 9:00 - 18:00
Събота: 10:00 - 14:00
Карта се зарежда...